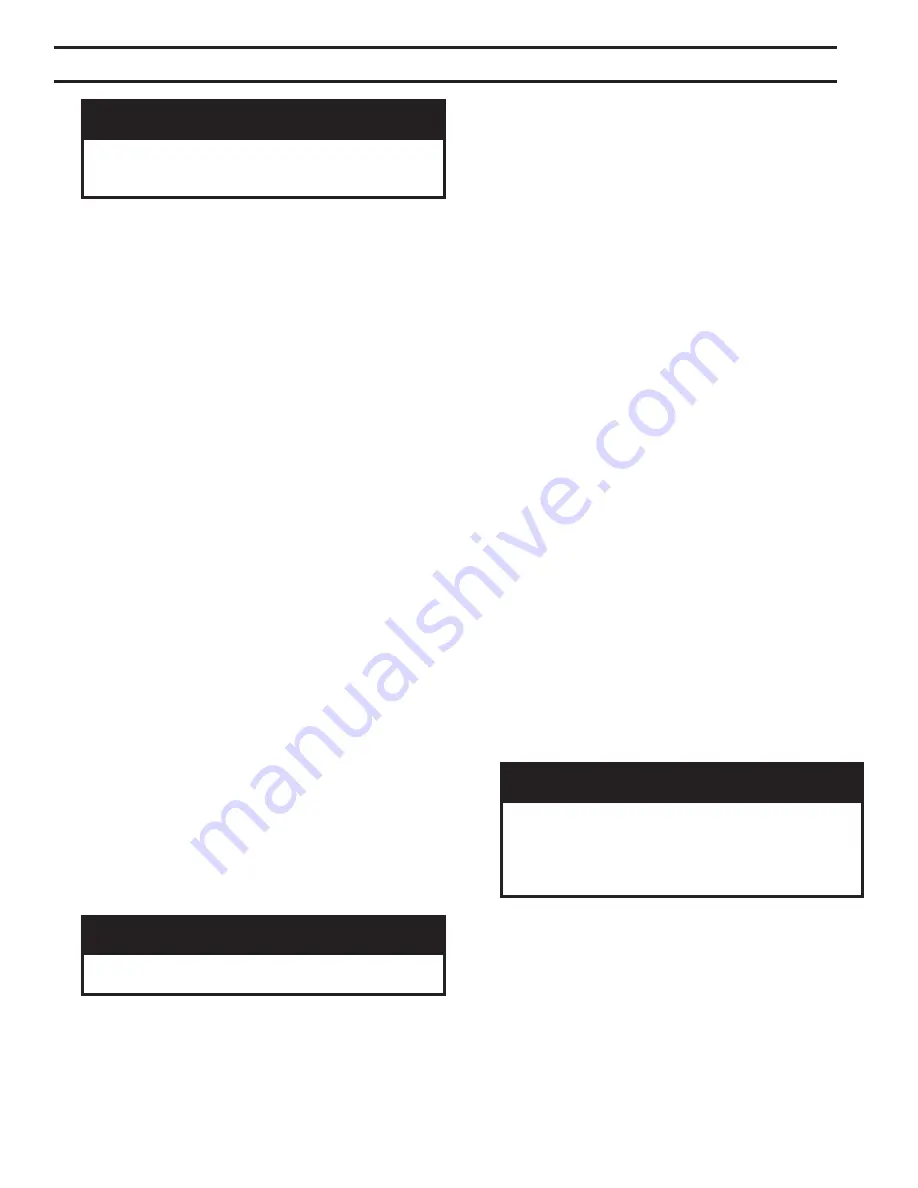
9
I. Pre-Installation
1. Determine volume of space (boiler room). Rooms
communicating directly with space (through
openings not furnished with doors) are considered
part of space.
Volume [ft³] = Length [ft] x Width [ft] x Height [ft]
2. Determine Total Input of all appliances in space.
Round result to nearest 1,000 Btu per hour (Btuh).
3. Determine type of space. Divide Volume by Total
Input.
a. If result is greater than or equal to 50 ft³ per
1,000 Btuh, space is considered an
unconfined
space
.
b. If result is less than 50 ft³ per 1,000 Btuh, space
is considered a
confined space
.
4. Determine building type. A building of
unusually
tight construction
has the following characteristics:
a. Walls and ceiling exposed to outside atmosphere
have a continuous water vapor retarder with a
rating of 1 perm or less with openings gasketed
and sealed, and;
b. Weather-stripping has been added on openable
windows and doors, and;
c. Caulking or sealants applied in joints around
window and door frames, between sole
plates and floors, between wall-ceiling joints,
between wall panels, at plumbing and electrical
penetrations, and at other openings.
5. For boiler located in an
unconfined space in a
building of
other than unusually tight construction
,
adequate combustion and ventilation air is normally
provided by fresh air infiltration through cracks
around windows and doors.
NOTICE
Boilers operated with sealed combustion are
exempt from needing provisions for combustion
air from the room, provided air intake piping is
installed per code and the instructions in this
manual.
6. For boiler located within
unconfined space in
building of unusually tight construction
or within
confined space
, provide outdoor air through two
permanent openings which communicate directly or
by duct with the outdoors or spaces (crawl or attic)
freely communicating with the outdoors. Locate one
opening within 12 inches of top of space. Locate
remaining opening within 12 inches of bottom of
space. Minimum dimension of air opening is 3
inches. Size each opening per the following:
WARNING
Carefully read all instructions before installing
boiler. Failure to follow all instructions in proper
order can cause personal injury or death.
A
. Installation must conform to the requirements of the
authority having jurisdiction. In the absence of such
requirements, installation must conform to the
National
Fuel Gas Code
, NFPA 54/ANSI Z223.1, and/or
CAN/CSA B149 Installation Codes. Where required
by the authority having jurisdiction, the installation
must conform to the
Standard for Controls and Safety
Devices for Automatically Fired Boilers
, ANSI/ASME
CSD-1.
B.
The boiler is not design certified for installation on
combustible flooring. The boiler must not be installed
on carpeting.
C.
Provide clearance between boiler jacket and
combustible material in accordance with local fire
ordinance. Refer to page 4 of this manual for minimum
listed clearance from combustible material.
D.
Install on level floor. For basement installation provide
concrete base if floor is not perfectly level or if water
may be encountered on floor around boiler. Floor
must be able to support weight of boiler, water and all
additional system components.
E.
Protect gas ignition system components from water
(dripping, spraying, rain, etc.) during boiler operation
and service (circulator replacement, condensate trap
service, control replacement, etc.).
F.
Provide combustion and ventilation air in accordance
with applicable provisions of local building codes
or: USA -
National Fuel Gas Code
, NFPA 54/
ANSI Z223.1, Section 5.3, Air for Combustion and
Ventilation; Canada - Natural Gas Installation Code,
CAN/CSA - B149.1, or Propane Installation Code,
CAN/CSA - B.149.2, Part 5, Venting Systems and Air
Supply for Appliances.
WARNING
Adequate combustion and ventilation air must be
provided to assure proper combustion.
The following guideline is based on the
National Fuel
Gas Code
, NFPA 54/ANSI Z223.1.
Содержание EVS SERIES
Страница 13: ...13 Figure 3 Sidewall Positive Pressure Venting Optional Figure 2 Sidewall Positive Pressure Venting ...
Страница 14: ...14 Figure 4 Vertical Pressurized Venting ...
Страница 16: ...16 Figure 5 Typical Negative Pressure Conventional Venting ...
Страница 18: ...18 Figure 7 Vertical Air Intake Piping ...
Страница 27: ...27 Figure 9a 208 230 460V 1 3 ph 60 Hz Supply Power Wiring Schematic ...
Страница 28: ...28 Figure 9b 120V 1ph 60Hz Supply Power Wiring Schematic ...
Страница 29: ...29 Figure 9c Standard UL FM CSD 1 Wiring Diagram EVS 500 2000 ...
Страница 31: ...31 Figure 9e Standard UL FM CSD 1 EVS 2000S 3000 ...
Страница 35: ...35 Figure 11 Modular System Horizontal Air Intake Piping ...
Страница 36: ...36 Figure 12 Modular System Vertical Air Intake Piping ...
Страница 37: ...37 Figure 13 Modular System Typical One Pipe Water Piping ...
Страница 38: ...38 Figure 14 Modular System Typical Primary Secondary Water Piping ...
Страница 39: ...39 Figure 15 Modular System Typical Primary Secondary without System Pump ...
Страница 40: ...40 Figure 16 Modular System Typical Reverse Return Water Piping ...
Страница 41: ...41 Figure 17 Modular System Reverse Return with System Pump Only ...
Страница 42: ...42 Figure 18 Modular System Typical Primary Secondary with Reverse Return ...
Страница 58: ...58 Figure 19 Combustion Chamber Assembly ...
Страница 60: ...60 Figure 20 Burner Assembly FRONT VIEW TOP VIEW ...
Страница 62: ...62 Figure 21 UL FM CSD 1 Main Gas Train Assembly ...
Страница 65: ...65 Figure 22b DB B Gas Train 500 750 Figure 22c DB B Gas Train 1000 2000 ...
Страница 70: ...70 Figure 23 Jacket Panels ...
Страница 74: ...74 Figure 25 Pilot Assembly Bishop Design ...
Страница 88: ...88 NOTES ...
Страница 89: ...89 NOTES ...
Страница 90: ...90 NOTES ...
Страница 91: ...91 NOTES ...