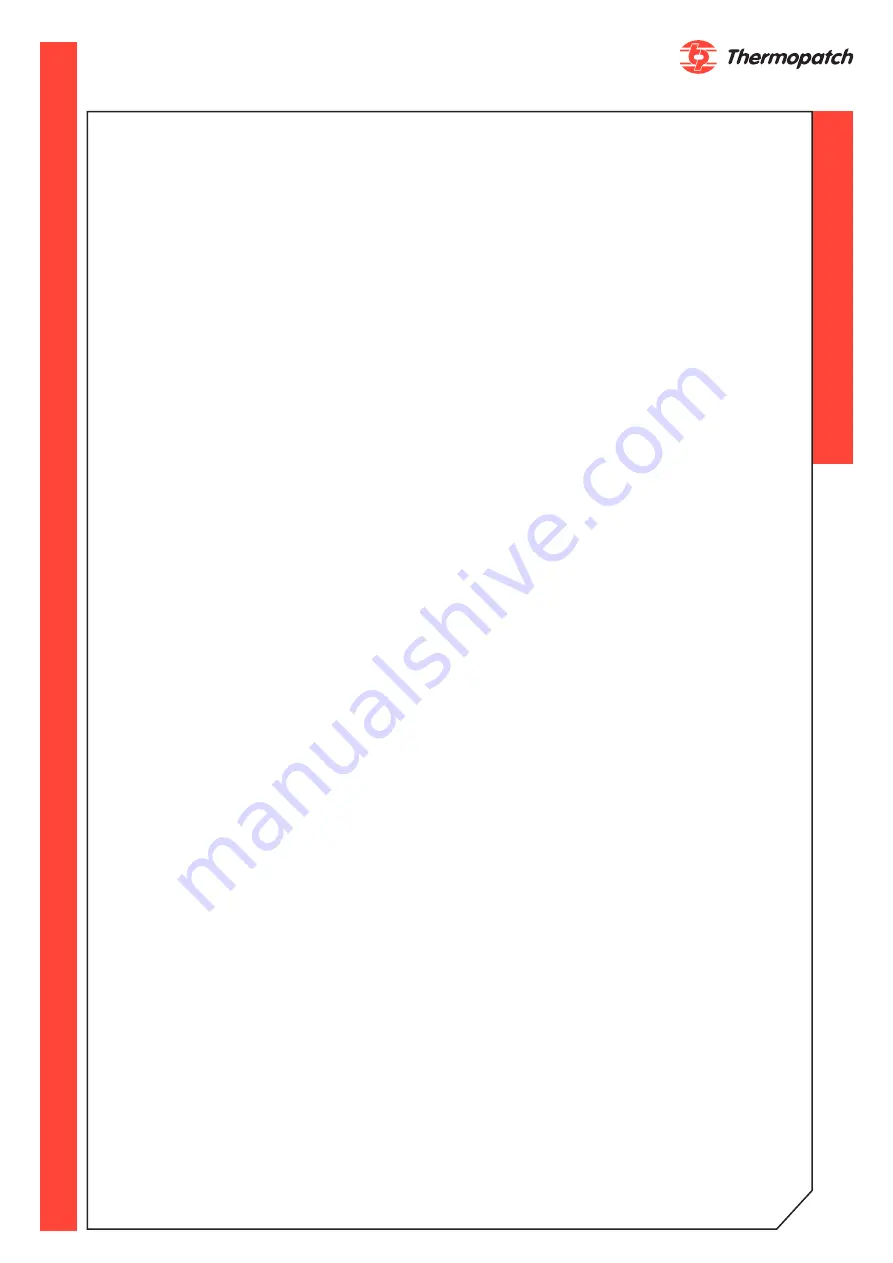
thermopatch.com
19
6.3 ADJUSTING THE PRINTING PRESSURE AND PLATEN HEIGHT PRINTING
PRESSURE
Printing pressure is preset at the factory to 50 PSI. The printing pressure range is from 25
PSI (1.8 BAR) minimum to 70 PSI (4.8 BAR) maximum. NEVER EXCEED 70 PSI. In general,
the larger the printing area, the higher the pressure required. The air regulator is located
outside, at the rear of the machine. At the top of the regulator is a black knob. Pull upward
to change the current setting. Turn the knob clockwise to increase the air pressure or coun-
terclockwise to decrease the air pressure. After pressing down on the foot pedal and then
releasing, check the air gauge reading. Readjust if necessary, then activate the foot pedal
and release again for a new gauge reading. To lock in a setting, push the black knob down
into its original position.
Printing Platen Adjustment
Occasionally, it may be necessary to increase the pressure on one corner or side of the
printing platen in order to make it print better in that area. This might be true where an
engraved design has a denser area in one corner. To adjust, locate the appropriate thumb
screws below the rubber platen. Looking from the top, turn the screw counterclockwise to
increase the pressure. NOTE: The platen is level when all screws are turned clockwise and
the platen is put in its lowest position.
Setup for 2, or More Ribbons
1.
Multiple ribbons of different colors are threaded the same as a single ribbon shown in
Figure 10 — Ribbon Roll Threading.
a.
The rolls must be separated by a thin disc, to prevent interaction, when they are dif-
ferent outside diameters. Three discs are provided in the Optional Printing Kit, and are to be
used on the unwind, or supply shaft.
2.
Place one roll on shaft followed by a disc and push to rear. Repeat this procedure
for each roll added. No disc is required after the last roll added. Replace the supply flange
and clamp collar. If a single ribbon is used, push the three thin separator discs to the rear,
against the supply flange or remove from machine for storage.
3.
Usually the outer clamp collar can be adjusted to minimize endplay of the roll, be-
cause of the drag from the roll insert on the shaft. If the roll turns freely on the shaft, push
the clamp collar in to create drag on the roll. Too much drag may cause the ribbon to break
or the motor to stall. Do not stall motor.
4.
Thread the tape through the machine: Refer to Figure 10 for a visual aid.
•
Unroll approximately two feet of tape off the roll.
•
Feed the tape under the sensor roller, under the heating iron, up and around the feed
roller, down under the dancer roll, and up to the take-up shaft.
•
Attach to take-up shaft as shown in Figure 10.
•
Press the JOG button until the tape is taut through the machine.
Содержание Deco-Print DP2000T
Страница 13: ...thermopatch com 13 Step 5 Refer to below Place flange assemblies Item A on supply and take up shafts Item B...
Страница 14: ...thermopatch com 14...
Страница 15: ...thermopatch com 15...
Страница 41: ...thermopatch com 41 Drawing 15 Electronics Module Drawing 16 Main Electronics Module...
Страница 42: ...thermopatch com 42 Drawing 17 AC Harness...
Страница 43: ...thermopatch com 43 Drawing 18 DC Harness...