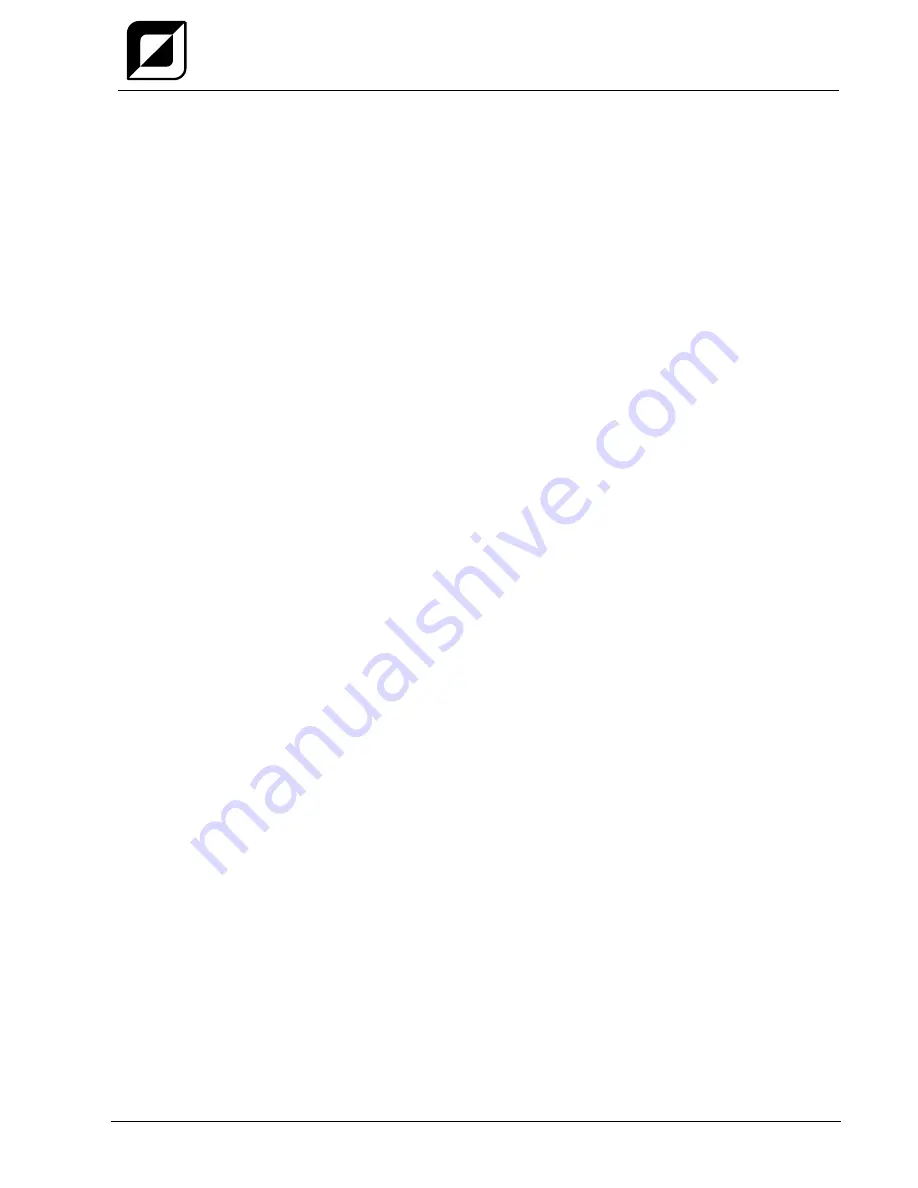
Contents
Notes on the use of these operating instructions
299-031000-TWD01
18.10.2016
5
10
Replaceable parts ................................................................................................................................ 73
10.1
Wire feed rollers ........................................................................................................................... 73
10.1.1
Wire feed rollers for steel wire ...................................................................................... 73
10.1.2
Wire feed rollers for aluminium wire ............................................................................. 73
10.1.3
Wire feed rollers for cored wire .................................................................................... 73
10.1.4
Conversion kit ............................................................................................................... 74
11
Appendix A ........................................................................................................................................... 75
11.1
JOB-List ....................................................................................................................................... 75
12
Appendix B ........................................................................................................................................... 76
12.1
Parameter overview
– setting information ................................................................................... 76