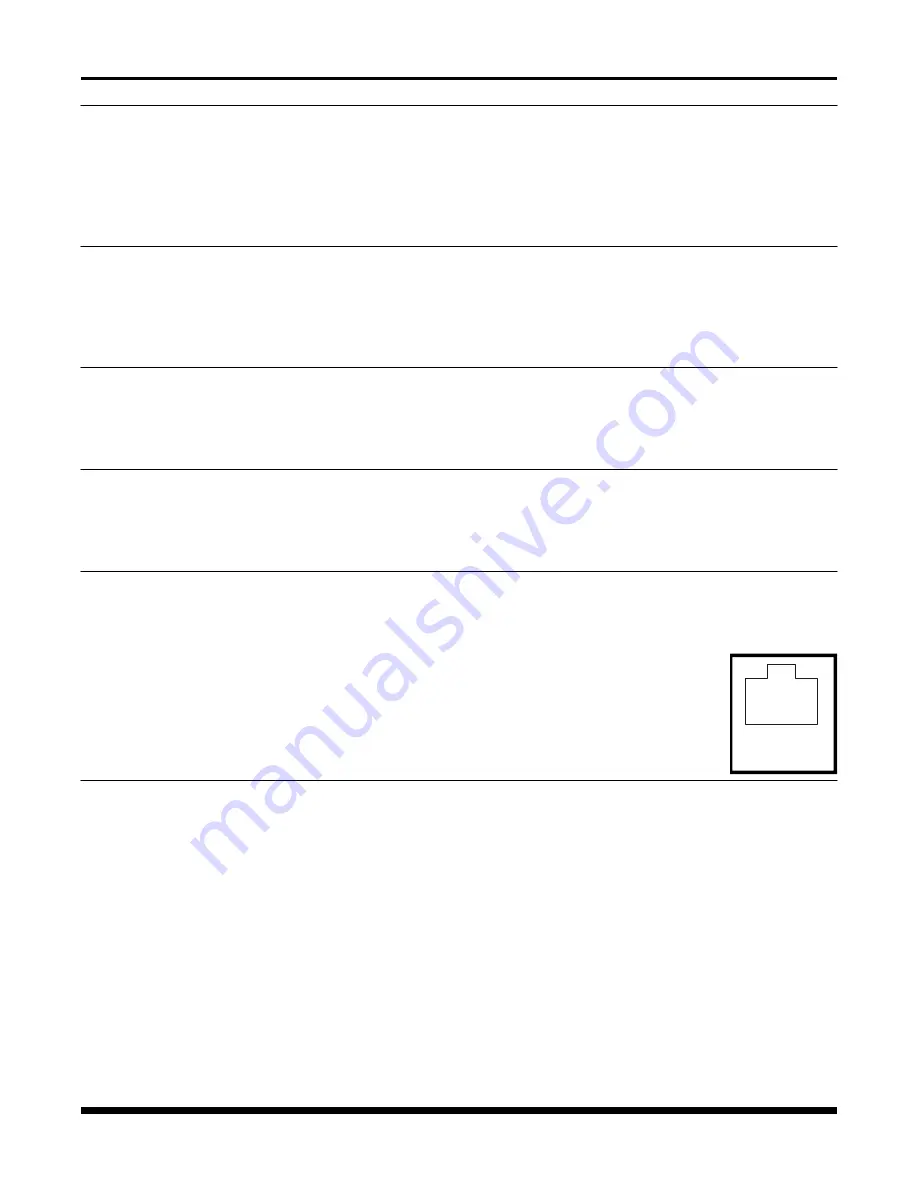
- 13 -
TC8116
User's Manual
Rev. 5.6D
Chapter 2 - Installation
Unpacking the Unit
Before unpacking any equipment, inspect all shipping containers for evidence of external damage caused
during transportation. The equipment should also be inspected for damage after it is removed from the
container(s). Claims concerning shipping damage should be made directly to the pertinent shipping agencies.
Any discrepancies should be reported immediately to the Customer Service Department at TC Communi-
cations, Inc.
Equipment Location
The TC8116 should be located in an area that provides adequate light, work space and ventilation. Avoid
locating it next to any equipment that may produce electrical interference or strong magnetic fields, such as
elevator shafts or heavy duty power supplies. As with any electronic equipment, keep the unit from excessive
moisture, heat, vibration and freezing temperatures.
Dry Contact Alarm Relay
A round jack connector at the rear panel of the A board provides for the Dry Contact Relay Alarm. Normally
in the OPEN position, any fiber problem will trigger an alarm condition that will force the switch to a CLOSE
position & the alarm buzzer will sound. The alarm buzzer can be disabled with front panel "disalm" dip switch.
System Configuration
The TC8116 has been pre-tested and switches have been set per factory specifications. The channels can
be field configured (in groups of four) for RS-232, RS-422, RS-485, TTL, Dry Contact Relay, Analog or
Intercom interfaces.
Power Supply
Each TC8116 card is powered by an external DC power adapter rated 9 to 12 VDC @400mA. There are
two terminal block connectors labeled "PWR A" and "PWR B" only one is required to power up the unit. If
your system has ten TC8116 cards, the power supply requirement is 10 x 400mA = 4.0A. Either a power
adapter or TC Communications' power card can be utilized to supply power to the units.
The power can be plugged into any of the power jacks at the back panel. Since each TC8116
card is equipped with a power redundancy capability, the power LEDs on the front panel will
light according to which power jack (A or B) is connected. Both LEDs will light when power
redundancy is utilized.
System Start Up
Apply the power by plugging the power plug into a power jack. The power source can be from a power
adapter or from a power card (installed either on the left side or right side of the rack). After power is applied
(and all DIP switches are set properly), all LEDs (except PWR & Vcc LEDs) will flash momentarily and
the following LED status should be observed from the front panel:
1.
The Power "A" and/or "B" LED should be lit. The "Vcc" LED should also be lit. If the unit is equipped
with dual optional optics (A & B boards), the "RxB" LED should be flashing on the A board.
2.
The "ALM" LED should be lit to indicate a "lost optic" condition. It will reset when the unit receives a
valid optic signal at "RxA" and "RxB" on optional dual optic models.
3.
At the rear panel, apply the electrical signals by plugging in the RJ-11 connector plugs one at a time.
Verify the corresponding "IN" LEDs for each particular channel as the connections are made. Each "IN"
LED should light to indicate a valid electrical signal connection. If the "IN" LED does not light on a
particular channel, it usually indicates incorrect connections at the RJ-11 input port (double-check your
connections and verify them with the connection diagrams in the Electrical Signal Interface section). If
all the "IN" LEDs are lit prior to the RJ-11 connections being made, flip SW5 to the On position.
9-12 VDC@400mA
+ -