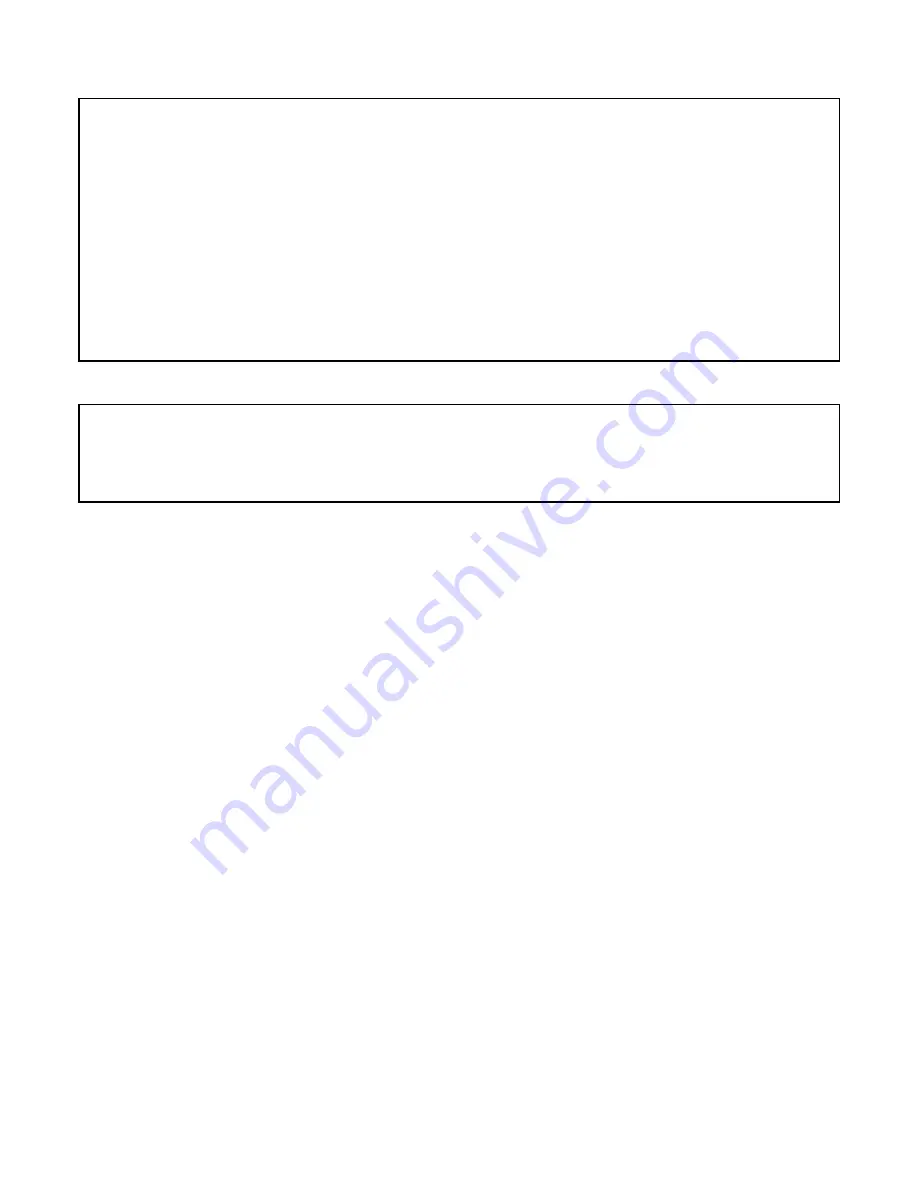
2
WARNINGS
WARNING
THIS FURNACE CONTAINS REFRACTORY CERAMIC INSULATION WHICH CAN PRODUCE RESPIRABLE
FIBERS AND DUST WHEN HANDLED. THESE FIBERS CAN CAUSE IRRITATION AND CAN AGGRAVATE PRE-
EXISTING RESPIRATORY DISEASE. THE INTERNATIONAL AGENCY FOR RESEARCH ON CANCER (IARC)
HAS CLASSIFIED REFRACTORY CERAMIC FIBER AS POSSIBLY CARCINOGENIC.
AFTER SERVICE REFRACTORY CERAMIC FIBER DUSTS MAY CONTAIN CRYSTALLINE SILICA, WHICH MAY
CAUSE LUNG DAMAGE (SILICOSIS) AND WHICH HAS BEEN CLASSIFIED BY IARC AS A PROBABLE
CARCINOGEN.
CONSULT THE OWNER’S MANUAL FOR THIS EQUIPMENT BEFORE YOU MAKE ANY REPAIRS TO OR
REPLACE ANY PARTS, INCLUDING REPAIRS TO OR REPLACEMENTS OF ELECTRICAL COMPONENTS OR
INSULATING MATERIALS. THE OWNER’S MANUAL CONTAINS INFORMATION AND WARNINGS RELATING
TO THE HAZARDS ASSOCIATED WITH THE REPAIR AND MAINTENANCE OF THIS EQUIPMENT.
WARNING
REFER SERVICING TO QUALIFIED PERSONNEL.
INTRODUCTION
A .
Intended Use
The Type 2000 furnaces are general laboratory and heat treating furnaces. Standard models are intended
for applications requiring temperatures from 400°F (204°C) to 1800°F (982°C) for continuous use, or
temperatures from 1800°F (982°C) to 2000°F (1093°C) for intermittent use. High temperature (-1) models
are intended for applications requiring temperatures from 400°F (204°C) to 1950°F (1066°C) for
continuous use, or temperatures from 1950°F (1066°C) to 2150°F (1177°C) for intermittent use.
Continuous use is operating the furnace for more than 3 hours and intermittent use is operating the
furnace for less than 3 hours.
The unit consists of 1) a heating chamber, 2) an automatic proportioning temperature control, 3) a two-
position power switch. See Figure 1 for the overall shape and general features of the unit.
B .
Principles of Operation
The furnace chamber is heated by four electric resistance heaters which are embedded In a refractory
material. The chamber is insulated with a ceramic fiber insulation. The temperature is controlled by an
automatic proportioning controller using a chromel/ alumel thermocouple. The control unit is located
under the furnace chamber well Insulated from the furnace chamber.
This furnace is equipped with thermocouple break protection, a door safety switch, and cold junction
compensation. The silicon controlled rectifiers which control power to the heating elements are controlled
by internal circuitry to operate as zero switching devices. This zero switch capability prevents line
interference which can effect other sensitive equipment.
Содержание FC2020P
Страница 2: ...January 1990 LT326X1...
Страница 6: ...3 Barnstead Thermolyne 1 800 553 0039 Figure 1...
Страница 7: ...4 Figure 2...
Страница 21: ...18 Figure 3 Exploded View...
Страница 24: ...21 Barnstead Thermolyne 1 800 553 0039 Figure 4 Wiring Diagram...