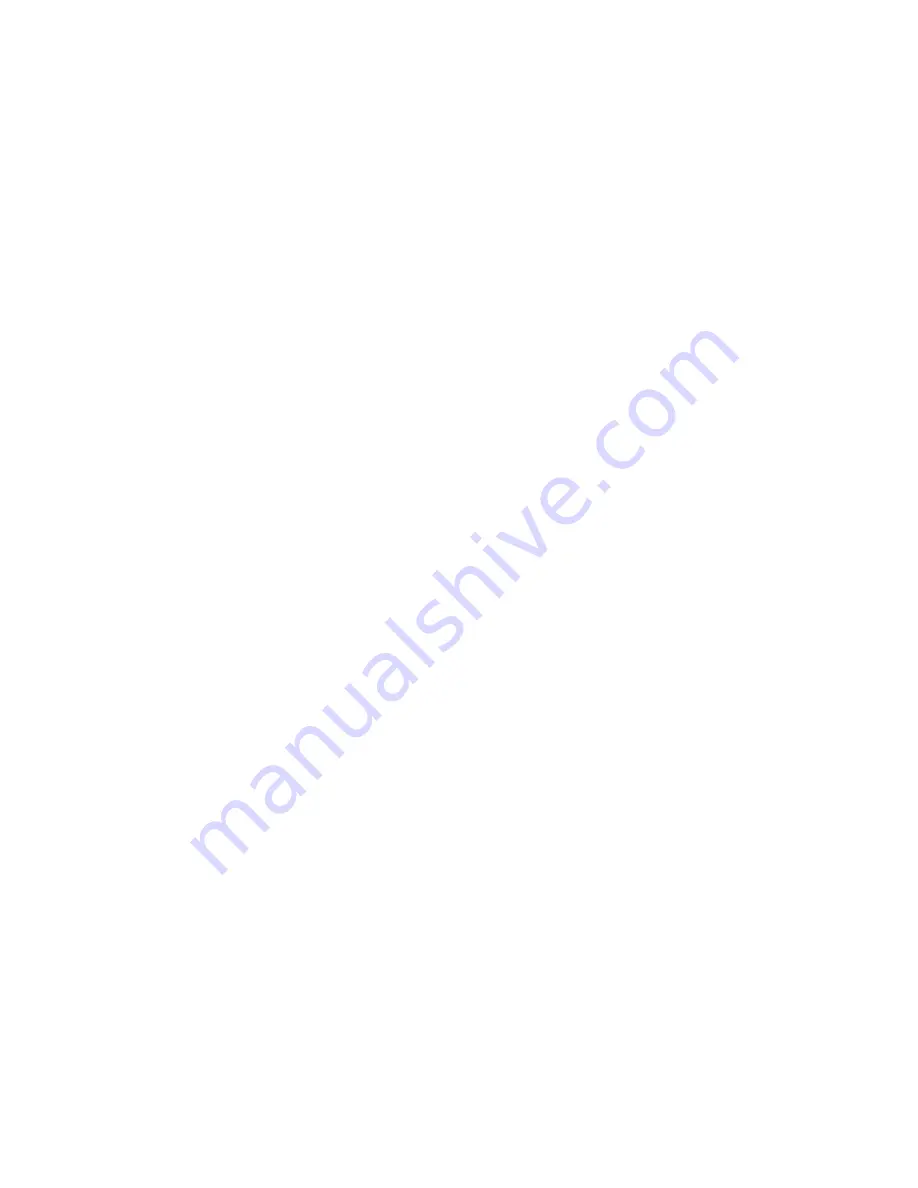
6
If the material shows signs of stretch or excessive pressure loosen studs slightly. The material should
emerge from the machine with a properly formed angle to obtain 90 deg. duct corners when locks are
snapped together. The angle can be controlled by the location of the top number eight forming roll on the
shaft and the positioning in or out of the idler bracket located at the seventh and eighth roll station. To adjust
the above proceed as follows:
1.
Remove the two idler bracket-retaining cap screws. Note shims are placed between the bracket and
the plate. Shims may range from .020 to .030 to insure proper flange.
2.
Remove top and bottom #8 roll station.
3.
To increase angle of formed flange add from .010 to .040 shims 22 mm I.D. on the roll shaft.
4.
Place the roll onto the shaft securely by tightening setscrew.
5.
Replace bottom #8 roll.
6.
Replace idler bracket assembly.
If angle is less than 90 deg. then too much pressure is applied by the top 8 roll or idler bracket rollers.
Adjust roller and bracket to obtain proper results.
GAUGE SETTINGS:
Both entrance gauges located at front of machine may be checked or reset by placing a straight edge along
the outer edge of the machine plate for the inboard rolls and along the outer edge of the rolls for the button
flange. (See Sketch # 1 .)
PRESENT GAUGE SETTINGS:
Inboard Rolls
3-5/64” measured from edge of gauge nearest the rolls.
3-1/8” measured from edge of gauge farthest from rolls. (As shown is Sketch # 1.)
AUXILIARY BUTTON FLANGE:
1” measured from edge of gauge nearest the rolls.
1-1/32” measured from edge of gauge farthest from rolls.
The above gauge settings can be modified slightly to suit specific requirements.
TROUBLE CHECKS:
Due to the unusual physical characteristics of certain types of material, it may become necessary to reset the
entrance gauge in its entirety. In the event that the material pulls away from the gauge or the lock is not
formed properly, the gauge-taper can be increased – or the entire gauge setting may be increased or
decreased slightly to achieve required results. Exit gauge bars are set to, but not against, the formed edge of
material when emerging from the machine.
In running certain types of material, it may be necessary to add a slight lubricant to the edge of the sheet
being formed to aid the flow of material into the finished lock. The above may be required if the 1/8” return
hem does not form properly – if this hem is irregular in nature or tends to wave at edge of formed section –
or entrance gauge adjustments do not correct or compensate for proper formation. This lubricant is any light
machine oil applied either manually or by a felt wiper pad mounted on the machine.
To obtain the best lock, it will be necessary to insure that the material is in contact with the entrance-starting
gauge throughout the complete length of the sheet being formed. Certain materials, as well as hold- down
adjustment may have a tendency to allow the material to drift away from the gauge. When this occurs the