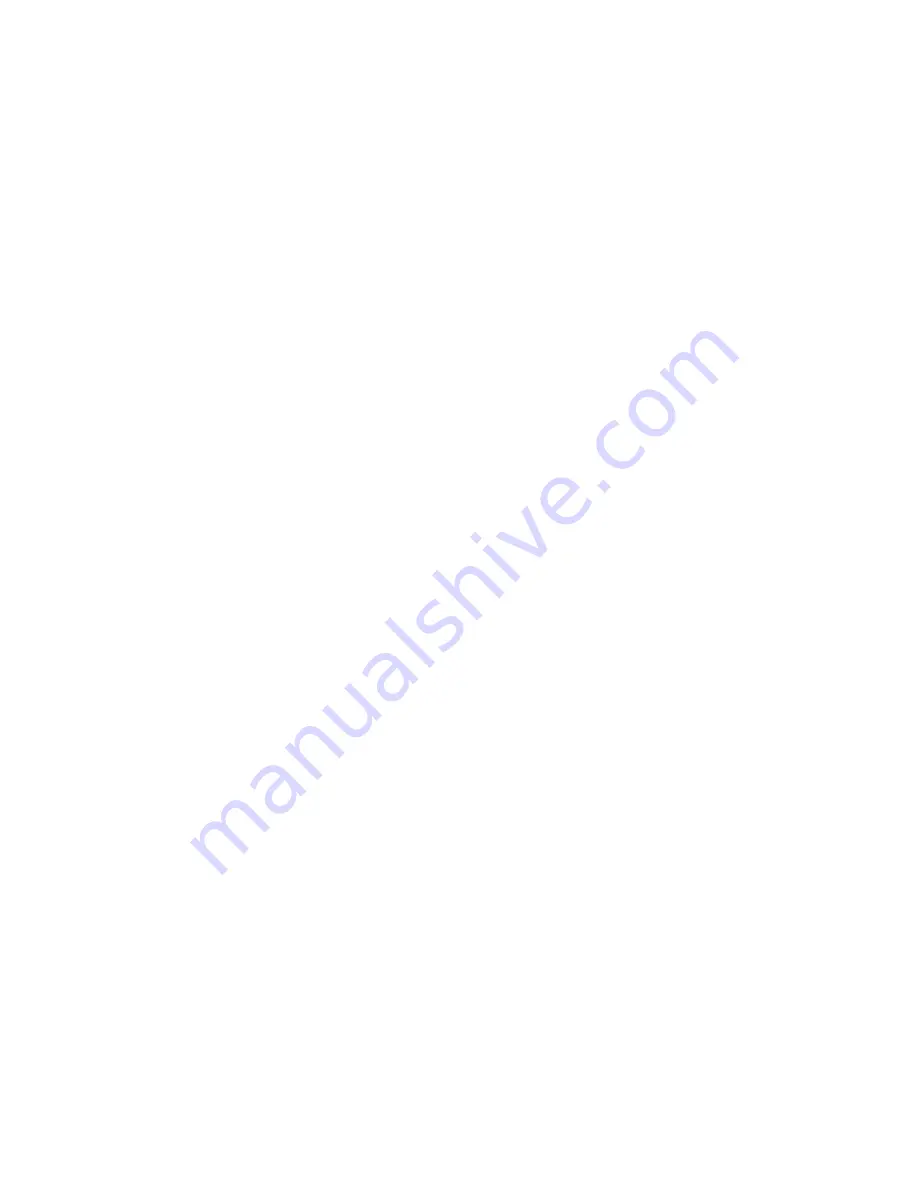
7
lock will be improperly formed – and you may also lose the hem-return. The same condition may exist if the
entrance gauge is not set correctly.
STRAIGHTNESS:
Raising or lowering the adjustable gauge bar on the exit end of the machine can eliminate upward or
downward bow. (See Sketch # 3.) Lowering the exit bar and putting pressure slightly on the formed lock can
compensate upward bow. A downward bow shows too much pressure against material – raise bar slightly.
Should the auxiliary button flange shape bow downward, a thin shim can be placed onto the tabletop to
apply slight pressure to the underside of the material thereby straightening the formed section.
Note: the # 1 roll station punch position can be shimmed out away from the machine plates to locate the
punch closer to the bend line thereby achieving a tighter fit on the snap. See Warning note for proper roll
positioning.
WARNING:
The gauge setting should not be made while #1 station is shimmed away from its normal location. The Top
# 1 roll is fastened to the shaft by a bolt and washer. The bottom roll is held to the shaft by a key placed into
the rolls and is not restrained but held in place by a shoulder on Top #1 roll and should be allowed to float.
The shim, if required, should be placed behind the top roll only.
LUBRICATION:
There are seven Ale mite fittings located on the underside of the stand. These fittings are for the high-speed
reduction bearings, which should be lubricated after every four hours of operation. Lubricate gears
periodically as required. Recommended lubricant: Lubricant standard viscous # 3 ( a product of the Standard
Oil Co. ) or equivalent.