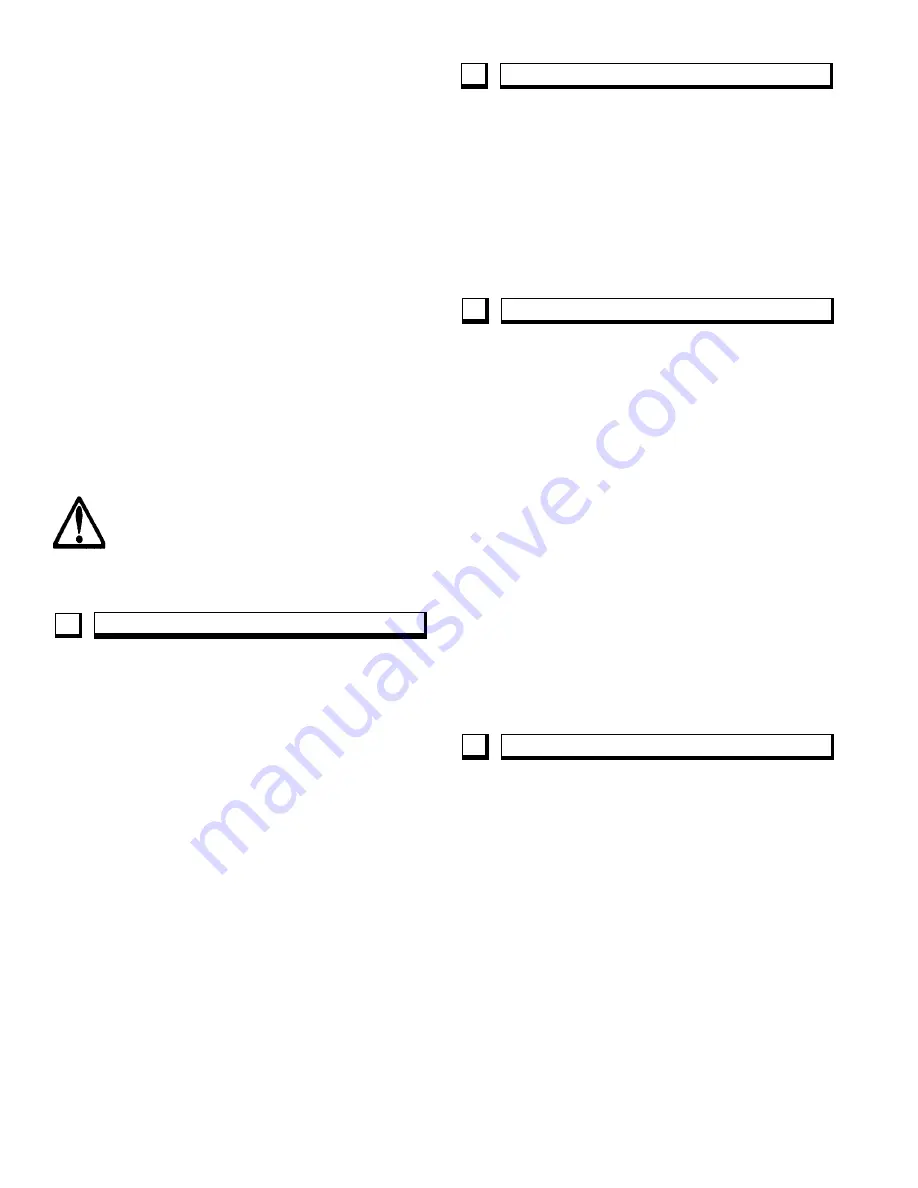
30
14
IMPORTANT ADVICE
(See Fig. 2)
•
Tighten loose nuts and bolts regularly, particularly
after several hours of operation.
•
Check V-Belt tension regularly. Re-tighten
V-Belts as necessary. Replace V-Belts
in complete
sets only.
•
Remove the Diamond Blade (2E) for storage. Store it
carefully.
•
Check the water spray over the Diamond Blade (2E)
periodically.
•
Tighten the Diamond Blade (2E) firmly on the Blade
Arbor (2C).
•
Make sure the contact faces of Flanges (2B & 2F),
Diamond Blade (2E), and Blade Shaft (2I) are clean.
•
Use the Emergency Stop Switch (1T) ONLY in the case
of emergency. Do not use for normal engine stopping.
•
Put the saw in STOP (1V) before turning the key to the
OFF position.
If installed, this saw has a mechanical parking brake that
locks the rear axle by engaging a mechanical lock into a
gear on the rear axle.
•
To engage parking brake, pull up on the parking brake
knob (1N). The brake will lock when the locking lever
lines up with a slot in the gear.
•
To disengage the brake, push down on the parking
brake knob (1N) .
13
PARKING BRAKE (OPTIONAL)
The hydraulic system on this saw is used to RAISE /
LOWER the Diamond Blade (2E) and to propel the saw
FORWARD or REVERSE. The hydraulic system consists
of a Hydrostatic Transmission, a DC Lift Pump with a Flow
Control Valve, and a Hydraulic Lift Cylinder.
•
Check Hydrostatic Transmission fluid level periodically.
Maintain oil level with SAE 10W30 API CLASS
SE,CC,CD motor oil.
DO NOT OVERFILL
! Check oil
level when saw is level.
•
Change Hydrostatic Transmission fluid every 500 hours
of operation. Fill Hydraulic Reservoir with SAE 10W30
API Class SE,CC,CD motor oil.
DO NOT OVERFILL
!
Check oil level when saw is level.
•
Check the DC Lift Pump fluid level periodically.
Maintain oil level with Dextron III transmission fluid.
DO
NOT OVERFILL
!
•
The lowering rate of the saw can be adjusted using the
Flow Control Valve at the rear of the saw. If the saw
falls too quickly, turn the knob on the Flow Control Valve
CLOCKWISE until an adequate lowering rate is set.
12
HYDRAULIC SYSTEM
TO TENSION V-BELTS -
PRO 35 III DIESEL AND ELECTRIC:
ALWAYS use Goodyear TensionRite
™
Gauges, Fig. 5 to
ensure achieving the proper tension. Refer to the instruc-
tions on the back of the TensionRite gauge for proper use.
This saw is equipped with high tension banded V-belts.
The belts are properly tensioned at the factory but after a
few hours of operation they will stretch and become loose.
Model
Used Belts
New Belts
Pro 35 III Diesel 26”/30” # 1.75
# 2.25
Pro 35 III Diesel 18”
# 2.25
# 3.0
Pro 35 III Electric
# 2.25
# 3.0
•
Turn Engine Start Switch (1L) to the
“0” (OFF)
position.
•
Using the wrench, loosen the horizontal clamping bolts
at the front of the machine.
•
Turn the Tensioning Bolt [at the front of machine]
CLOCKWISE until the V-Belts are tight.
•
Replace
V-Belts
in complete sets only.
Never tension V-Belts beyond the original
factory tension. Loose V-Belts result in poor
saw performance and short belt life.
The Pro 35III is available in several 20HP electric
versions. It is available in 4 different voltages with three
(3) different motors. It comes completely wired with
appropriate plugs, connectors, wiring, motor starter,
overload heaters and an in dash current load meter. The
electric saw is operated exactly like a gas saw after it is
connected to the power source. The key must be turned
to the Start position and will engage the motor starter.
Turn the key off, the motor will stop. The emergency stop
switch and water safety switch will also stop the motor.
Operate the electric saw at a speed where the current
load meter does not exceed 100% of full load current.
Exceeding 100% of the full load amperage will result in
the current overload heaters to overheat and shut off the
electric motor. After allowing the overload to cool off,
(approx. 5 minutes), press the RESET button on the front
of the electrical enclosure box. Turn the key to the start
position to engage the motor starter.
15
PRO 35III ELECTRIC SAWS
Содержание PRO 35 III DIESEL
Страница 3: ...3...
Страница 17: ...17...
Страница 33: ...33...
Страница 36: ...36 Diagram 1 Wiring Diagram PRO 35 III Diesel 182127...
Страница 38: ...38 Diagram 2 Wiring Diagram PRO 65 III Diesel 182139...
Страница 40: ...40 Diagram 3 Ladder Diagram PRO 35 III Diesel and PRO 65 III Diesel 182121...
Страница 42: ...42 Diagram 4 Wiring Diagram PRO 35 III Electric 182062...
Страница 45: ...45 Diagram 6 Ladder Diagram PRO 35 III Electric 182068...