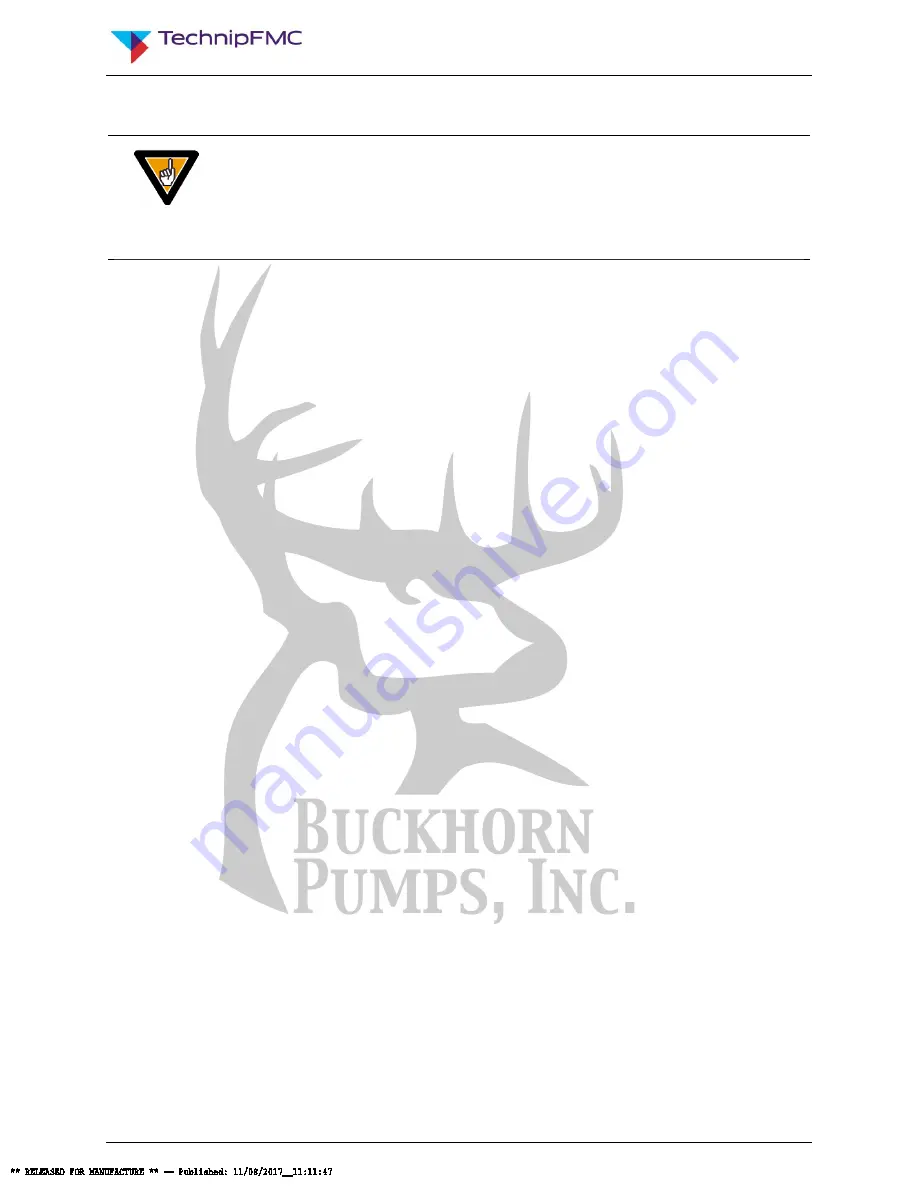
Doc No: OMM50001243
Rev: C Page 11 of 68
This document and all the information contained herein are the confidential and exclusive property of TechnipFMC,
and may not be reproduced, disclosed, or made public in any manner prior to express written authorization by TechnipFMC.
CAUTION
Never operate the pump without a belt guard securely installed.
For direct-coupled or spline-driven units, ensure that the shafts are centered and
parallel when the driver is mounted to the pump. Follow the coupling manufacturer
instructions for installation procedures and tolerances.
4.3
Suction Piping Recommendations
Poor suction piping practices are a very common source of pump problems. To ensure
proper operation, it is very important to follow good design practice in the installation of
the suction system before the pump is operated. A small amount of additional planning
and investment in the piping system usually provides for better pump performance and
longer periods between service requirements. It is difficult to diagnose many pump
problems without the aid of a suction pressure gauge. For this reason, FMC
recommends that a gauge always be installed in the suction line directly before it enters
the pump.
The suction line from the fluid source to the pump should be as short and direct as
possible. Use rigid piping, non-collapsible hose or a combination of both as
circumstances require in your installation. The suction pipe size should be at least
equal to or one size larger than the pump inlet. Long piping runs, low suction heads, or
indirect pipe routing may require even greater over-sizing of the suction line for proper
operation of the pump. A suction pulsation dampener is recommended to reduce the
effects of acceleration head to help when suction conditions are not optimal. In some
cases it may be necessary to install a booster pump in the suction line of the pump to
obtain sufficient pressure for the pump to operate successfully.
The suction line must be configured so there are no high spots in the line where air
pockets can collect. These pockets may make the pump difficult to prime and cause
rough, erratic operation. A drain valve or plug should be installed at the low point of the
suction line to allow for draining before freezing conditions or for maintenance.
FMC recommends that all piping be supported independently of the pump. By
supporting the piping this way, vibrations are reduced and stress on the pump is kept to
a minimum. The use of elbows, nipples, unions, or other fittings should be minimized.
Make sure that all joints and connections are airtight. Air leaks reduce the capacity of
the pump and can result in cavitation, rough operation, and/or loss of prime. To help
isolate mechanical and hydraulic vibrations, FMC recommends the use of flexible pipe
couplings or hose connections between the pump and any rigid piping.