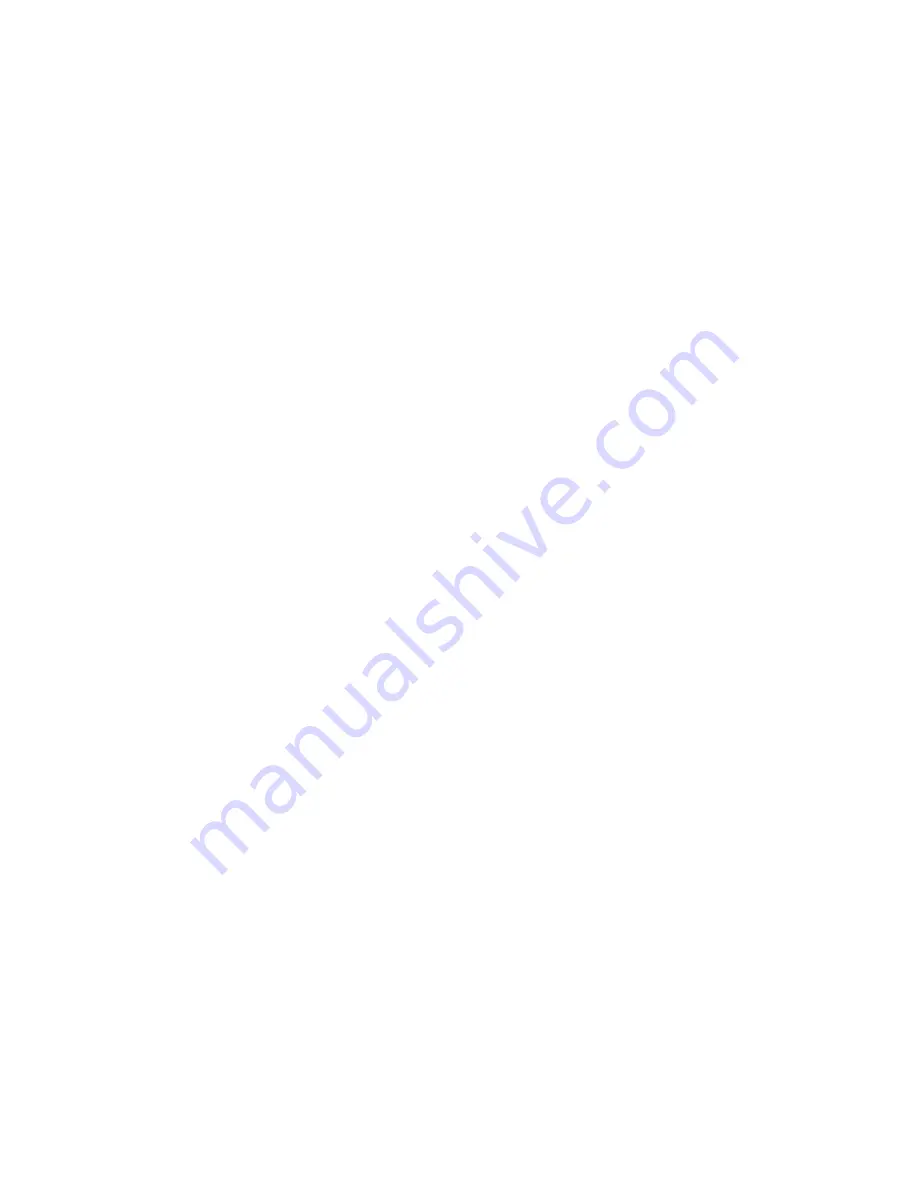
7
interaction between the rotor and the magnetic field tries to
align the rotor with the field. Thus, the SHORT-STOP
actually drives the rotor to zero speed.
A further feature is that the retarding torque is proportional
to the field strength, and hence to the braking current. By
varying the braking current, the braking strength can be set
to any desired value.
9.2
Operation
When any START button is depressed, the motor will start
instantly, provided a brake cycle is not in progress.
Starting the motor primes the brake.
When the STOP button is depressed and the starter
contactor is released, the SHORT-STOP will begin
braking the motor, after a short delay.
The length of the brake cycle is determined by the Time
control, and the amount of braking is determined by the
Torque control.
If Terminals B and Y are closed during a run to brake
transition, the brake will not activate and the motor will
coast to a stop.
10.
IF YOU HAVE A PROBLEM
10.1
Preliminary Checks
No adjustments are provided or required other than those
described in Section 8.
Should a system fail to perform properly, be sure to check
the wiring first. Also, be certain that the power line
voltage is present and correct. For instance, there should be
equal voltages between any two leads of a three-phase
power line, and these should be in the correct nominal
range for the SHORT-STOP.
If the system has previously been operating properly, it is
also a good idea to check fuses, and that the adjustments of
the two controls - TIME and TORQUE - have not been
tampered with.
If there is a problem on initial installation, or if the brake
should fail to function properly, the following checks
should be made:
[A]
Check that TIME and TORQUE controls are set
properly, and are not at minimum.
[B]
Verify that the SHORT-STOP rated motor voltage is
present at Terminals 5 and 6 WHEN THE MOTOR
RUNS. If there is NO voltage at 5 and 6 with the
motor running, the unit is installed incorrectly.
[C]
Verify that there is normal line voltage (SHORT-
STOP rated voltage) across Terminals 1 and 2, and
that there is AC voltage at the output of the control
transformer in the SHORT-STOP if one is present.
(Lack of voltage at these places may indicate a blown
line fuse, etc.)
[D]
If you do not have a programmable controller
operating your motor starter contactor, verify that the
"ILK SENSE" switch (located to the right of the brake
LED on the control board) is in the ON position.
[E]
If you have a programmable controller operating your
motor starter contactor, refer to section 7.1
Note that 230-volt units operated from 208 volts will
produce somewhat lower torque. Consult the factory if
this is a problem.
If the power line fuses blow at high torque settings, the
brake should be removed from the motor power line, and
operated from a separate disconnect fused at the same
rating as the motor.
10.2
No Braking When Motor is Turned OFF.
[ ] First, verify that the unit is installed and wired
correctly.
[ ] Next, check that the TIME and TORQUE adjustments
are not set too low.
[ ] Check for blown fuses in the supply line and in the
SHORT-STOP.
Possible reasons for blown fuses are:
[ ] Interlock not operating properly - the most likely cause
is that it is wired wrong, OR NOT AT ALL!
[ ] Overloading of the SHORT-STOP. Replace fuses, and
try operating at lower braking torque. If fuses do not
blow until torque is turned up, the SHORT-STOP
chosen was probably too small for the application.
[ ] Power factor capacitors, if used, MUST NOT be across
the load