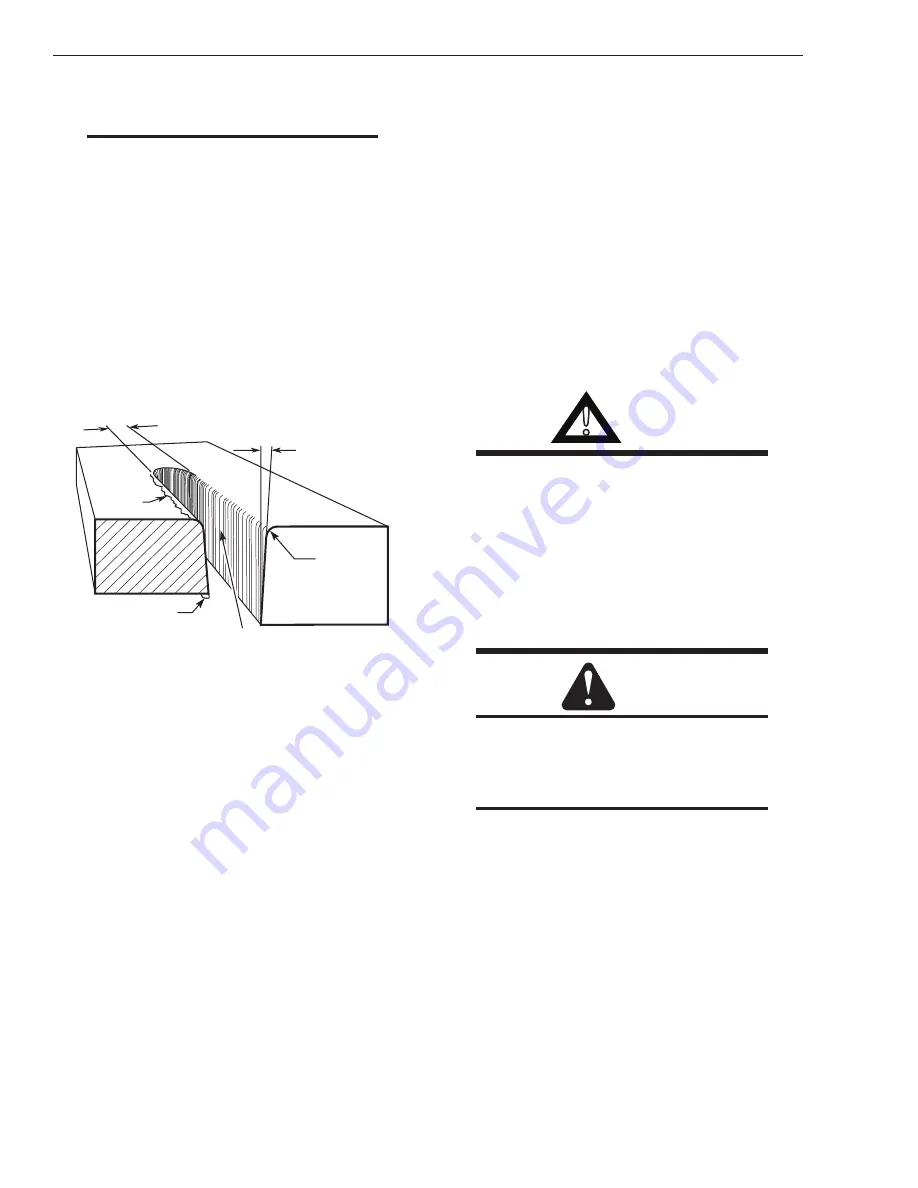
CUTMASTER 152
OPERATION 4T-2
Manual 0-4987
4T.02 Cut Quality
NOTE
Cut quality depends heavily on setup and
parameters such as torch standoff, align-
ment with the workpiece, cutting speed, gas
pressures, and operator ability.
Cut quality requirements differ depending on
application. For instance, nitride build - up and
bevel angle may be major factors when the sur-
face will be welded after cutting. Dross - free cut-
ting is important when finish cut quality is desired
to avoid a secondary cleaning operation. The
following cut quality characteristics are illustrated
in the following figure:
Kerf Width
Cut Surface
Bevel Angle
Top Edge
Rounding
Cut Surface
Drag Lines
Dross
Build-Up
Top
Spatter
A-00007
Cut Quality Characteristics
Cut Surface
The desired or specified condition (smooth or rough)
of the face of the cut.
Nitride Build - Up
Nitride deposits can be left on the surface of the cut
when nitrogen is present in the plasma gas stream.
These buildups may create difficulties if the material
is to be welded after the cutting process.
Bevel Angle
The angle between the surface of the cut edge and
a plane perpendicular to the surface of the plate.
A perfectly perpendicular cut would result in a 0°
bevel angle.
Top - Edge Rounding
Rounding on the top edge of a cut due to wearing
from the initial contact of the plasma arc on the
workpiece.
Bottom Dross Buildup
Molten material which is not blown out of the cut
area and resolidifies on the plate. Excessive dross
may require secondary cleanup operations after
cutting.
Kerf Width
The width of the cut (or the width of material re-
moved during the cut).
Top Spatter (Dross)
Top spatter or dross on the top of the cut caused by
slow travel speed, excess cutting height, or cutting
tip whose orifice has become elongated.
4T.03 General Cutting Information
!
WARNING
Disconnect primary power at the source be-
fore disassembling the power supply, torch,
or torch leads.
Frequently review the Important Safety Pre-
cautions at the front of this manual. Be sure
the operator is equipped with proper gloves,
clothing, eye and ear protection. Make sure no
part of the operator’s body comes into contact
with the workpiece while the torch is activated.
CAUTION
Sparks from the cutting process can cause
damage to coated, painted, and other sur-
faces such as glass, plastic and metal.
NOTE
Handle torch leads with care and protect
them from damage.
Piloting
Piloting is harder on parts life than actual cutting
because the pilot arc is directed from the electrode
to the tip rather than to a workpiece. Whenever
possible, avoid excessive pilot arc time to improve
parts life.
Torch Standoff
Improper standoff (the distance between the torch tip
and workpiece) can adversely affect tip life as well as
shield cup life. Standoff may also significantly affect
the bevel angle. Reducing standoff will generally
result in a more square cut.
Содержание 152 CUTMASTER
Страница 4: ...This Page Intentionally Blank...
Страница 14: ...CUTMASTER 152 GENERAL INFORMATION 1 8 Manual 0 4987 This Page Intentionally Blank...
Страница 22: ...CUTMASTER 152 INTRODUCTION 2T 4 Manual 0 4987 This Page Intentionally Blank...
Страница 32: ...CUTMASTER 152 OPERATION 4 4 Manual 0 4987 This Page Intentionally Blank...
Страница 54: ...CUTMASTER 152 OPERATION 4T 22 Manual 0 4987 This Page Intentionally Blank...
Страница 69: ...CUTMASTER 152 Manual 0 4987 6 5 PARTS LIST A 07994_AB 1 4 2 3 5 6 7 8 9 10 12 11 10 13...
Страница 72: ...CUTMASTER 152 PARTS LIST 6 8 Manual 0 4987 This Page Intentionally Blank...
Страница 77: ...CUTMASTER 152 Manual 0 4987 A 5 APPENDIX This Page Intentionally Blank...
Страница 83: ...This Page Intentionally Blank...