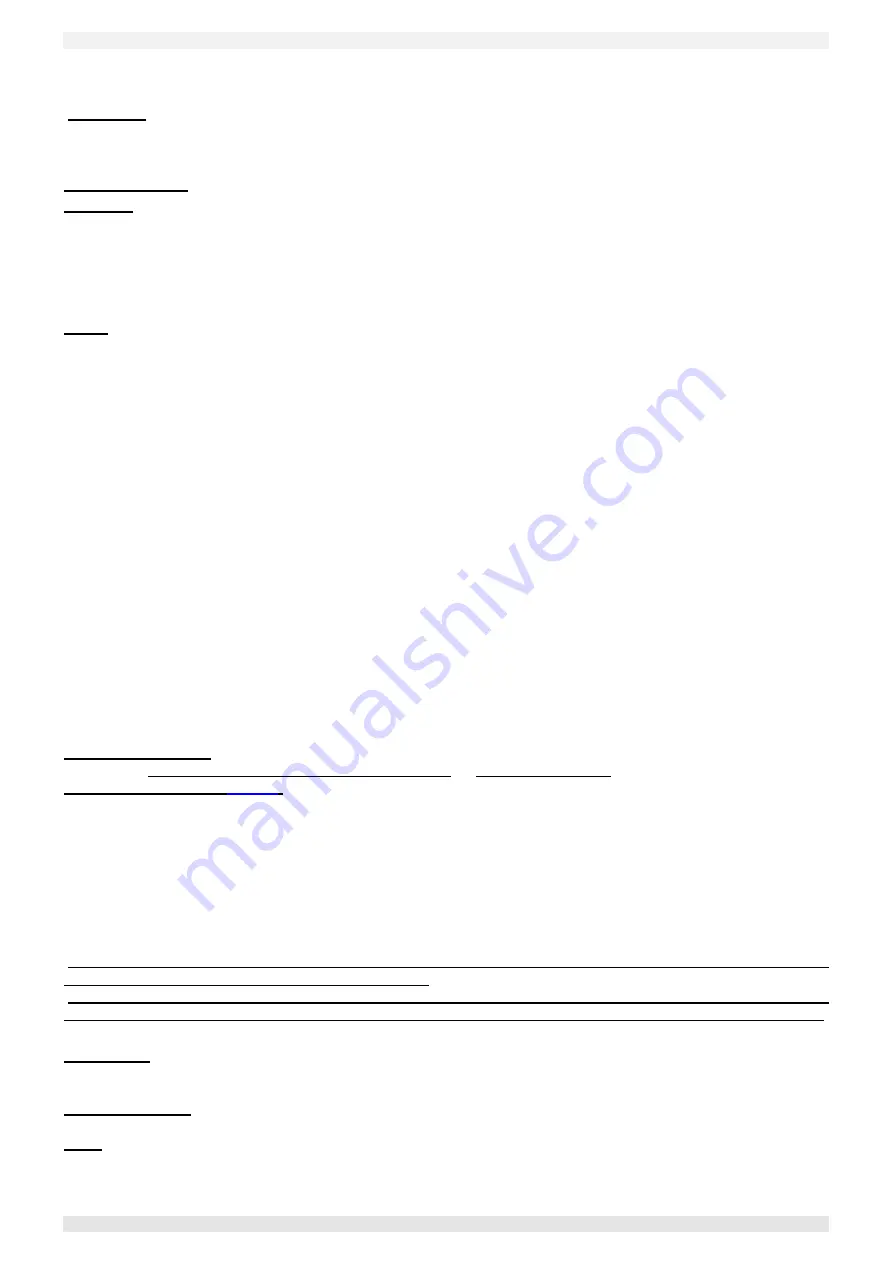
IST-2137.EO01.01/A
Istruzione / User’s Manual / Manuel d’utilisation
Pag.5/11
TECNOCONTROL S.r.l. Via Miglioli 47 SEGRATE ( MI )
Tel: 02/26 92 28 90 Fax: 02/21 33 734
OPERATIONAL DESCRIPTION
The electrochemical sensor is temperature compensated, but is sensitive to extreme humidity variations.
Preheating
: when powered, the sensor needs a time of preliminary heating of about 60 seconds. During this pe-
riod the yellow LED “
FAULT
” flashes. After this period, the yellow LED light off, the green LED “
ON
” illuminates to
indicate normal functioning. After this period the unit is able to detect gas even if it attains the optimum stability
conditions after about 15 minutes continual functioning.
Normal operation
: the green LED “
ON
” should be light on.
ALARMS:
different alarms levels can be set by Dip-Switch (
see table 2
).
The 1st° Red LED
(
ALARM 1
) illuminates when the Gas concentration attains 1st alarm level. And fter about 3
seconds the “ALARM 1" relay will activate.
The 2nd Red LED
(
ALARM 2
) illuminates when the Gas concentration attains 2nd alarm level and after about 3
seconds, the “ALARM 2" relay will activate.
The 3rd Red LED
(
ALARM 3
) illuminates when the Gas concentration attains 3rd alarm level and after about 3
seconds, the “ALARM 3" relay will activate.
Faults:
the instrument signal different kind of failures, as listed below. The Yellow LED illuminates, the "
S
" output
falls down to 0mA and the “
FAULT
”
normally activated relay deactivate. The "
FAULT
" relay, if necessary, can be
used both to signal remotely an occurred damage and to signal the absence of power to the instrument.
Yellow LED illuminates each 4 seconds (
with Green LED activate
):
this happens when the “
Cartridge Sensor
” has
overcome its theoretical period of life (2 years approximately) and its correct operation is not longer guaranteed.
The detector keeps on operating normally but it is necessary to replace, as soon as possible, the “
Cartridge Sen-
sor
” with a new one. The type to be required is described at
Page1
. The replacement procedure is described in the
attached manual.
Yellow LED activate, Green LED off (
FAULT relays activate and 0mA output signal
):
this signal different kind of
faults.
1)
The Dip Switch set up is wrong, please verify (
see Table 2
).
2)
The “
Cartridge Sensor
” is not working,
please replace with new one.
3)
If a new
“
Cartridge Sensor
” is installed or it is not correctly connected or a not
compatible one is mounted. Please check the cartridge connections and compatibility (
see Table 3
) these checks are
made connecting and disconnecting the device.
If the condition does not change, it will be necessary to replace the
unit and/or send it back to the supplier to repair.
Yellow and Green LED activates (
FAULT relays activate and 0mA output signal
):
this happens when the “
Cartridge
Sensor
” is not working. First try to perform the procedure of “
Calibration in Air
” as described in the section
“Test
and Calibration > Calibration in Air”
, finally try to replace a new
“Cartridge Sensor
”. If the condition is not
change, it will be necessary to replace the unit and/or send it back to the supplier to repair.
All LED activate (
FAULT relays activate and >24mA output signal
):
this happens when the “
Cartridge Sensor
” is not
working or gas concentration is out of scale (higher than 30%v/v O
2
). If there are not any gas leaks and the condi-
tion is not change, it will be necessary to replace the unit and/or send it back to the supplier to repair.
INSTALLATION
The detector must be accurately installed according to the national dispositions in force on the safety of the plants
and installation of electric devices.
Detector positioning:
The
Fig. 2
shows the instrument size. The unit must be positioned vertically with the sensor
downwards.
It should be fixed at 1.60 m from the floor (the O
2
gas is lighter as air).
Electrical Connection (
see Fig.2
)
: the maximum distance to install each detector from the power supply show in the
Table 1
.
If more than one detector is to be powered in parallel, it is necessary to consider the voltage drop across
the supply cable. Normally use a two wire cable (
not shielded
) for power the conductors for output relay.
If
the output signal is used in mA, please use 3 conductors screened conductors for relay output. The max
load resistor is 50 ohm with 12Vdc power supply, while is 400 ohm with 24Vdc power supply (
see fig.4
).
Power Supply terminals, on the main board, are plug-in type, it is necessary to extract them to make the connec-
tion. Pay attention when you insert them again, being polarized. The relays terminals, on outputs board, are fixed.
The sealed relays are
tension free
SPST (
S
ingle
P
ole
S
ingle
T
hrow)
contacts and should be set NO (Normally Open) or
NC (Normally Closed) by positioning the 4th Dip-Switch (
see Table 3
). With the
Dip-Switches from 1 to 3 the concen-
tration for alarm activations is determined.
Note:
Dip-Switch should be set with instrument powered off. Dip-Switch settled in reserved position activate Fault
indications (see
“Operational Description > Faults”)
.
Important:
Once installation is completed,
only if it is necessary, adjust the sensor to the environment conditions,
switch on the unit, wait about 15÷20 minutes and carry out the
”Calibration in Air”
(see ‘
Test and Calibration >).
WARNING
Average life
: The sensitive element used in this detector has an excellent stability in time. In fresh air and in nor-
mal working condition the
sensor's life is
about 2 years
. After this period the yellow LED “
FAULT
” flashes every 4
seconds, is necessary replacing the “
Cartridge Sensor
”.
Periodical testing
: we advise to carry out working tests every 6 or 12 months. as explained on page 4 chapter
“
Tests and Calibration
”.
Note:
the detector is not able to detect Oxygen gas outside the room where it is installed, neither inside walls nor
under the floor.