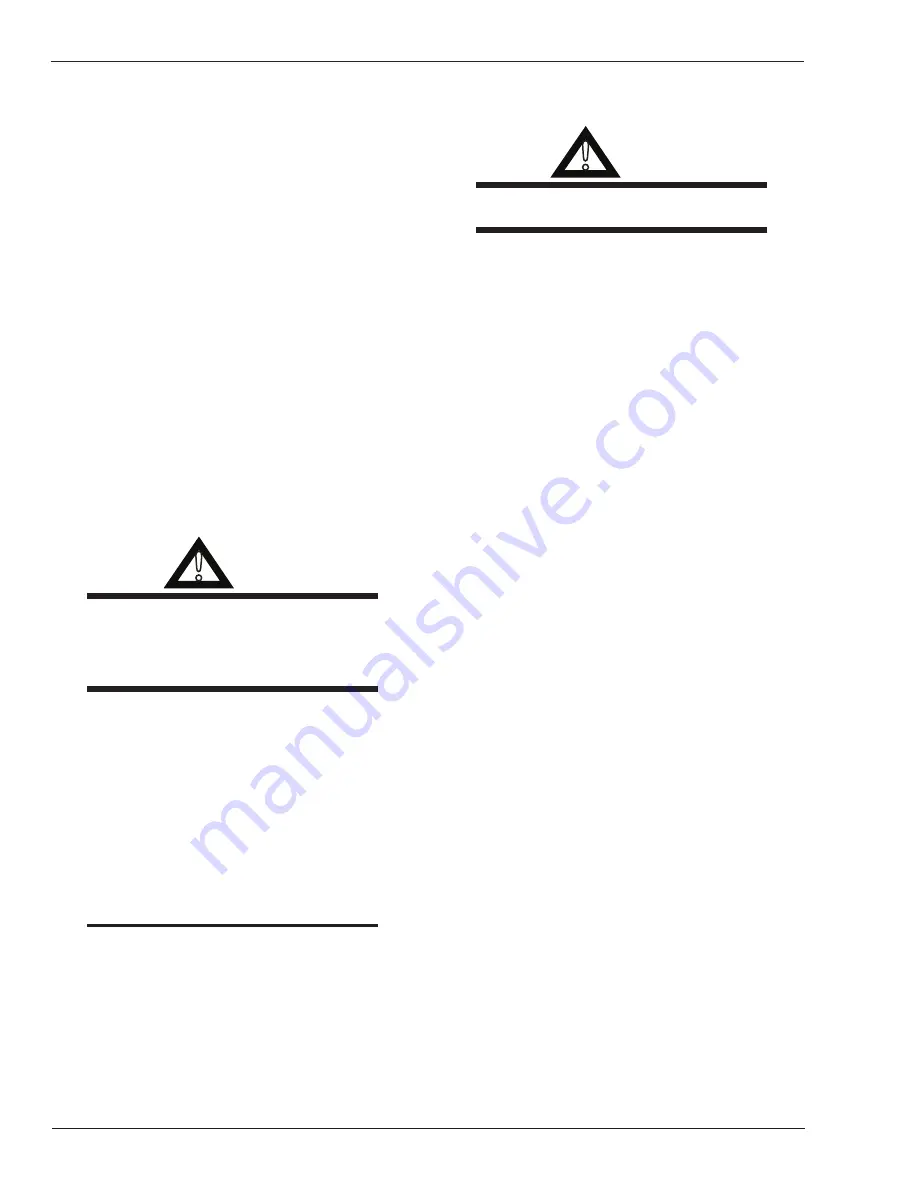
FIREpOwER Fp-95
OpERATION
Manual 0-5122
4-4
Operation
4.03 Flux Cored Arc Welding (FCAW)
See Welding Guidelines included in this manual.
1. Make all necessary connections as instructed in
the INSTALLATION chapter.
2. Place the WELDING OUTPUT VOLTAGE SELECTOR
at the desired setting.
3. Rotate the WIRE SPEED FEED control to the de-
sired setting.
4. Plug the supply cord into a 120 VAC 20 Ampere
receptacle.
5. Connect the WORK CLAMP to the workpiece
(material to be welded).
6. Extend wire from the gun, and cut to proper stick-
out for that type of wire (when welding always
maintain this distance).
7. Position gun to where it is at approximately right
angles to the workpiece with proper wire stick-
out. Lower your welding helmet and pull the gun
trigger switch.
!
WARNING
Be sure to put on proper protective clothing and eye safe-
guards (welding coat, apron, gloves, and welding helmet
with proper lenses installed). See Safety Instructions and
Warnings chapter included in this manual. Neglect of
these precautions may result in personal injury.
Travel at a speed necessary to maintain a bead width from
1/8" to ¼" (3mm to 6mm) depending on the thickness of
the material. For material that may require larger weld-
ments, either change to a larger diameter filler wire or use
multi pass beads. On some applications, it may be neces-
sary to adjust the voltage range to stabilize the arc.
Upon completion of the weld, release the gun trigger
switch, raise the welding helmet, and visually examine
the weld.
NOTE
To help you overcome any problems that might arise,
you will find useful information in section 4.05 Basic
Welding Techniques.
4.04 Shutdown Procedures
Place the POWER ON/OFF SWITCH in the OFF position.
!
WARNING
After releasing the gun switch, the electrode wire will
remain electrically “hot” for several seconds.
4.05 Basic Welding Technique
General
Two different welding processes are covered in this
section, with the intention of providing the very basic
concepts in using the semi-automatic mode of welding.
In this mode, the welding gun is hand-held. The electrode
(welding wire) is then fed into a weld puddle and the arc
is shielded by a gas or gas mixture.
Setting of the power Supply
The settings of the FP 95 requires some practice by the
operator in that the welding Power Supply has two control
settings that need to balance. These are the Wire Speed
control and the Voltage Control switches. The welding
current is determined by the Wire Speed control (i.e., the
current will increase with increased wire speed, resulting
in a shorter arc). Slower wire speed will reduce the cur-
rent and lengthen the arc. Increasing the welding voltage
hardly alters the welding current level, but lengthens the
arc. By decreasing the voltage, a shorter arc is obtained
with little change in welding current.
When changing to a different electrode wire diameter,
different control settings are required. A thinner electrode
wire needs more wire speed to achieve the same current
level.
A satisfactory weld cannot be obtained if the wire speed
and voltage switch settings are not adjusted to suit the
electrode wire diameter and dimensions of the work
piece.
If the wire speed is too high for the welding voltage,
“stubbing” will occur as the wire dips into the molten pool
and does not melt. Welding in these conditions normally
produces a poor weld due to lack of fusion. If however,
the welding voltage is too high, large drops will form on
the end of the electrode wire, causing spatter. The cor-
rect setting of voltage and wire speed can be seen in the
shape of the weld deposit and heard by a smooth regular
arc sound.