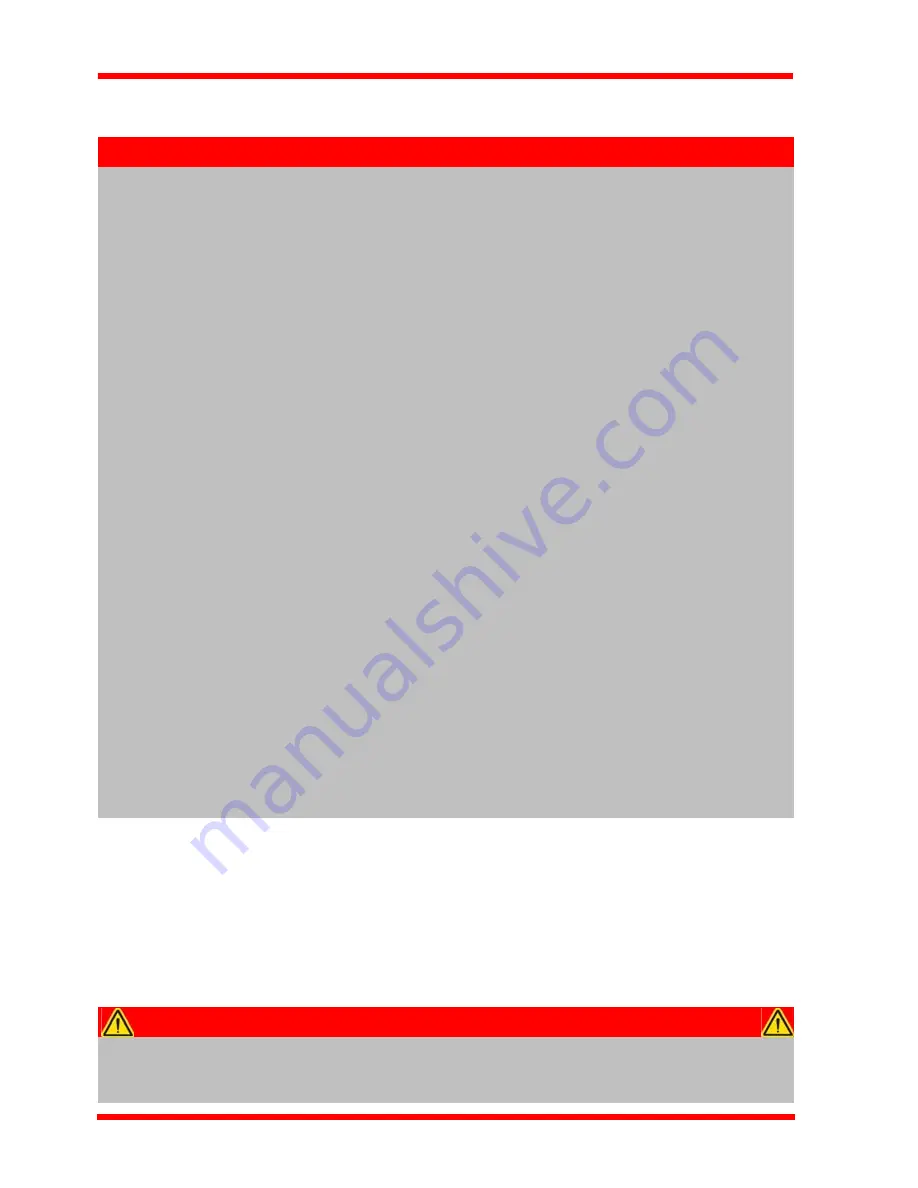
12
HA0263T Rev E May 2017
Chapter 4
4.2
Maintenance
The product is maintenance free. If any problems occur, the user should contact the
local Thorlabs tech support for more information.
4.3
Transportation
Note
The MOTOR DRIVE connectors for each channel/axis contain an
EEPROM, which stores the factory default settings for the set up
parameters. When the stage is connected, these settings are loaded into
the controller on start up, and are tuned for loads up to the 1.0 kg (2.2 lb)
maximum, at speeds up to 250 mm/s.
However, depending on the load being driven and the speed/duty cycle of
the particular application, it may be necessary to further optimize the
Position PID loop settings.
If problems are encountered (e.g. stability of the closed loop position
control, lost motion or incomplete moves) the position loop PID
parameters should be adjusted to tune the stage for the given application.
Normally, only minor adjustment of the Proportional, Integral and
Derivative parameters should be necessary, and some trial and error will
be required before the ideal settings for a specific application are
achieved. In cases where further adjustment of the control loop
parameters is required, the following guidelines are provided in order to
assist in the tuning process.
Position PID Settings Summary
Stage overshoots the intended position
- reduce the integral term, and
increase the derivative and proportional terms.
Stage fails to attain final position
- increase the integral and proportional
terms.
Motion is unstable
- reduce the proportional and integral terms, increase
the derivative term.
Stage sounds noisy
- reduce the derivative term.
Please see the handbook supplied with the controller, for more
information on changing these settings
Caution
When packing the unit for shipping, use the original packing. If this is not
available, use a strong box and surround the unit with at least 100 mm of
shock absorbent material.