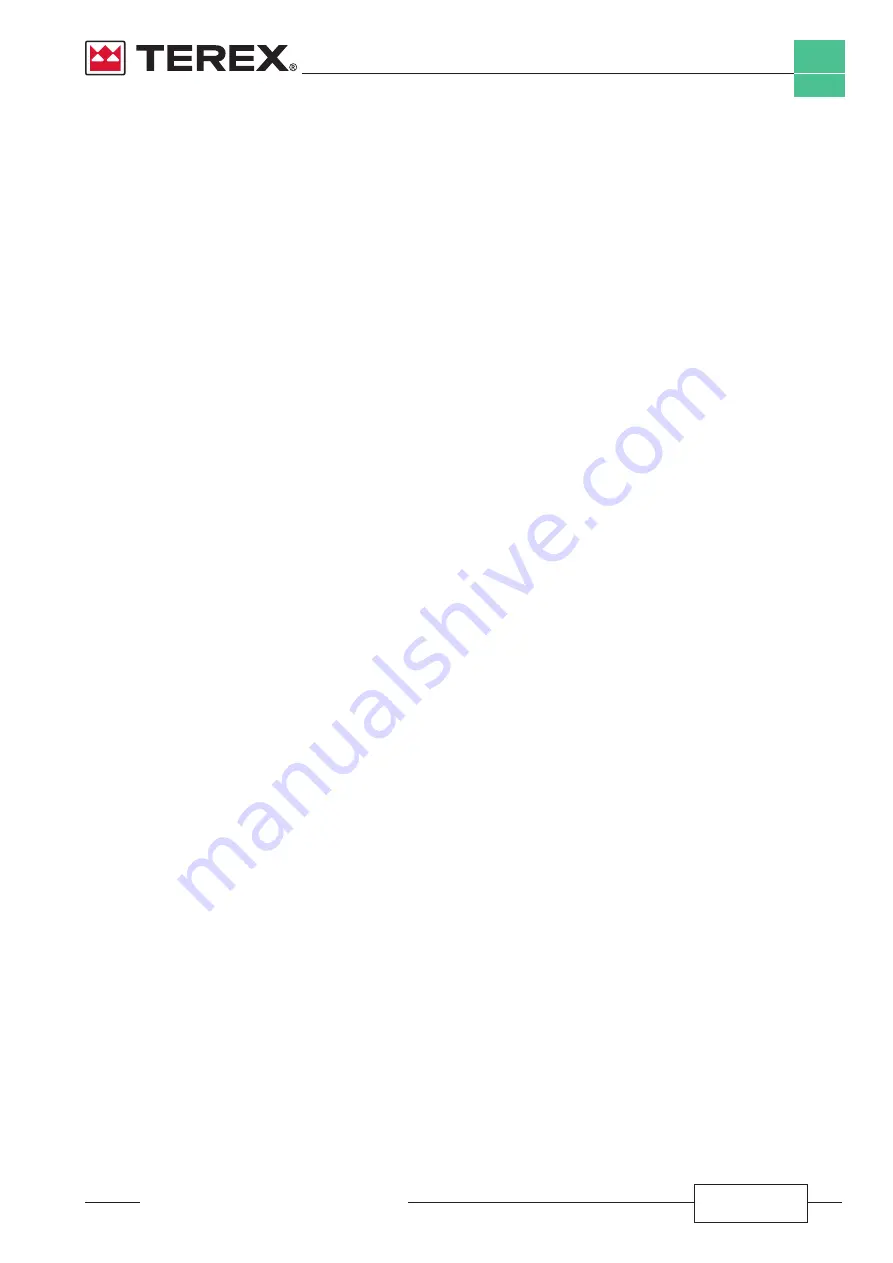
TELELIFT 3713 SX
TECHNICAL SPECIFICATIONS
41
Document 57.4402.9200 - 1
st
Edition 10/2006
INDEX
8.
CHECKS AND INSPECTIONS
1) Checking the overload system power supply:
•
Check the supply voltage (12÷14.5 V) between pins
6
(+) and
5
(-) on connector
B
.
2) Checking the load cell excitation voltage:
•
Check the load cell excitation voltage (from 4.75 V
to 5.25 V) between pins
(+) and
4
(-) on connector
B
.
3) Checking connections on the main module:
•
Remove connector
B
from the main module.
•
Ensure all wires are hooked up on the connector
exactly as shown on the electrical schematic.
•
Gently pull on each wire, to make sure they are
securely fastened on the connector.
•
Check every wire for nicks, cuts or abrasions.
4) Checking the load cell connections:
•
Remove connector
B
from the main module (always
remember to cut off main power before removing or
inserting the connector).
•
Set the multimeter on the resistance (“ohm”Ω)
range; the measured resistance between pins
1
and
should be 351 ± 5 Ω. Between pins
and
4
the
measured resistance should be 350 ±20 Ω. If this is
not the case, a broken wire in the load cell cable or
a defective load cell could be the problem.
•
Check for electrical continuity between the shield of
the load cell cable and chassis ground.
•
Ensure every wire from the load cell is insulated
from ground: the reading must show resistance
greater than 20 MΩ. Smaller measured values can
be caused by a damaged insulation (usually a result
of arc-welding): replace the load cell.
5) Checking the weight applied on the load cell:
•
Remove any load from the forks, retract the boom
all the way and place the machine on a hard, level
surface.
•
Set the multimeter on the 200 mV range and measure
the output of the load cell, between pins
(+) and
1
(-) on connector
B
:
-
If the voltage is negative, the load cell signal wires
(white and green) must be inverted.
-
If the voltage exceeds 1.3 mV, go to step 6.
-
If the voltage does not exceed 1.3 mV, calculate the
corresponding weight (see Appendix A) and make
sure it does not exceed the maximum weight on the
rear axle (see the identification plate on the machine).
If the maximum rear axle weight is exceeded, go to
step 6.
•
If, after checking the rear axle, the problem still
persists, a defective load cell is likely.
6) Checking mechanical components:
•
Ensure the oscillation of the rear axle is not restricted
by any part or object.
•
Check the correct axial positioning of the load cell.
The cell should not have any longitudinal play. If this
occurs, tighten the locking ring.
•
Ensure there is no axial play between load cell and
axle support, and between load cell and chassis.
•
Lubricate the load cell bushings (see Operator
Handbook).
Содержание Telelift 3713 SX
Страница 4: ...Courtesy of Crane Market...
Страница 200: ...6 6 INDEX TELELIFT 3713 SX SCHEMATICS Document 57 4402 9200 1st Edition 10 2006 Y21 Y20 Courtesy of Crane Market...
Страница 202: ...6 8 INDEX TELELIFT 3713 SX SCHEMATICS Document 57 4402 9200 1st Edition 10 2006 Y01 Y02 B56 Courtesy of Crane Market...
Страница 205: ...6 41 INDEX TELELIFT 3713 SX SCHEMATICS Document 57 4402 9200 1st Edition 10 2006 22 23 30 32 31 Courtesy of Crane Market...