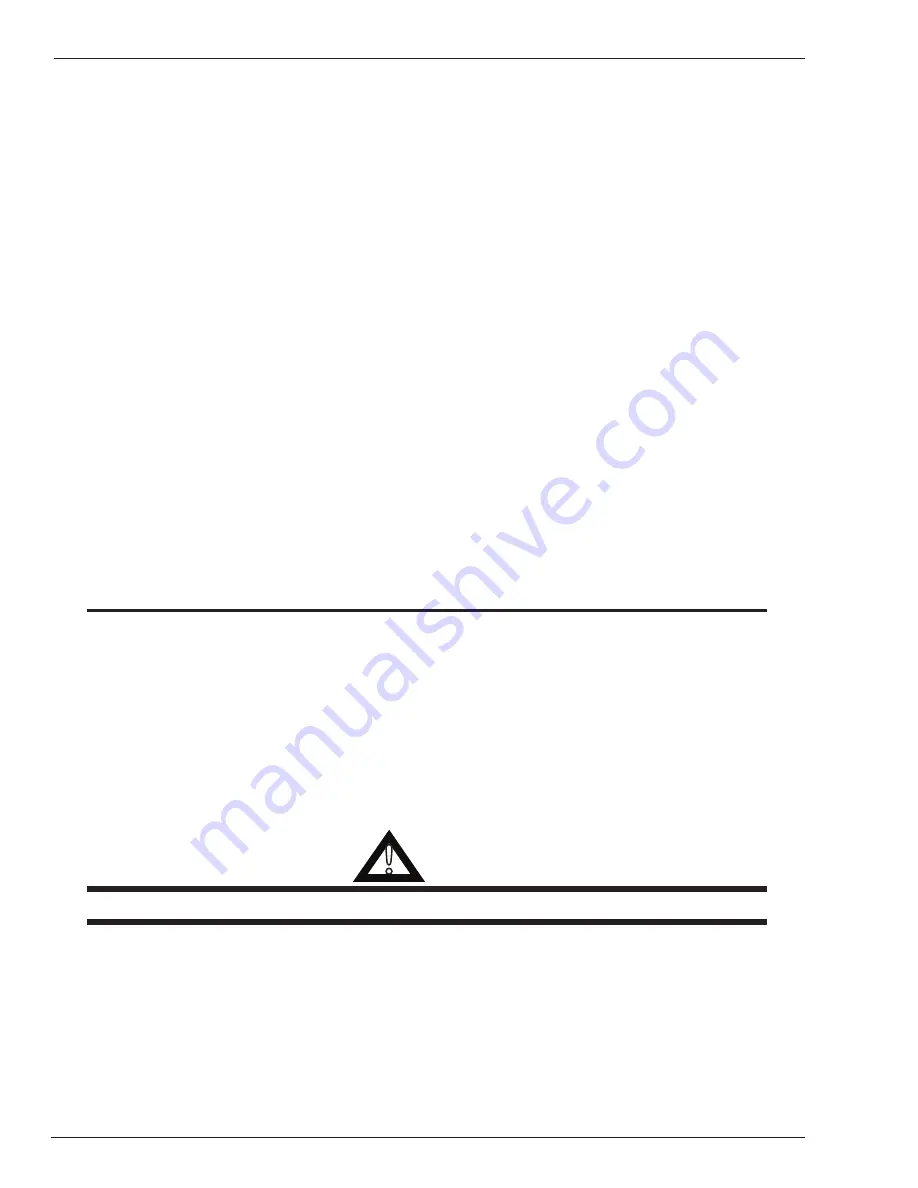
FABRICATOR 211i
INSTALLATION/SETUP
INSTALLATION/SETUP
3-14
Manual 0-5157
13. Process Selection Control
The process selection control is used to select the desired welding mode. Three modes are available, MIG (GMAW/
FCAW), LIFT TIG (GTAW) and STICK (SMAW) modes. Refer to section 3.18 or 3.19 for MIG (GMAW/FCAW) set
up details, section 3.21 for LIFT TIG (GTAW) set-up details or section 3.22 for STICK (SMAW) set-up details.
Note that when the unit is powered off the mode selection control will automatically default to MIG mode. This is
necessary so as to prevent inadvertent arcing should an electrode holder be connected to the unit and mistakenly
be in contact with the work piece during power up.
14. Digital Voltage Meter (Right Digital Display)
MIG Mode
This digital meter is used to display the pre-set (preview) Voltage in MIG mode and actual welding voltage of the
power source when welding. At times of non-welding, the digital meter will display a pre-set (preview) value of
Voltage. This value can be adjusted by varying the Multifunction Control Knob (10).
STICK and LIFT TIG Modes
This digital meter is used to display the Welding Output Terminal Voltage in STICK / LIFT TIG modes during non-
welding or welding. This value cannot be adjusted by varying the Multifunction Control Knob (10).
When welding, this digital meter will display actual welding voltage in all modes.
At the completion of welding, the digital meter will hold the last recorded voltage value for a period of approxi-
mately 10 seconds in all modes. The voltage meter will hold the value until; (1) any of the front panel controls are
adjusted in which case the unit will revert to preview mode, (2) welding is recommenced, in which case actual
welding amperage will be displayed, or (3) a period of 10 seconds elapses following the completion of welding in
which case the unit will return to preview mode.
NOTE
The preview functionality provided on this power source is intended to act as a guide only. Some differ-
ences may be observed between preview values and actual welding values due to factors including the
mode of welding, differences in consumables/gas mixtures, individual welding techniques and the transfer
mode of the welding arc (ie dip versus spray transfer). Where exact settings are required (in the case of
procedural work), it is recommended that alternate measurement methods be utilized to ensure output
values are accurate.
15. Gas Inlet (MIG mode only for MIG Gun or Spool Gun operation)
The Gas Inlet connection,5/8-18 UNF female thread is used to supply the appropriate MIG welding gas to the
Power Source. Refer to section 3.18 or 3.19 for MIG (GMAW/FCAW) set up details
!
WARNING
Only Inert Shielding Gases specifically designed for welding applications should be used.
16. On / Off Switch
This Single Phase circuit breaker performs a dual function.
It is used to turn the unit on/off and it will also trip in the event of a fault.
Содержание 211i
Страница 6: ......
Страница 32: ...FABRICATOR 211i INTRODUCTION INTRODUCTION 2 8 Manual 0 5157...
Страница 82: ...FABRICATOR 211i BASIC WELDING BASIC WELDING 4 22 Manual 0 5157...
Страница 92: ...FABRICATOR 211i REPLACEMENT PARTS REPLACEMENT PARTS 6 4 Manual 0 5157...