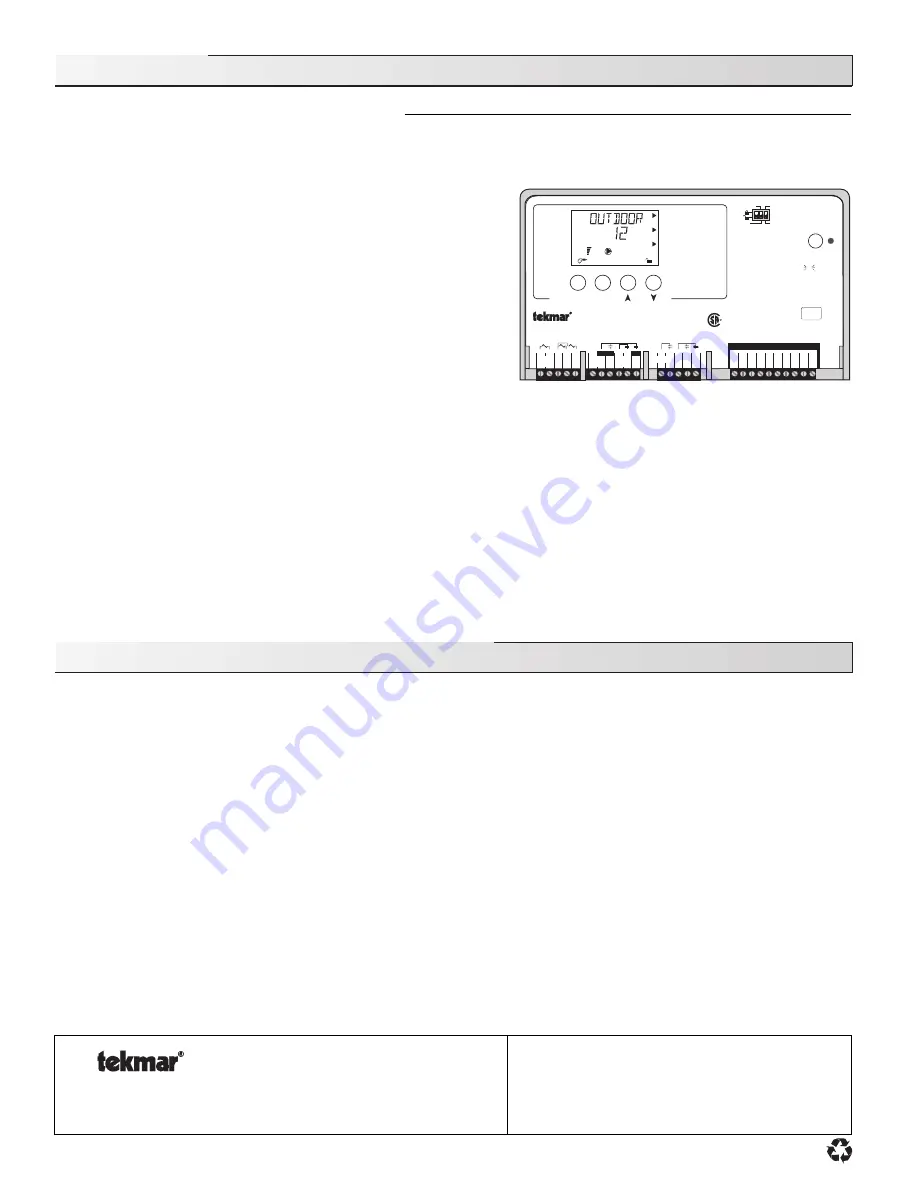
The installer must ensure that this control and its wiring are isolated and/or shielded from strong sources of electromagnetic noise.
Conversely, this Class B digital apparatus complies with Part 15 of the FCC Rules and meets all requirements of the Canadian
Interference-Causing Equipment Regulations. However, if this control does cause harmful interference to radio or television reception,
which is determined by turning the control off and on, the user is encouraged to try to correct the interference by reorienting or relocating
the receiving antenna, relocating the receiver with respect to this control, and/or connecting the control to a different circuit from that
to which the receiver is connected.
Cet appareil numérique de la classe B respecte toutes les exigences du Règlement sur le matériel brouilleur du Canada.
Caution
The nonmetallic enclosure does not provide grounding between conduit connections. Use grounding type bushings and jumper
wires.
Attention
Un boîtier nonmétallique n’assure pas la continuité électrique des conduits. Utiliser des manchons ou des fils de accord
spécialement conçus pour la mise á la terre.
Universal Reset Control 363
Mixing, Boiler & DHW
Literature
— D 363, A 363’s, D 001, D 070, E 003, E 021, U 363.
Control
— Microprocessor PID control; This is
not a safety (limit) control
.
Packaged weight
— 3.9 lb. (1760 g), Enclosure A, blue PVC plastic
Dimensions
— 6-5/8” H x 7-9/16” W x 2-13/16” D (170 x 193 x 72 mm)
Approvals
— CSA NRTL/C, meets ICES & FCC regulations for EMI/RFI.
Ambient conditions
— Indoor use only, 32 to 122
°
F (0 to 50
°
C), < 95% RH non-con-
densing.
Power supply
— 120 V
±
10% 50/60 Hz 1800 VA
Relays
— 240 V (ac) 7.5 A 1/3 hp, pilot duty 240 VA
Var. Pump
— 240 V (ac) 2.4 A 1/6 hp, fuse T2.5 A 250 V
Demands
— 20 to 260 V (ac) 2 VA
Sensors included
— NTC thermistor, 10 k
Ω
@ 77
°
F (25
°
C
±
0.2
°
C) ß=3892
Outdoor Sensor 070 and 2 of Universal Sensor 071.
Optional devices
— tekmar type #: 011, 031, 040, 062, 063, 070, 071, 072, 073, 076,
077, 367, 368.
40 of 40
Limited Warranty The liability of tekmar Control Systems Ltd. and tekmar
Control Systems, Inc. (“tekmar”) under this warranty is limited. The purchaser,
by taking receipt of the tekmar product (“product”), acknowledges receipt of
the terms of the warranty and acknowledges that it has read and
understands same.
tekmar warrants each tekmar product against defects in workmanship and materi-
als, if the product is installed and used in compliance with tekmar's instructions. The
warranty period is for a period of twenty-four (24) months from the production date
if the product is not installed during that period, or twelve (12) months from the
documented date of installation if installed within twenty-four (24) months from the
production date.
The liability of tekmar under this warranty shall be limited to, at tekmar's sole dis-
cretion: the cost of parts and labor provided by tekmar to repair defects in materials
and/or workmanship of the defective product; or to the exchange of the defective
product for a replacement product; or to the granting of credit limited to the original
cost of the defective product, and such repair, exchange or credit shall be the sole
remedy available from tekmar, and, without limiting the foregoing in any way,
tekmar is not responsible, in contract, tort or strict product liability, for any
other losses, costs, expenses, inconveniences, or damages, whether direct, indi-
rect, special, secondary, incidental or consequential, arising from ownership or use
of the product, or from defects in workmanship or materials, including any liability
for fundamental breach of contract.
This warranty applies only to those products returned to tekmar during the
warranty period. This warranty does not cover the cost of the parts or labor
to remove or transport the defective product, or to reinstall the repaired or
Limited Warranty and Product Return Procedure
replacement product. Returned products that are not defective are not cov-
ered by this warranty.
This warranty does not apply if the product has been damaged by negligence
by persons other than tekmar, accident, fire, Act of God, abuse or misuse; or
has been damaged by modifications, alterations or attachments made sub-
sequent to purchase which have not been authorized by tekmar; or if the
product was not installed in compliance with tekmar’s instructions and the
local codes and ordinances; or if due to defective installation of the product;
or if the product was not used in compliance with tekmar’s instructions.
This warranty is in lieu of all other warranties, express or implied, which the
Governing Law (being the law of British Columbia) allows parties to contrac-
tually exclude, including, without limitation, warranties of merchantability,
fitness for a particular purpose, durability or description of the product, its
non-infringement of any relevant patents or trademarks, and its compliance
with or non-violation of any applicable environmental, health or safety legis-
lation; the term of any other warranty not hereby contractually excluded is
limited such that it shall not extend beyond twenty-four (24) months from the
production date, to the extent that such limitation is allowed by the Govern-
ing Law.
Product Return Procedure
Products that are believed to have defects in work-
manship or materials must be returned, together with a written description of the
defect, to the tekmar representative for that territory. If the address of the repre-
sentative is not known, please request it from tekmar at the telephone number
listed below
.
All specifications are subject to change without notice.
Printed in Canada on recycled paper. D 363 -06/99.
Product design, software and literature are Copyright © 1999 by:
tekmar Control Systems Ltd. and tekmar Control Systems, Inc.
Control Systems
tekmar Control Systems Ltd., Canada
tekmar Control Systems, Inc., U.S.A.
Head Office: 4611 - 23rd Street
Vernon, B.C. Canada V1T 4K7
Tel. (250) 545-7749 Fax. (250) 545-0650
Web Site: www.tekmarcontrols.com
Technical Data
°
F
1
View
2
1
%
7
Power
120 V
±
10% 50/60 Hz 2000 VA
Relays
240 V (ac) 7.5 A 1/3 hp, pilot duty 240 VA
Var. Pump
240 V (ac) 2.4 A 1/6 hp, fuse T2.5 A 250V
Demands
20 to 260 V (ac) 2 VA
Made in Canada by
tekmar Control Systems Ltd.
Test
not testing
testing
testing paused
off
red
red
2
3
1
Com
Dem
4
Mix
Demand
Boil
P1
13
Pwr
Mix
15
Power
N L
18
Com
19
tN1/
tN2
20
10K
2
21
10K
1
22 23
Com
24
Mix
25
Boil
Universal Reset Control 363
Mixing, Boiler & DHW
Signal wiring must be rated at least 300 V.
6
10
12
14
16
Boiler
Opn Cls/
Var
DHW
Pmp / Vlv
Boil
Dem
Setp/
DHW
Mix Demand
Boiler Demand
DHW Demand
Setpoint Demand
WWSD
Minimum
Maximum
5
R
Do not apply power
Menu
Item
Reset Ratio
Setback
Characterized
Heating Curve
None
Mix
P2
8
11
9
17
Com
UnO
Sw
26
Out
DHW
For maximum heat,
press and hold
Test
button for 3 seconds.
C US
LR 58223
Содержание Universal Reset Control 363
Страница 39: ...39 of 40 Copyright D 363 06 99 Notes...