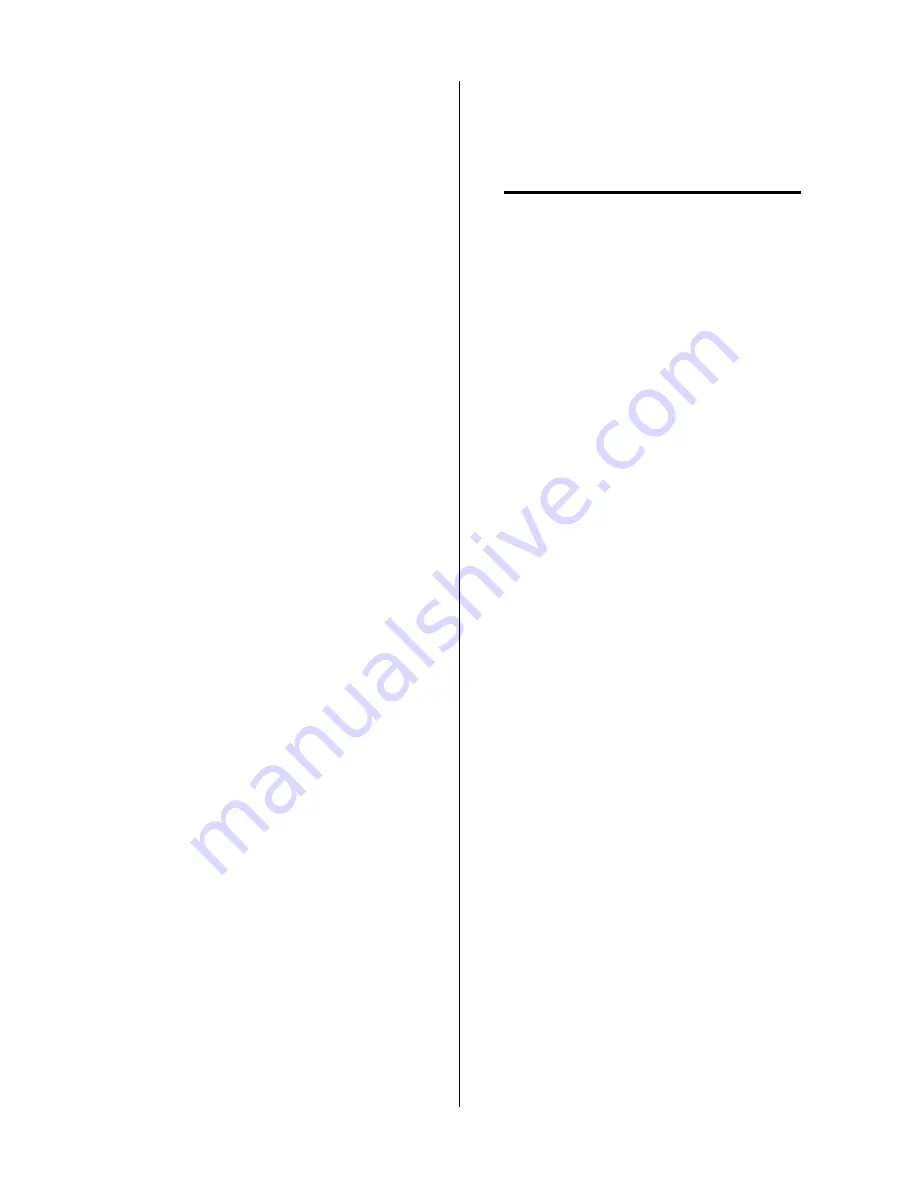
SERVICE TROUBLESHOOTING
18
Manual 0-2569
E. Logic PC Board (PCB) Functions
The Logic PCB controls the timing and sequencing of the
system. The functions of the Logic PCB are as follows:
• Monitors the pressure, temperature, and coolant
flow interlocks.
• Controls the gas solenoids.
• Controls the pre-flow and post-flow times which
are selected by DIP-switches on the Logic PCB.
• Drives the front panel Status LED’s.
• Contains the circuit for measuring coolant conduc-
tivity.
• Contains circuits to determine if a Slave Power Sup-
ply is connected and turned ON.
• If Slave Power Supply is turned ON, signals the
Switching Control PCB and Remote Control to be
configured for 300A operation.
The following is the sequence that the Logic PCB goes
through:
• Receives the START signal from the CNC cutting
machine controller from either the remote control,
standoff control, direct from the controller via the
remote connector or through TB2 the “simple” in-
terface terminal strip.
• Initiates gas pre-flow.
• Energizes the main contactor, W1 or W2, as deter-
mined by the Voltage Selection PCB.
• When the Arc Starter Box senses OCV greater than
250V between the torch’s plus and minus, it starts
the capacitor discharge (CD) arc starting circuit to
fire the spark gap producing the high voltage spark
which starts the DC pilot arc.
• Once a constant DC pilot is established the torch
voltage drops below 250V and shuts off the CD
circuit.
• When the torch is close to the work the cutting arc
“transfers” to the work. The resulting current in
the work lead is sensed by the Shunt Amp, then
the Switching Control PCB sends the CSR signal
to the Logic PCB which opens the pilot contactor ,
shutting off the pilot and generating an OK-TO-
MOVE signal.
• The OK-TO-MOVE signal can be either contact clo-
sure or 24 VAC through contacts selected by SW5
on the Logic PCB (set for contacts if RC6010 or
SC11 is used). The OK-TO-MOVE signal is sent to
the remote control, standoff control or direct to the
cutting machine controller. It also controls the Arc
Hour and Starts Counter Meters and the optional
High Flow Water Shield.
F. Isolation PC Board (PCB)
NOTE
The Isolation PCB is located only in the Master
Power Supply.
All control signals between the Master Power Supply and
the Slave Power Supply pass through the Isolation PCB
in the Master Power Supply. The Isolation PCB optically
isolates the following signals:
• ENABLE TO SLAVE (digital ON or OFF signal)
• START TO SLAVE (digital ON or OFF signal)
• SLAVE IS ON (digital ON or OFF signal)
• DEMAND ( current control) TO SLAVE(analog 0
to 10vdc signal)
• OUTPUT SIGNAL FROM SLAVE. (analog 0 to
10vdc signal)
Power for the circuits on the Isolation PCB that connect
to the Master Power Supply comes from the Master Power
Supply Switching Control PCB. Power for the circuits on
the Isolation PCB that connect to the Slave Power Supply
comes from the Slave Power Supply Switching Control
PCB.
The output of the Isolation PCB goes through the Parallel
cable between the Master and Slave Power Supply.
G. Pulser PC Board (PCB)
Pulsing the pilot current allows higher transfer distances
without increasing parts wear. The Merlin 6000 Pulser
uses a transistor to momentarily short out a portion of
the pilot resistors. The result is a short pulse, about 5 ms,
of higher pilot current to increase the maximum transfer
distance. The pulse repeats at a 33 Hertz (Hz) rate. Higher
rates of 50 or 66 Hz can be selected using a DIP-switch,
SW1, on the Pulser PCB. Power for the Pulser PCB con-
trol circuits is obtained from the voltage on the pilot re-
sistors.
H. LED/Current Control PC Board
The LED/Current Control PC Board contains the se-
quence status LED indicators and the front panel current
control pot.
I. Remote Control
The Remote Control (RC6010) allows remotely control-
ling the cutting current, setting reduced current for cor-
ner slowdown. An ENABLE switch shuts down the
power supply and coolant pump for changing torch con-
Содержание MERLIN 6000
Страница 1: ...Manual No 0 2569 October 6 1999 MERLIN 6000 Plasma Cutting Master Power Supply Service Manual A 01497...
Страница 6: ...TABLE OF CONTENTS continued...
Страница 16: ...INTRODUCTION 10 Manual 0 2569...
Страница 66: ...REPLACEMENT PROCEDURES 60 Manual 0 2569...
Страница 71: ...Manual 0 2569 65 PARTS LISTS 1 2 4 5 6 7 8 9 10 11 12 13 14 15 16 19 18 17 20 21 A 02341 22 23 3 3 25 24 26...
Страница 82: ...PARTS LISTS 76 Manual 0 2569...
Страница 96: ...APPENDIX 90 Manual 0 2569 APPENDIX XIII CORNER SLOWDOWN CSD CIRCUIT DIAGRAM A 01140...
Страница 103: ...Manual 0 2569 97 APPENDIX APPENDIX XX ARC STARTER BOX OPTION SYSTEM SCHEMATIC A 01575...
Страница 106: ...APPENDIX 100 Manual 0 2569 APPENDIX XXII GAS CONTROL GC3000 WIRING DIAGRAM A 01129...
Страница 107: ...Manual 0 2569 101 APPENDIX...
Страница 108: ...APPENDIX 102 Manual 0 2569 APPENDIX XXIII SYSTEM SCHEMATIC Rev B or Earlier A 01573...
Страница 110: ...APPENDIX 104 Manual 0 2569 APPENDIX XXIV SYSTEM SCHEMATIC Rev C or Later A 01947...
Страница 112: ...APPENDIX 106 Manual 0 2569...