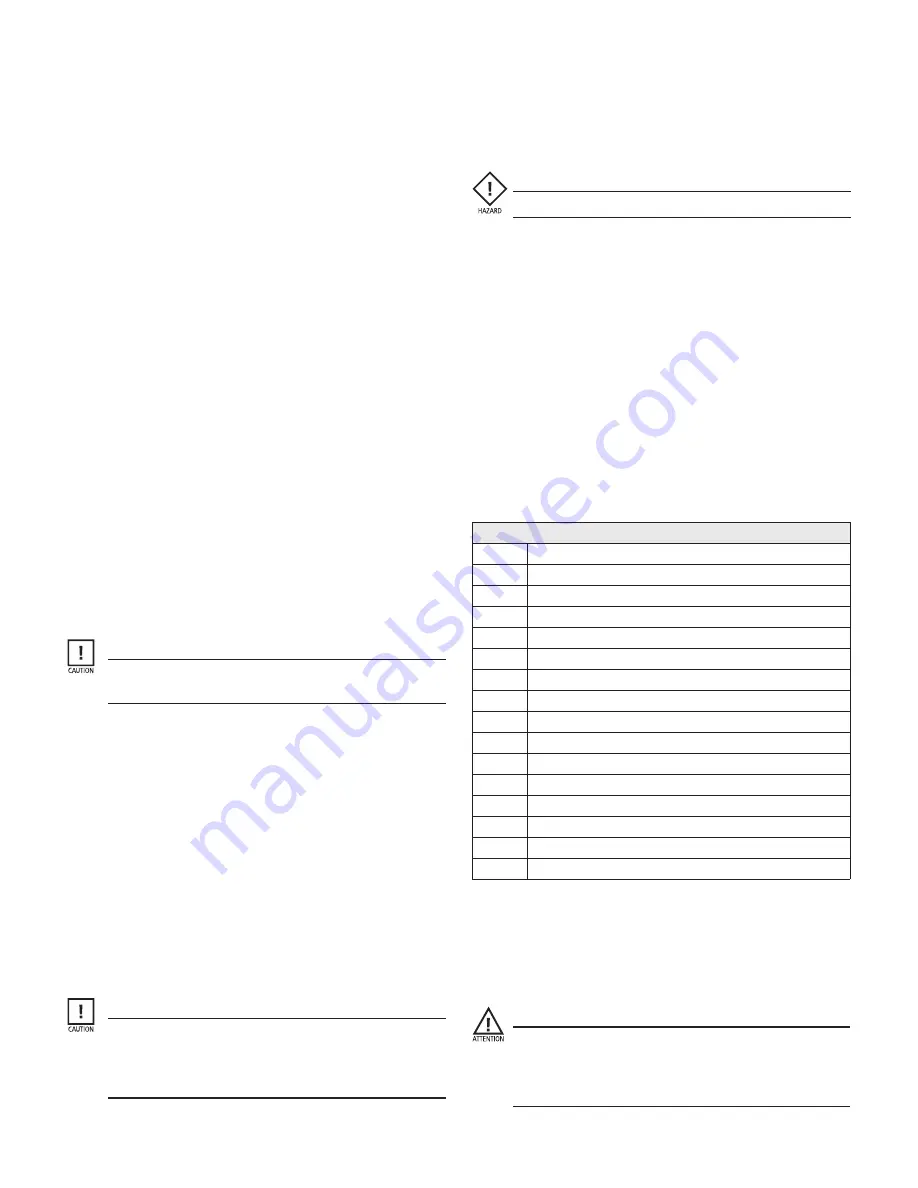
Teikoku USA | Chempump
Instruction Manual G-Series
20
3.3 Starting Procedure
After priming and checking the direction of rotation, put the
pump in operation as follows:
1. Set the valve in the suction line to 100% open.
2. Set the valve in the discharge line to 20% open.
3. Start the pump. Pump should operate with very low noise and
vibrations. Excessive or abnormal noise or vibrations should
be corrected immediately.
4. Open discharge valve to desired flow position.
5. Care should be taken in process design to assure there can be
no operation at shutoff or deadhead conditions (zero flow).
All canned motor pumps require a minimum flow that assures
adequate motor cooling circulation. Minimum flow values by
model from laboratory tests on water are provided in
Appx.
C., Page 31
. Minimum flow requirements will very based on
the fluid pumped and its pumping temperatures. Please con-
sult the factory for any application specific guidance on mini-
mum flow that may be required.
Once pump is operational, check the reading of the TRG meter.
Record initial reading for comparison to future readings. See
Table
2-1
.
6. During any startup sequence, caution must be exercised not
to exceed full load ampere rating indicated on the nameplate.
7. If the unit has not been run for a period of two weeks or
more, the following inspections should precede its operation:
A. Check terminal box for moisture.
B. Upon starting, check for excessive noise, vibration, erratic
speeds or excessive amp draw.
Caution!
The pump should not be allowed to run for more than one
minute with the discharge valve fully closed.
NOTES:
1.
If the suction and discharge lines are completely filled with
system fluid and adequate suction head is available the pump
can be started without closing the discharge valve. During any
startup sequence, caution must be exercised not to exceed full
load amperage rating indicated on the nameplate.
2.
If the unit has not been run for a period of two weeks or more,
the following inspections shall precede its operation:
a)
Check secureness of base hold down bolts if supplied.
b)
Check terminal box for moisture and tightness
of fittings.
c)
Upon starting, check for excessive noise, vibration, or
erratic speeds.
Caution!
If the pump appears to be airbound as a result of the unit
not being properly primed, do not continue operation. Lo-
cate and correct the conditions that prevent proper prim-
ing before attempting to start the unit.
3.4 Operation Details
TRG Meter should be checked periodically during operation. If
the initial reading (TRG) was not recorded, then the color coding
system shown in
Table 2-1
may be used to determine bearing
changing intervals.
Hazard!
Do not operate if TRG meter conditions is RED.
Discharge pressure should be checked frequently during opera-
tion. Pressure should be stable in a non-variable closed loop al-
though the discharge pressure gauge needle may show small
fluctuations. Check motor amps at normal operations. Verify mo-
tor amps are within the expected range. Pump should never be
operating above the rated full load amps listed on the nameplate.
In some cases, the liquid supply may contain an excessive amount
of air or gas, which will tend to separate from the liquid and re-
main in the passages of the pump. This results in the pump losing
its prime and becoming air bound with marked reduction in ca-
pacity. The discharge pressure gauge will show large fluctuations
if this occurs. Stop the pump and vent per
Section 3.2.1
.
If any abnormal noise or vibration is observed, stop the pump and
check for the possible causes, see
Appx B. Troubleshooting
.
Table 3-1 Minimum Flow
Model
Minimum Flow (GPM)
GA
6
GB
7.5
GC
20
GVBS
20
GVD
25
GVE
45
GVHS
22
GG
65
GKS
55
GK
90
GVM
60
GN
75
GP
75
GS
140
GRS
250
3.5 Shutdown Procedure
Shutdown as follows:
1. Stop the pump (de-energize the motor).
2. If pump is to be removed from service, shut all valves.
Attention!
If the pump is to be shut down for a long period of time
or if there is danger of freezing, after stopping the pump,
shut all valves and drain the entire pump and connected
piping.