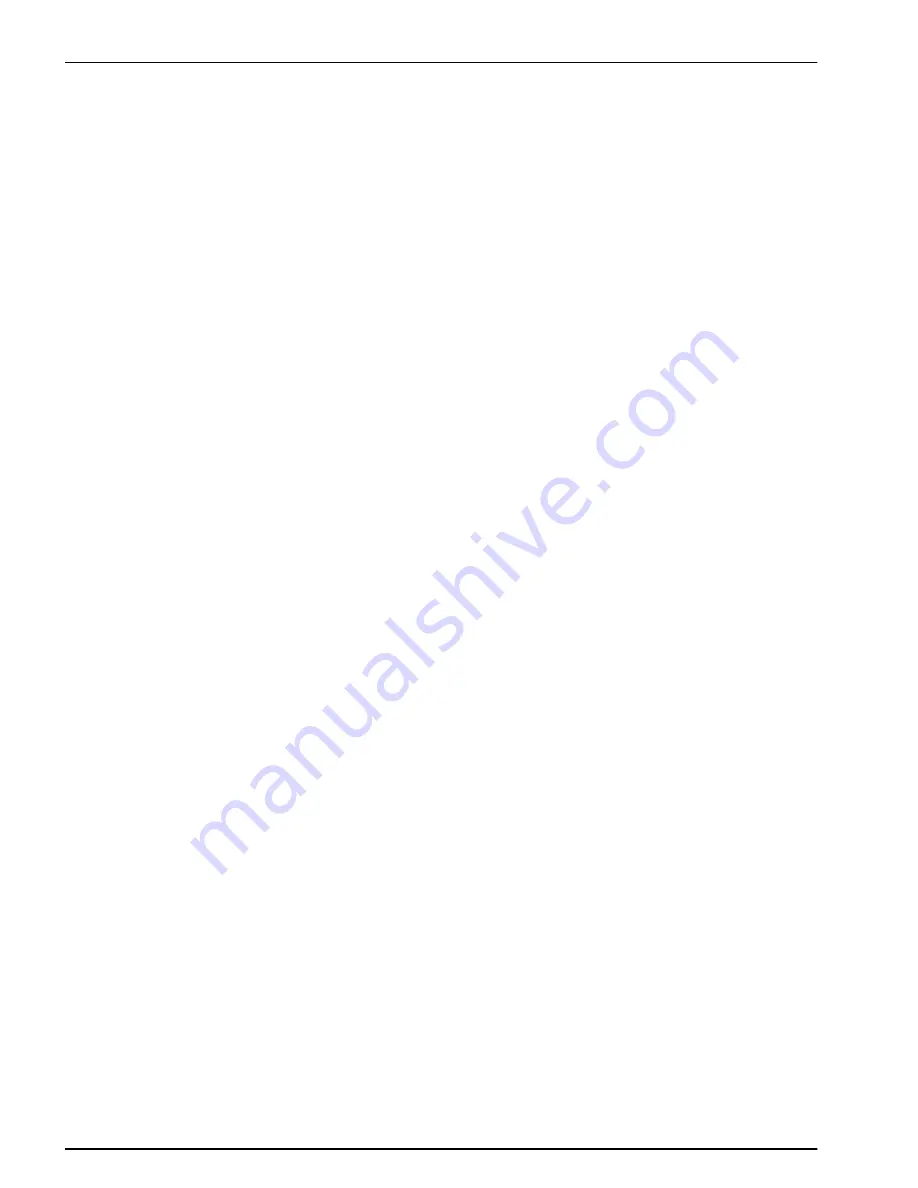
Refrigeration Service Operations (Rev. 1/99)
58
DISCHARGE CHECK VALVE REPAIR
(Model 20 Only)
Testing the Discharge Check Valve
The discharge check valve is a very important part of the
Model 20 system. The check valve isolates the engine-
driven compressor from the electric standby compressor,
ensuring the compressor oil and refrigerant do not migrate
between compressors. The check valve should be tested
when the system is initially charged and operating and any-
time the system has been opened for service or repair. Test-
ing the check valve requires two gauge manifold sets.
1.
Disconnect the liquid injection solenoid valve wires.
2.
With the unit off, install a gauge manifold set on each
compressor.
3.
Observe the gauge manifold readings of the electric
standby compressor. If the high side and low side read-
ings are not the same, open the gauge manifold valves
and equalize the pressures. Close the gauge manifold
valves.
4.
Adjust the thermostat so the unit will run in cool. Start
the truck and run the unit with the engine-driven com-
pressor.
5.
Observe the gauge manifold readings of the engine-
driven compressor. The head pressure should increase
and the suction pressure should decrease.
6.
Observe the gauge manifold readings of the electric
standby compressor. The high side pressure should
remain the same as the pressure in step 3 after the high
and low sides were equalized. If the high side pressure
is increasing or has increased noticeably, the discharge
check valve is leaking internally.
7.
Turn the unit off and shut off the truck engine. Connect
the remote control box to an appropriate electric power
source.
8.
Observe the gauge manifold reading of the engine-
driven compressor. If the high side and low side read-
ings are not the same, open the gauge manifold valves
and equalize the pressures. Close the gauge manifold
valves.
9.
Adjust the thermostat so the unit will run in cool. Start
the unit and run on electric standby.
10. Observe the gauge manifold readings of the electric
standby compressor. The head pressure should increase
and the suction pressure should decrease.
11. Observe the gauge manifold readings of the engine-
driven compressor. The high side pressure should
remain the same as the pressure in step 8 after the high
and low sides were equalized. If the high side pressure
is increasing or has increased noticeably, the discharge
check valve is leaking internally. Stop the unit.
12. Remove the gauge manifold sets and the electric
standby power source. Connect the wires to the liquid
injection solenoid valve. If the check valve is leaking
internally, refer to the repair procedures.
Discharge Check Valve Repair
Disassembly
1.
Remove the refrigerant charge.
2.
Loosen and remove the end cap nuts.
3.
Carefully remove the end caps from the valve body.
Avoid damaging the refrigeration lines, pistons or
spring.
4.
Remove the pistons, spring and copper sealing washers.
5.
Check the spring. The free length should be 1.75 in.
(44.5 mm). Replace the spring if the free length is less
than 1.57 in. (37.9 mm).
Содержание 914 724
Страница 4: ......
Страница 8: ......
Страница 14: ...4...
Страница 16: ...6...
Страница 25: ...Unit Description Rev 1 99 15 1 Fan 2 Thermometer Sensor 3 Thermostat Sensor Evaporator 1 2 3 AGA358...
Страница 32: ...22...
Страница 38: ...28...
Страница 98: ...88...
Страница 107: ...97 Model 10 and 20 Schematic Diagram...
Страница 108: ...98 Model 10 Wiring Diagram...
Страница 109: ...99 Model 20 Wiring Diagram...
Страница 110: ...100 Model 20 Single Phase with Heat Option Schematic Diagram...
Страница 111: ...101 Model 20 Single Phase Wiring Diagram...