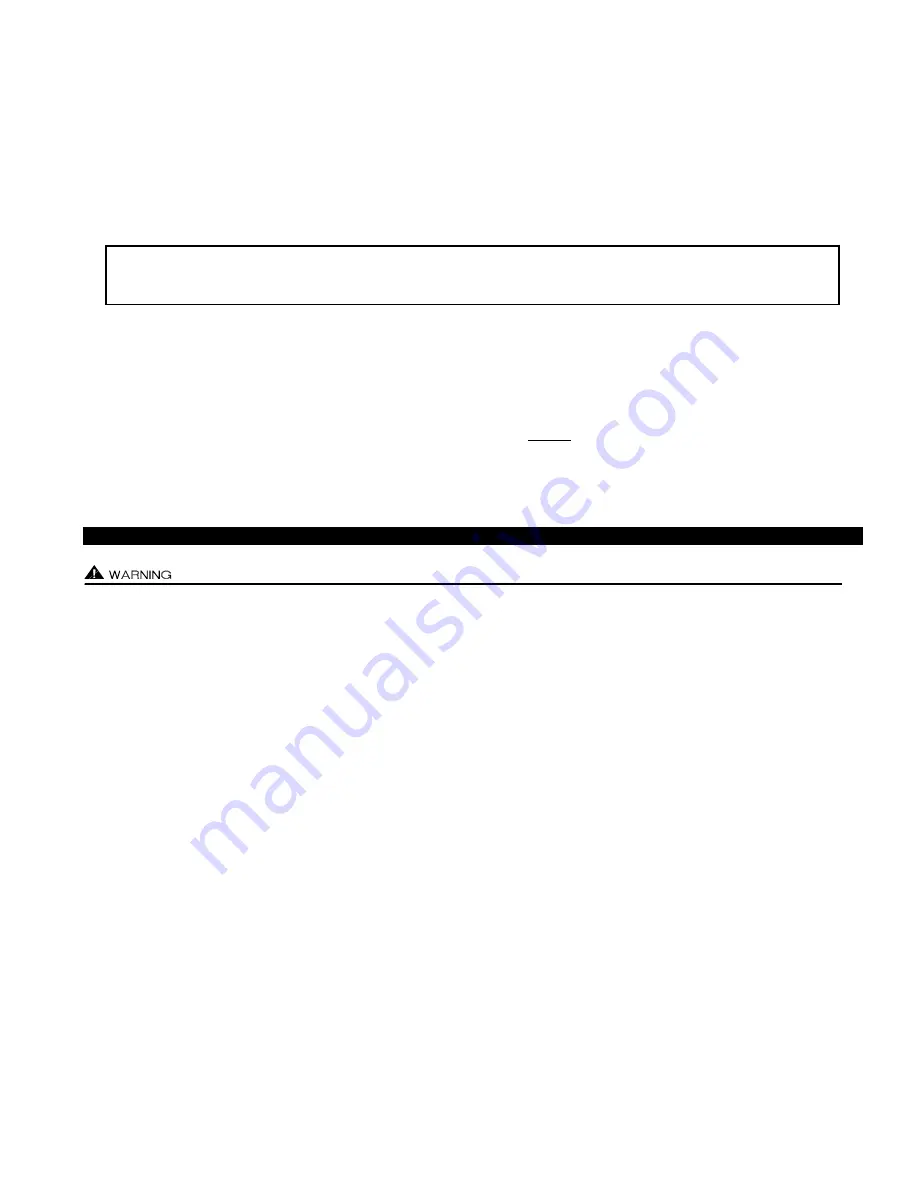
Draft Adjustment:
The SS1R Draft Adjustment, located outdoors on the Vent Hood, has two functions: A) It allows the installer to
adjust the amount of draft in accordance with the draft adjustment chart that the SS1R must develop to vent the specific appliance,
and B) During the off-cycle, when the SS1R is off, it prevents air infiltration caused by strong winds and gusts. Air infiltration back
through the vent system will bring with it the odors from the flue gas residue on the inside of the vent pipe. When the Draft
Adjustment is at an inward setting (lower number) the Vent Hood will deflect a greater volume of wind than at a higher setting.
(
REMINDER :
The most significant preventer of wind-induced air infiltration is choosing a proper termination location of
the SS1R before installation, see requirements on pages 5, 6, 7 under "Vent Hood Termination Clearances.")
V
Verify that the Draft Adjustment is appropriate for the BTU/hr input, as shown on the "Draft Adjustment Chart," page 15. If neces-
sary, change setting by loosening both nuts on each side of the Vent Hood and center both indicators to the desired setting.
Tighten the four nuts to secure new Draft Adjustment.
Burner Adjustment:
Verify that the over-fire draft matches that recommended by the heating equipment manufacturer. Adjust the
combustion efficiency and smoke characteristics to optimum levels of performance.
Combustion Air:
Modern construction methods and materials have reduced natural air infiltration rates to extremely low levels.
Even older homes can lack adequate air for combustion, when insulation upgrades and other weatherization methods have been
installed.
It is recommended that fuel burning appliances have dedicated sources of outside air for combustion. This may be simply accom-
plished by running a properly sized duct from outdoors and terminating it near the burner air intake. Accessory air intakes are
available that connect to the burner motor, using it to pull in the outdoor air. The Tjernlund IN-FORCER
TM
Combustion Air Intake
tempers the raw outdoor air as it is delivered to the burner. Without a source of outdoor air for combustion, a tight home's negative
pressures will draw odors back through the venting system during the appliance off cycle.
TROUBLESHOOTING ELECTRICAL PROBLEMS
The following guide is intended to be used if a problem occurs during the use of the SS1R sidewall vent system. It may be
necessary to measure voltage during troubleshooting.
Extreme caution must be exercised to prevent injury.
If you are
unable to determine the defective part with the use of this guide, call your Tjernlund distributor or Tjernlund Products direct
at 1-800-255-4208 for further assistance.
LED STATUS & FAULT INDICATORS
LED INDICATOR LIGHTS
LED #1 (Amber) Appliance call for heat.
LED #2 (Blue)
Safety circuit through P1 & P2 (SS1R Limit & Fan Prover). Indicates SS1R Limit & Prover are closed during run cycle.
Oil solenoid valve is energized with Interlock Relay contact closure from terminal 3 to 4.
LED #3 (Green)
Power switched to SS1R motor & burner motor from L to MTR & M.
LED #4 (Red)
Status / Fault indicator.
LED #5 (Red)
Used as a status indicator.
LED #6 (Red)
115 VAC power supplied to board.
LED STATUS INDICATORS
LED #4 & #5 (Red) Flashing Alternately
= Venter in Pre-purge. (Pre-Purge options 0, 5, 20, 35 seconds)
LED #4 & #5 (Red) Flashing in Unison
= Venter in Post-Purge. (Post-Purge options 0, 30 seconds or 1, 2, 4, 8, 16 minutes)
LED #4 Flashing Continuously*
= Fan Prover opened for more than 10 seconds during burner cycle.
(Venter will run for 10 minutes, attempting to make Fan Prover)
LED #5 (Red) Flashing Intermittently
= With no call for heat, flashes 3 seconds on / 3 seconds off if microcontroller is working properly.
LED FAULT INDICATORS
Fault conditions are indicated by counting the number of times LED #4 (Red) flashes.
LED #4 Flashes 2 Times
Fan Prover was in electrically closed position prior to venter operation.
LED #4 Flashes 3 Times*
Fan Prover does not close within 60 seconds after call for heat.
LED #4 Flashes 4 Times*
Fan Prover did not re-close after 10 minutes of Venter operation.
LED #4 Flashes 5 Times*
Fan Prover opened for more than 10 seconds during burner cycle but closed within 10 minutes.
* Investigate causes of Fan Prover not making, i.e; Firing burner at capacities or temperatures exceeding Venter limits, excessive
vent pipe runs, high winds, plugged / kinked Fan Prover sensing tube or a faulty Fan Prover. Reset SS1R High Limit. If Limit
was tripped and SS1R fires, investigate cause of high heat.
IMPORTANT
Any adjustment to the draft setting must be followed by an over-fire draft measurement and necessary adjustments to the
primary air intake on the burner and barometric draft control. See Draft Adjustment Procedure on pages 14, 15.
16