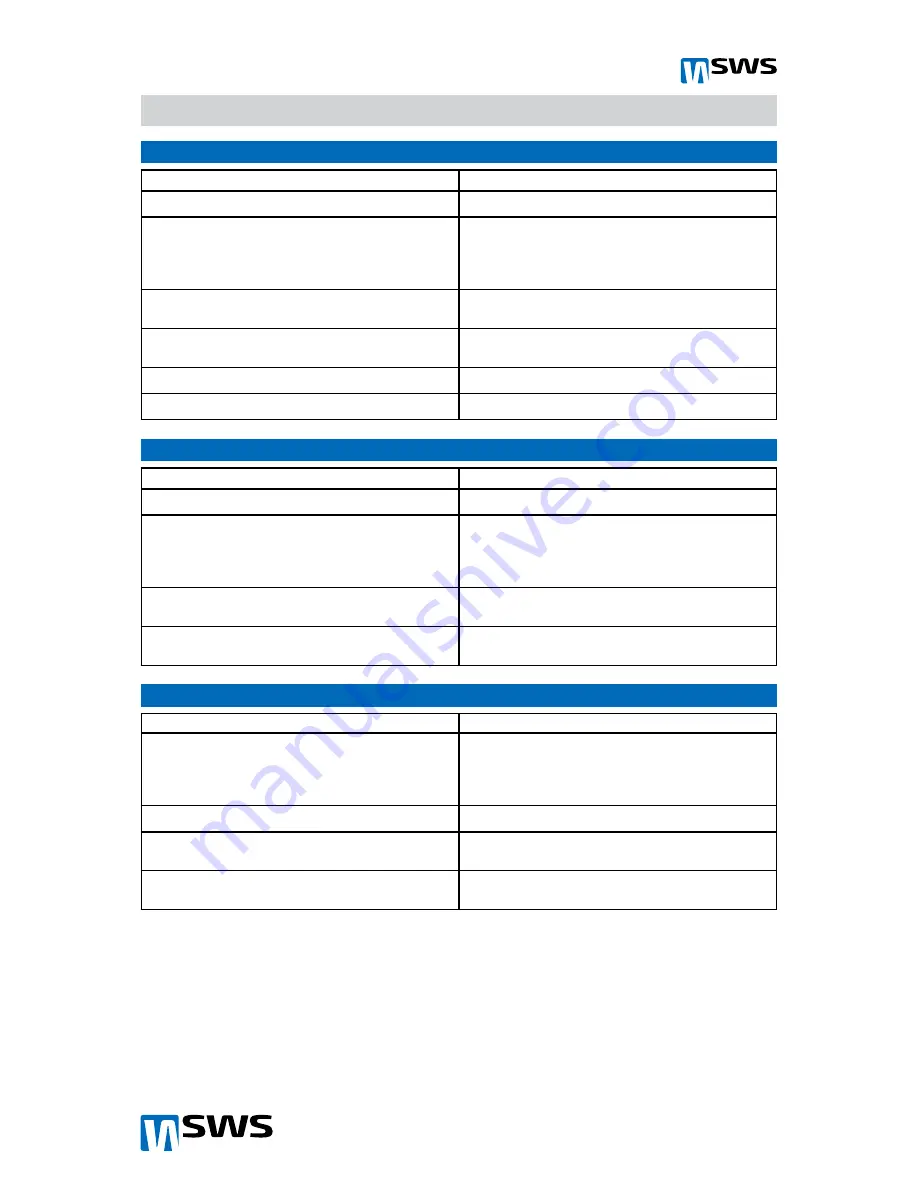
Manual Version 1.3 - June/2017
18
ALUMTIG 200
ALUMTIG 200
8.4 Porosity and or poor weld appearance and color
8.5 Unstable arc during DC welding
8.6 Unstable arc during AC welding
POSSIBLE REASON
SUGGESTED SOLUTION
Incorrect Gas
Check that 100% Argon is being used.
Inadequate gas flow / gas leaks
Check the gas is connected, check hoses, gas
valve and torch are not restricted. Set the gas flow
between 7–14 LMN (15–25 CFH) flow rate. Check
hoses and fittings for holes, leaks, etc.
Moisture on the base metal
Remove all moisture from base metal before
welding.
Contaminated base metal
Remove materials like paint, grease, oil, and dirt,
including mill scale from base metal.
Contaminated filler wire
Remove all grease, oil, or moisture from filler metal.
Incorrect filler wire
Check the filler wire and change if necessary.
POSSIBLE REASON
SUGGESTED SOLUTION
Torch connected to DC +
Connect the torch to the DC – output terminal.
Contaminated base metal
Check the gas is connected, check hoses, gas
valve and torch are not restricted. Set the gas flow
between 15–25 CFH (7–12 LMN) flow rate. Check
hoses and fittings for holes, leaks, etc.
Tungsten is contaminated
Remove 3/8” (10mm) of contaminated tungsten and
re‑grind the tungsten.
Arc length too long
Lower torch so that the tungsten is off of the work
piece 1/8”–1/4” (3.2– 6.35mm).
POSSIBLE REASON
SUGGESTED SOLUTION
Incorrect gas or inadequate gas flow
Check that pure Argon is being used. Check the gas
is connected, check hoses, gas valve and torch are
not restricted. Set the gas flow between 15–25 CFH
(7–12 LMN) flow rate flow rate.
Incorrect tungsten being used
Check and change the tungsten type if necessary.
Tungsten is contaminated
Remove 3/8” (10mm) of contaminated tungsten and
re‑grind the tungsten.
Excessive rectification in the base metal
Adjust balance control. Increase travel speed. Add
filler wire during welding.
7.2 GTAW (TIG)