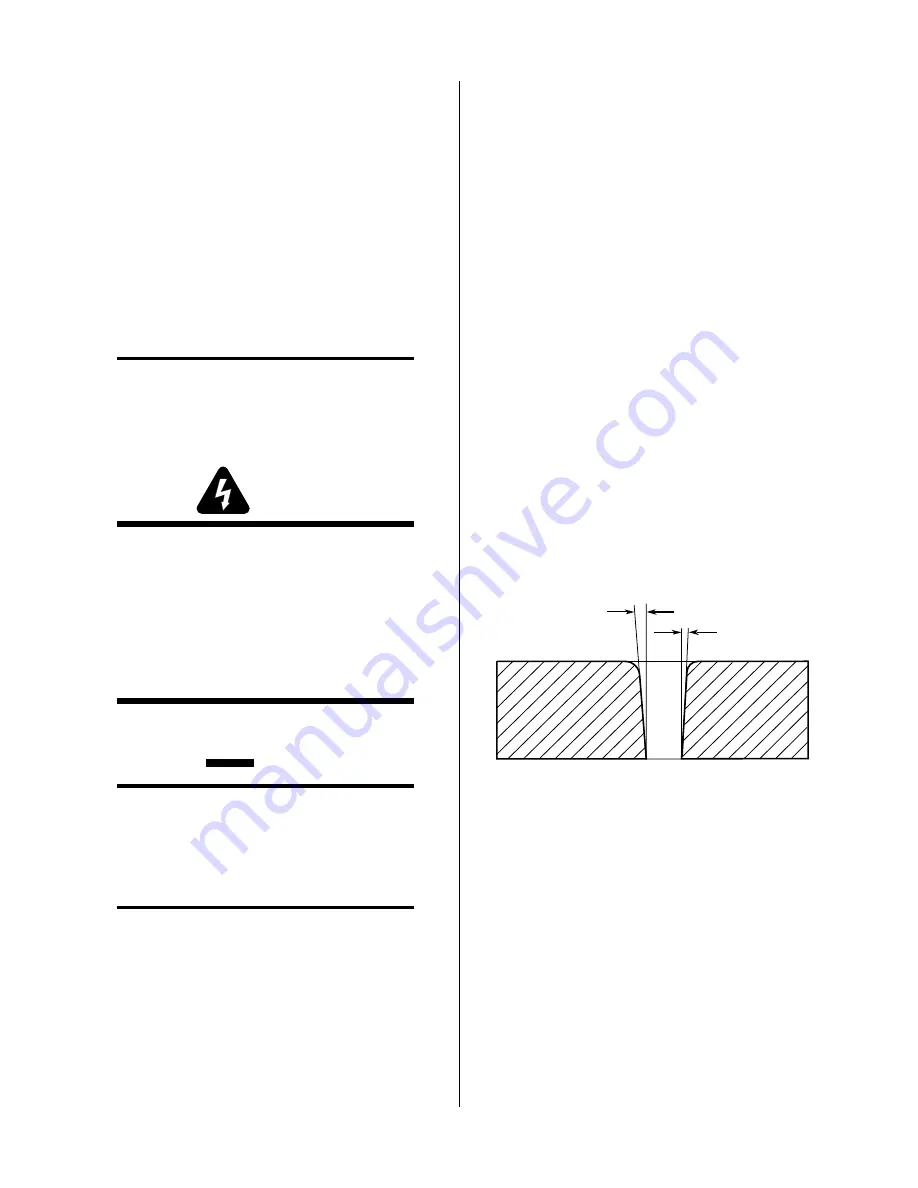
SECTION 5: SERVICE
26
Manual 0-2748
3. Disconnect gas supply hose from barbed fitting.
4. Turn the Cover counterclockwise and remove it
from the Filter Housing. The Filter Element is lo-
cated inside the Housing.
5. Remove the Filter Element from the Housing and
set Element aside to dry.
6. Wipe inside of housing clean, then insert the re-
placement Filter Element cup side first, as shown
below.
7. Replace Housing on Cover.
8. Reattach gas supply hose to barbed fitting.
NOTE
If unit leaks between housing and cover, inspect
the "O" Ring for cuts or other damage.
5.03 Common Operating Problems
WARNINGS
Disconnect primary power at the source before dis-
assembling the power supply, torch, or torch leads.
Frequently review the Important Safety Precau-
tions (page 1). Be sure the operator is equipped with
proper gloves, clothing, eye and ear protection.
Make sure no part of the operator’s body comes into
contact with the workpiece while the torch is acti-
vated.
CAUTION
Sparks from the cutting process can cause damage
to coated, painted, and other surfaces such as glass,
plastic and metal.
NOTE
Handle torch leads with care and protect them from
damage.
A. Piloting
Piloting is harder on parts life than actual cutting because
the pilot arc is directed from the electrode to the tip rather
than to a workpiece. Whenever possible, avoid excessive
pilot arc time to improve parts life.
B. Torch Standoff
Improper standoff (the distance between the torch tip and
workpiece) can adversely affect tip life as well as shield
cup life. Standoff may also significantly affect the bevel
angle. Reducing standoff will generally result in a more
square cut.
C. Edge Starting
For edge starts, hold the torch perpendicular to the work-
piece with the front of the tip at the edge of the work-
piece at the point where the cut is to start. When starting
at the edge of the plate, do not pause at the edge and
force the arc to "reach" for the edge of the metal. Estab-
lish the cutting arc as quickly as possible.
D. Direction of Cut
In the torches, the plasma gas stream swirls as it leaves
the torch to maintain a smooth column of gas. This swirl
effect results in one side of a cut being more square than
the other. Viewed along the direction of travel, the right
side of the cut is more square than the left (Refer to Fig-
ure 5-2). To make a square-edged cut along an inside di-
ameter of a circle, the torch should move counterclock-
wise around the circle. To keep the square edge along an
outside diameter cut, the torch should travel in a clock-
wise direction.
Right Side
Cut Angle
Left Side
Cut Angle
A-00512
Figure 5-2 Side Characteristics Of Cut
E. Dross
Generally when dross is present on carbon steel, it is re-
ferred to as either "high speed or slow speed dross".
"High speed dross" usually forms a narrow bead along
the bottom of the cut edge and is very difficult to remove.
"Slow speed dross" will be in larger quantities but does
not adhere tightly to the cut edge and can be easily re-
moved.
When cutting a troublesome steel, it is suggested that the
torch travel speed be reduced to produce "slow speed
dross". Any required cleanup can then be done by scrap-
ping, not grinding.
Содержание PakMaster 100 XL plus
Страница 1: ...Manual No 0 2748 August 23 1999 Operating Manual A 02464 Air Plasma Cutting Power Supply ...
Страница 3: ...Purchase Date Power Supply Torch Record Serial Numbers For Warranty Purposes ...
Страница 4: ......
Страница 36: ...SECTION 5 SERVICE 30 Manual 0 2748 A 01354 Internal Fuse 0 8 Amps 600V Figure 5 4 Internal Fuse Location ...
Страница 41: ...Manual 0 2748 35 APPENDIX This Page is Blank ...
Страница 42: ...APPENDIX 36 Manual 0 2748 APPENDIX III SYSTEM SCHEMATIC A 02465 16 13 12 5 1 9 INRUSH GAS GAS SOL INRUSH 5 ...
Страница 43: ...Manual 0 2748 37 APPENDIX A 02465 OK OK TO MOVE 8 23 99 AC EC 8397 HS 08 23 99 ...
Страница 44: ...APPENDIX 38 Manual 0 2748 ...