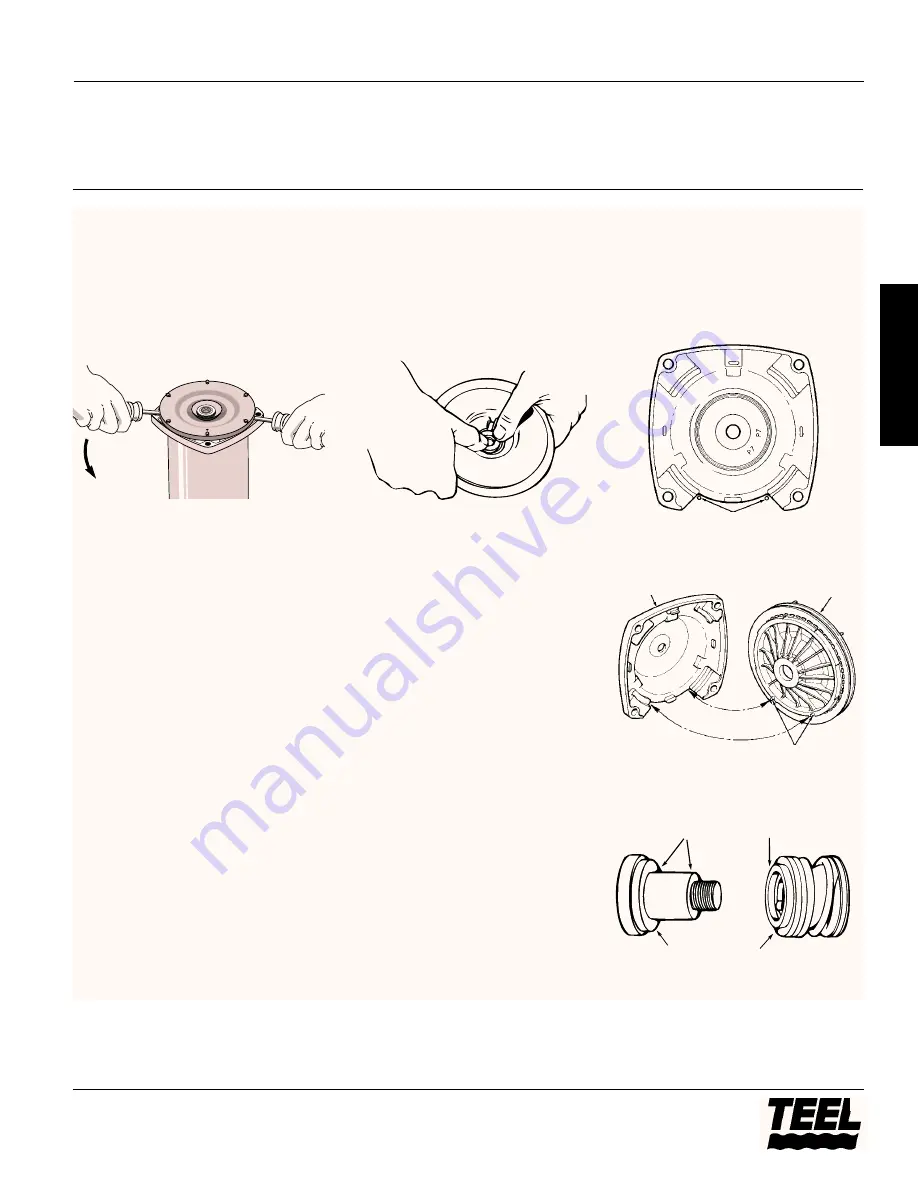
Maintenance (Continued)
2. Follow steps 1 through 5 under
“Cleaning/Replacing Impeller.”
3. Remove rotating half of seal by
placing two screwdrivers under seal
plate and carefully prying up (Figure
15). Seal plate will slide off shaft,
bringing seal with it.
IMPORTANT:
Be sure you do not
scratch or mar shaft; if shaft is marred,
it must be dressed smooth with fine
emery or crocus cloth before installing
new seal. DO NOT reduce shaft
diameter.
4. Place seal plate face down on flat
surface and tap out stationary half
of seal.
IMPORTANT:
Be sure you tap on the
ceramic seat, not on copper heat sink.
Do not disturb heat sink (Ref. No. 4,
Figure 29).
INSTALLING NEW SEAL
1. Clean seal cavity in copper heat sink.
Do not disturb heat sink. (If heat
sink is moved or dislodged, see
instructions for “Copper Heat Sink
Installation,” Page 12.
2. Wet outer edge of O-Ring on
ceramic seat with liquid soap. Be
sparing!
3. Put clean cardboard washer on seal
face. Polished face of ceramic seat
should be up. With thumb pressure,
press ceramic seal half firmly and
squarely into seal cavity in copper
heat sink (See Figure 16). If seal will
not seat correctly, remove, placing
seal face up on bench. Reclean
cavity. Seal should now seat
correctly.
4. If seal does not seat correctly after
recleaning cavity, place a cardboard
washer over polished seal face and
carefully press into place using a
piece of standard 3/4” pipe as a
press.
IMPORTANT:
Be sure you do not
scratch seal face.
5. Dispose of cardboard washer and
recheck seal face to be sure it is free
of dirt, foreign particles, scratches,
and grease.
6. Inspect shaft to be sure it is free of
nicks and scratches.
7. Reassemble seal plate to motor
flange. BE SURE it is right side up:
index pins should be down; seal
plate is marked at top (See Figures
17 and 18).
8. Apply liquid soap sparingly (one
drop is sufficient) to inside diameter
of rotating seal member.
9. Slide rotating seal member (carbon
face first) onto shaft until rubber
drive ring hits shaft shoulder.
IMPORTANT:
Be sure not to nick or
scratch carbon face of seal when
passing it over threaded shaft end and
shaft shoulder (See Figure 19). The
carbon surface must remain clean or
short seal life will result.
Models 3P683D, 3P684D, 2P899A and 3P715B
11
Teel Operating Instructions and Parts Manual
®
E
N
G
L
I
S
H
506 0194
Figure 15 – Pry Off Seal PLate
Figure 16 – Press In Seal
Figure 17 – Locate Seal Plate on Motor
Flange
Top of motor flange
Seal plate index pins slide in here
Figure 19 – Do Not Nick Seal On Shaft
Shoulder
Figure 18 – Locate Seal Plate On Motor
Flange
Motor flange
Seal plate
Index pins
Ceramic face
Be careful that
shaft shoulder. . . . . does not damage
seal faces
Carbon face