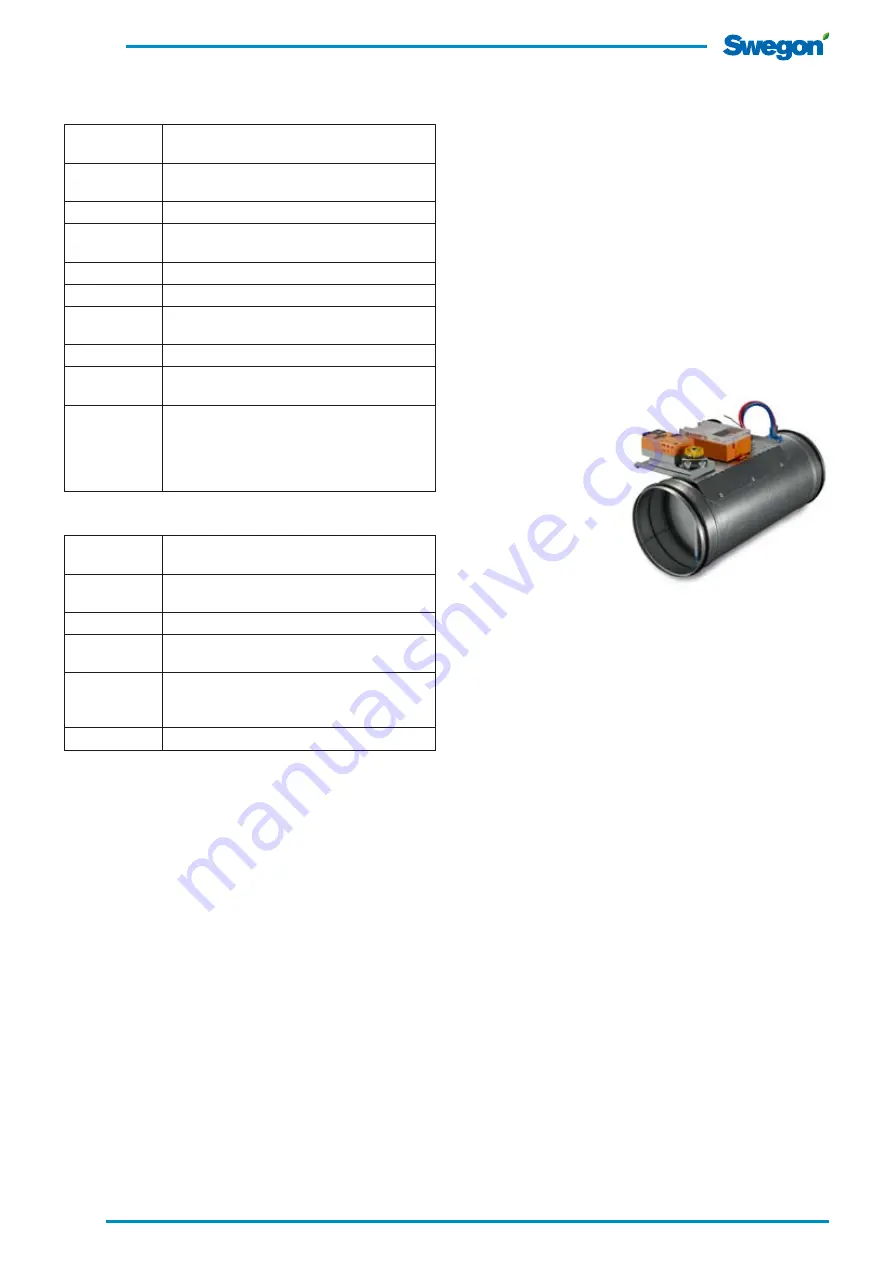
10
VAR
Swegon reserves the right to alter specifications.
20111011
www.swegon.com
VAR 2
Checking the performance
Start
A 3-minute warm-up period is required when you switch
on the voltage (cold start) before the controller will oper-
ate normally.
Checking the min. airflow
This can be done by disconnecting the control signal cable
from terminal 3. The damper will then move to the closed
position. This position is conditional on the bearing pres-
sure and the preset min. airflow rate. Measure the voltage
U and calculate the airflow using Formula 2 on page 7.
Checking the max. airflow
Use the room thermostat or some other microprocessor
substation equipment to override the system so that the
control voltage will be a 10 V input on terminal 3. As an
alternative you can short circuit between terminals 2 and
7. This will steer the controller to the preset max. airflow
setting. The damper will move to the open position.
Measure the pressure in the pressure tapping and calcu-
late the airflow using the K-factor for the relevant size.
Measure the voltage U and calculate the airflow using
Formula 2 on page 7.
The VAR 2 as a constant-flow controller
The VAR 2 can be used as a constant-flow controller in
two ways. It is most appropriate to use the min. flow
setting as the set point for the constant airflow. 24 V AC
only should be connected to cable pair 1 and 2. You can
also use the max. airflow setting, however you must then
provide for a short circuit between cables 2 and 7. See
under: Checking the max. airflow.
Trouble shooting
Incorrect polarity on control signal zero conductor
It is important that the neutral conductor follows the
entire chain of connections from thermostat to control-
ler. Check this by measuring the control voltage between
cables 1 and 3 on the VAR. Correctly wired it should be
possible to vary the signal between 0-10 V DC. If incor-
rectly wired the signal will be ~ 8 - 14 V DC. The follow-
ing values apply to the RTC: ~ 5-10 V DC.
Start menu of the VAV controller
Start:
Connect the cable provided to the VAV
controller
Reply:
The type of controller connected appears in
the display window
"OK" button
The serial number of the controller is shown
"+" button
The program version of the controller is
shown
Select fun-
ction:
▼▲
Navigate forward/backward to scroll
between the various menu positions (see
table below)
Exit:
Disconnect the cable to the VAV controller
PC-TOOL
A PC-based program can be used for checking performance
and changing settings. PC-Tool version 3.0 or later is required.
This is simpler since contact with the controller takes place
with a separate bus cable, no reconnection is required (Plug
And Play). Contact Swegon’s representative for further info.
Configuration menu of the ZTH-GEN
Start:
Hold the (OK) button depressed and at the
same time connect to the VAV controller.
Answer:
"Configuration menu"appears in the display
window
Select setting
Press the
▼
button (see selection below)
Choice of
language
German
*
/English
Choice of unit
m
3
/h
*, l/s, cfm
Voltage
DC/AC 24 V (shows current supply voltage)
MP test
Shows the pulse train in the network (for
system integrator)
Expert mode
0 */ 1 (provides expanded access to settings)
Advanced
mode
0 */ 1 (provides expanded access to settings)
Exit
Via menu selection (returns automatically to
the mode for configuring the VAV controller)
or for removing the connection to the VAV
controller. The selected settings are automa-
tically stored in the ZTH.
Airflow does not correspond
This is almost always due to that the requirements for
lengths of straight ducting upstream/downstream of the
VAR have not been met. If the ducting deviates from these
requirements, the error can be as much as 20%. The flow
measurement sensor may become fouled in systems with
considerable dusty air (most often extract air systems).
This however doesn’t occur until the system has been
operating for 3-5 years. The sensor can be cleaned by
blowing it with clean air in the opposite direction, i.e. in
the minus tube connection. We recommend compressed
air in a low-pressure aerosol tube. The duct must also be
cleaned so that the flow measurement stick and the pres-
sure tappings are not clogged.