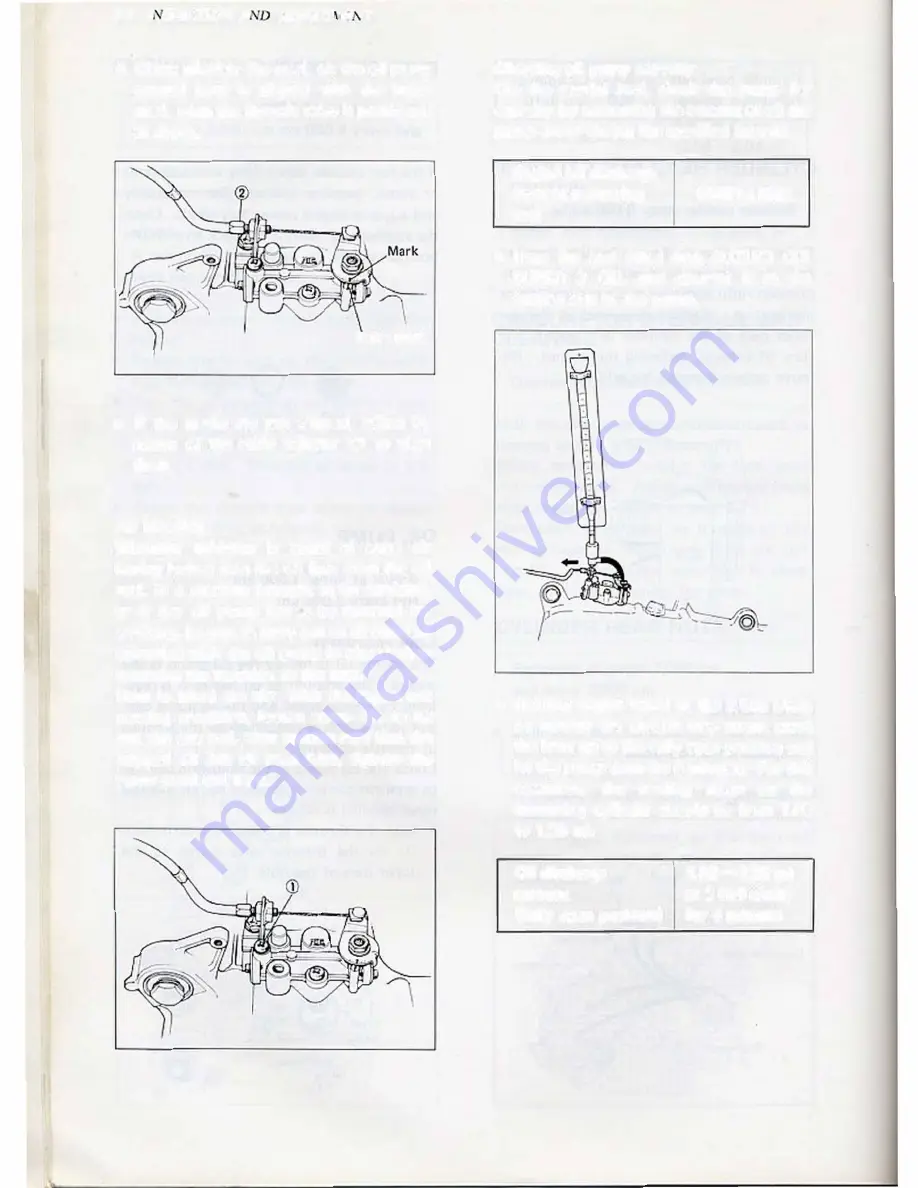
2-8
I
SPECTJON
A
/lD]UST
tr: 11'
•
Check whether the mark on the o i l pump
control lever is al igned with the index
mark when th
e
throttle valve is positioned
as abo
v
e
.
Index mark
•
If the marks are n ot aligned, adjust by
means of the cable adjuster
®
to a l ign
them.
Air bleeding
Whenever evidence is noted of some air
having leaked i n to the oil l i ne from the oil
tan k in a machine brought in for servicing,
or if the oil pump has to be removed for
servicing, be sure to carry out an a i r bleeding
operation with the o i l pump in place before
retu rning the machine to the user.
H ow to bleed the air: With the engine not
running condition , loosen screw
CD
,
to let
out the a ir; and, after making sure that the
trapped air has al l been bled, tighten the
screw good and hard.
Checking oil pump capacity
Use the special tool, check the pump for
capacity by measuring the amount of oil the
pump draws during the specified i n terval .
Engine
oi l
discharge
amount measuring
tool
09900-21602
•
Have the tool f i l led with SUZUK I CCI
SUPE R 2
0
I L and connect it to the
suction side of the pump.
•
Holding engine speed at the 2 000 r/min
by turn ing the th rottle stop screw, move
the lever u p to the fu l ly open position and
let the pump draw for 6 min utes. For this
operation, the reading taken on the
measuring cyl inder should be from 1 .02
to 1.26 ml.
Oil
discharge
1
.
02
-
1
.
26
m l
amount
at
2 000
r/min
(fu lly
open position)
for
6
minutes
Содержание FZ50 1979
Страница 1: ......
Страница 65: ...4 8 SER VICI re Ii FORMll no WIRE AND CABLE ROUTI NG WIRING ROUTING ...
Страница 74: ...SUZUKI MOTOR 1CO LTD ...