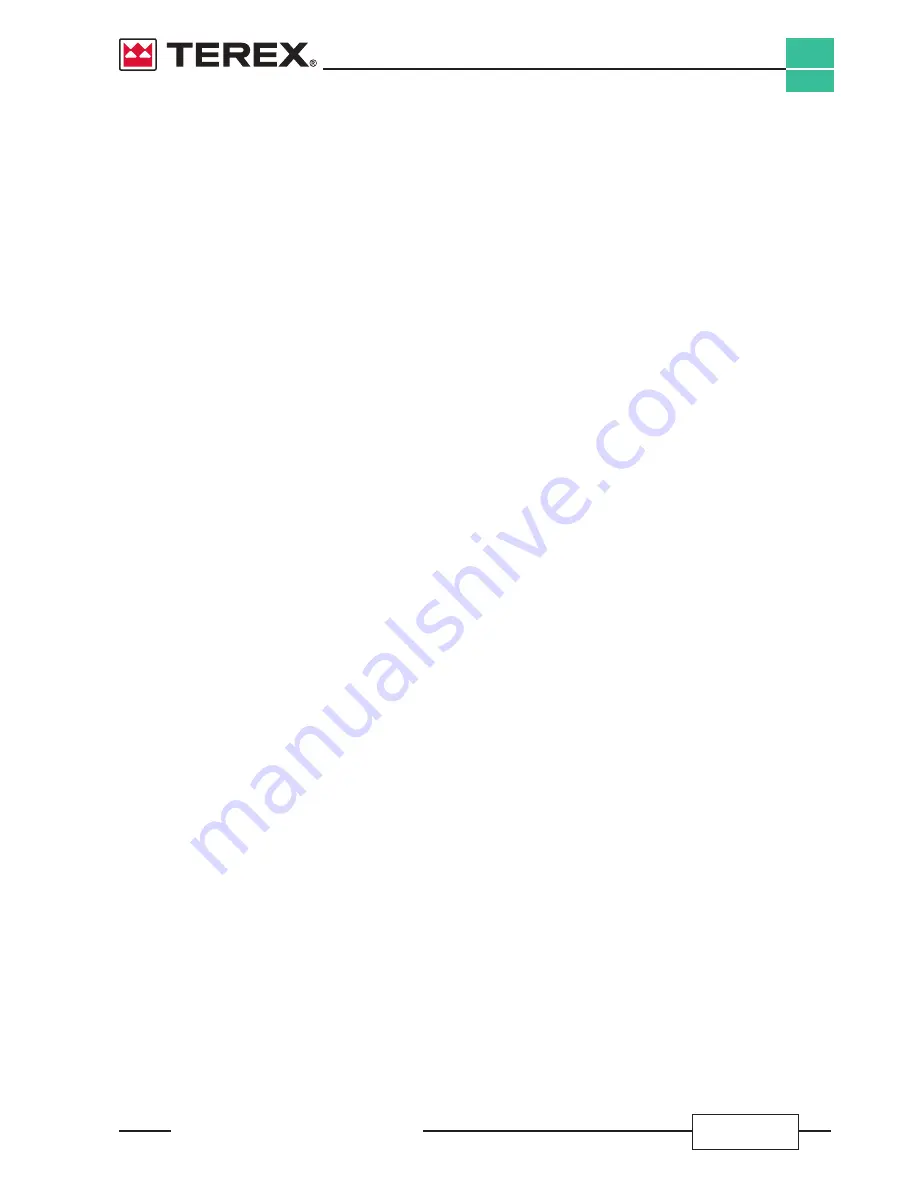
Document 57.4402.8200 - 1
st
Edition 03/2007
INDEX
v
GYRO 4020 - 4518
INTRODUCTION
its turn, receives an analog pressure signal from the
hydraulic drive (
7
). The exchange valve (
10
) is then
connected to the "load sensing" port of pump (
3
), thus
guaranteeing the adaptation of the pump adjustment to
the maximum load on the various users served by this
pump under any conditions.
The pressure relief valve (
11
) calibrated to 30 bar is
placed upstream of the pressure inlet port of the main
valve (
8
). This valve is used to deliver low-pressure oil
(30 bar) to the anti-cavitation circuits of automatic fork
levelling system and to feed the pilot line of the same
main valve (
8
).
The block cylinder of the slewing turntable (
28
) is
equipped with a double one-way valve (
29
) with hydraulic
release, acting as safety valve, and is controlled by the
4-way/3-position solenoid valve of the on/off type (
30
).
As already mentioned, the turntable lock/unlock is
possible through the simultaneous energisation of
module n.4 of the main valve (
8
), the electric divider
(
22
) and the solenoid valve (
30
).
The SAFIM S6 servo-assisted braking system with pedal
(
35
) receives oil from the pump (
4
) and uses this oil to
pressurise 3 hydraulic accumulators (
36
-
37
) connected
to the same system.
The oil at pressure contained in these accumulator is
then used to operate the service brakes of the two axles
(
57
-
58
) and to release the parking brake located inside
the rear axle (
58
).
The fill valve inside the braking system takes the flow
from the feeding line so the pressure on the line of the
accumulators reaches the calibration value of the cutout
valve set to 140 bar. When this pressure is reached, the
valve gradually releases all the flow to line B for other
uses.
The brake pedal located in the driving cab, which is an
integral part of the braking system S6, is connected to
two proportional sliders which control the two separated
lines of the service brake, one for each axle.
Such lines connect the part of circuit in the turntable with
the one in the undercarriage through ports n. 5 and n. 6
of the hydraulic rotary joint (
9
). In relation to the stroke
of these sliders, a gradual communication between
the feeding line, connected to two accumulators (
36
)
which, at their turn, are connected to ports R1 and R2
(the accumulators have 0.5-lt. capacity and 50 bar fill
pressure), and the service brake lines is established so
the flow is distributed to such lines and the discharge
line increasing, in this way, the pressure (and as a result
the braking force) on the lines of the service brakes.
When the sliders are in the rest position, the lines of the
service brakes are connected to the discharge.
The pressure switch (
38
) set to 2-10 bar, paralleled to on
of the two lines of the service brake, sends an electrical
signal when this brake is engaged.