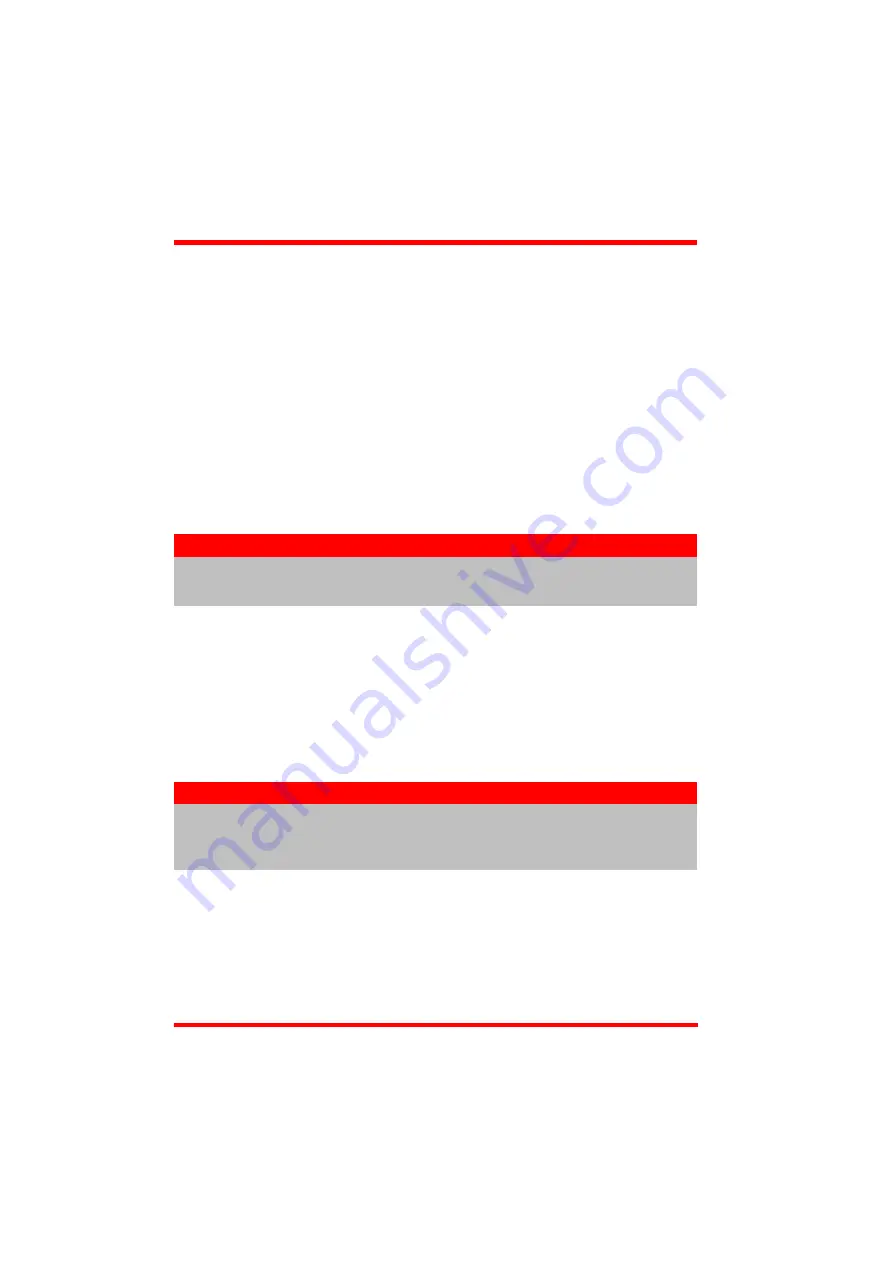
46
HA0216T Rev D March 2012
Chapter 5
Position PID Settings Summary
Stage overshoots the intended position
- reduce Int and increase Deriv and Prop terms.
Stage doesn't attain final position
- increase the Int and Prop terms.
Motion is unstable
- reduce Prop and Int, increase Deriv.
Stage sounds noisy
- reduce Deriv.
Current Loop Control Settings
The motion processors within the BBD series controllers use digital current control as a
technique to control the current through each phase winding of the motors. In this way,
response times are improved and motor efficiency is increased. This is achieved by
comparing the required current with the actual current to create a current error, which is
then passed through a digital PI-type filter. The filtered current value is used to develop an
output voltage for each motor coil. The following parameters allow this signal to be tuned
for a fast response and low error when moving to the demanded position.
Proportional
– This term drives the motor current to the demand value, reducing the
current error. It accepts values in the range 0 to 32767.
Integral
– This term provides the ‘restoring force’ that grows with time, ensuring that
the current error is zero under a constant torque loading. It accepts values in the
range 0 to 32767.
Integral Limit
– This term is used to cap the value of the lntegrator to prevent an
excessive build up over time of the ‘restoring force’, thereby causing runaway of the
integral sum at the output. It accepts values in the range 0 to 32767. If set to 0 then
the integration term in the PI loop is ignored.
Integral Dead Band
– This parameter allows an integral dead band to be set, such that
when the error is within this dead band, the integral action stops, and the move is
completed using the proportional term only. It accept values in the range 0 to 32767.
Feed Forward
– This parameter is a feed-forward term that is added to the output of
the PI filter. It accept values in the range 0 to 32767.
Note
These parameters are specific to the motor within the stage. Default
values are set at the factory and under normal circumstances do not need
to be changed.
Note
The following two parameters assist in fine tuning the motor drive current
and help reduce audible noise and/or oscillation when the stage is in
motion. A certain amount of trial and error may be experienced in order
to obtain the optimum settings.