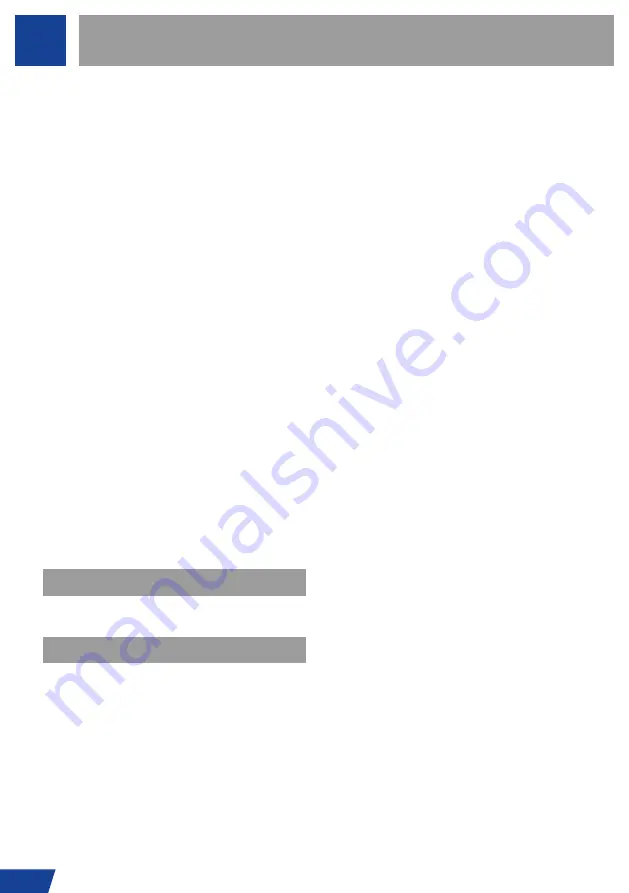
14
strictly observing the instructions, or else by the
manufacturer, and it must, whenever necessary, be
replaced. These inspections must be documented
(documentation of equipment; cf. attached Inspec-
tion Sheet). Refer to national regulations for inspec-
tion intervals.
This inspection must comprise:
�
Inspection of the general condition: age,
completeness, dirt, correct composition.
�
Inspection of the labels: Does it exist? Is it
legible? (CE marking, manufacturing date, serial
number EN standard, manufacturer, designation
of product)
�
Inspection of the individual parts for mechanical
damage such as cuts, cracks, notches,
abrasion, deformation, ribbing, curling,
squashing.
�
Inspection of all individual parts for damage
caused by heat or chemicals, such as fusion or
hardening.
�
Inspection of the metal parts for corrosion and
deformation.
�
Inspection of the completeness of the end
connections, seams, knots.
�
Inspection of all harness closures for their flaw
less function (e.g. proper locking)
Here, too,
if there is the slightest doubt, the prod-
uct must be with drawn or inspected by an expert.
MAINTENANCE
Only the manufacturer is permitted to carry out re-
pairs.
SERVICE LIFE
Only if the rope is rarely used (one week a year)
and Products made of plastic or textile materials
must be discarded no later than 11 years from their
date of manufacture (1 year in storage prior to their
first use + a maximum use period of 10 years) The
maximum storage period prior to first use that will
not cause a reduction of the maximum use period
is 1 year from the date of manufacture. In the event
of infrequent use, flawless condition, and proper
storage of the product (see chapter Transport,
Storage, and Cleaning), the use period for textile
safety products manufactured in-house can be
up to 10 years from the date of first use (the date
of first use must be documented in the relevant
inspection records). Intensive use will reduce the
period of possible use significantly. The determining
factor for its length is the respective condition of
the product at the time of the required inspections,
taking all defined inspection and discard criteria into
account. It is impossible to make a generally valid
statement about the service life of the product, as
it will depend on various factors such as storage
conditions, mechanical wear, UV radiation, intensity
and frequency of use, maintenance/ care, weather
conditions such as temperature, moisture, snow, or
environmental influences due to salt, sand, chem-
icals, etc. Bleached or abraded fibers/webbing,
discoloration and hardening are sure signs that the
product should be withdrawn from use. Unusual cir-
cumstances may reduce the equipment’s service life
to a single use; it is also possible that it becomes
unusable even before its first use (e.g., in case of
damage in transit).
Damaged systems or systems already subject-
ed to a fall must be withdrawn from use imme-
diately!
Generally, the following rules apply:
If for what-
ever reason, no matter how insignificant it may
seem, the user is not certain that the product sat-
isfies the requirements, it must be withdrawn from
use and inspected by a competent professional.
Discard any product that shows signs of wear!
MAINTENANCE / SERVICE LIFE