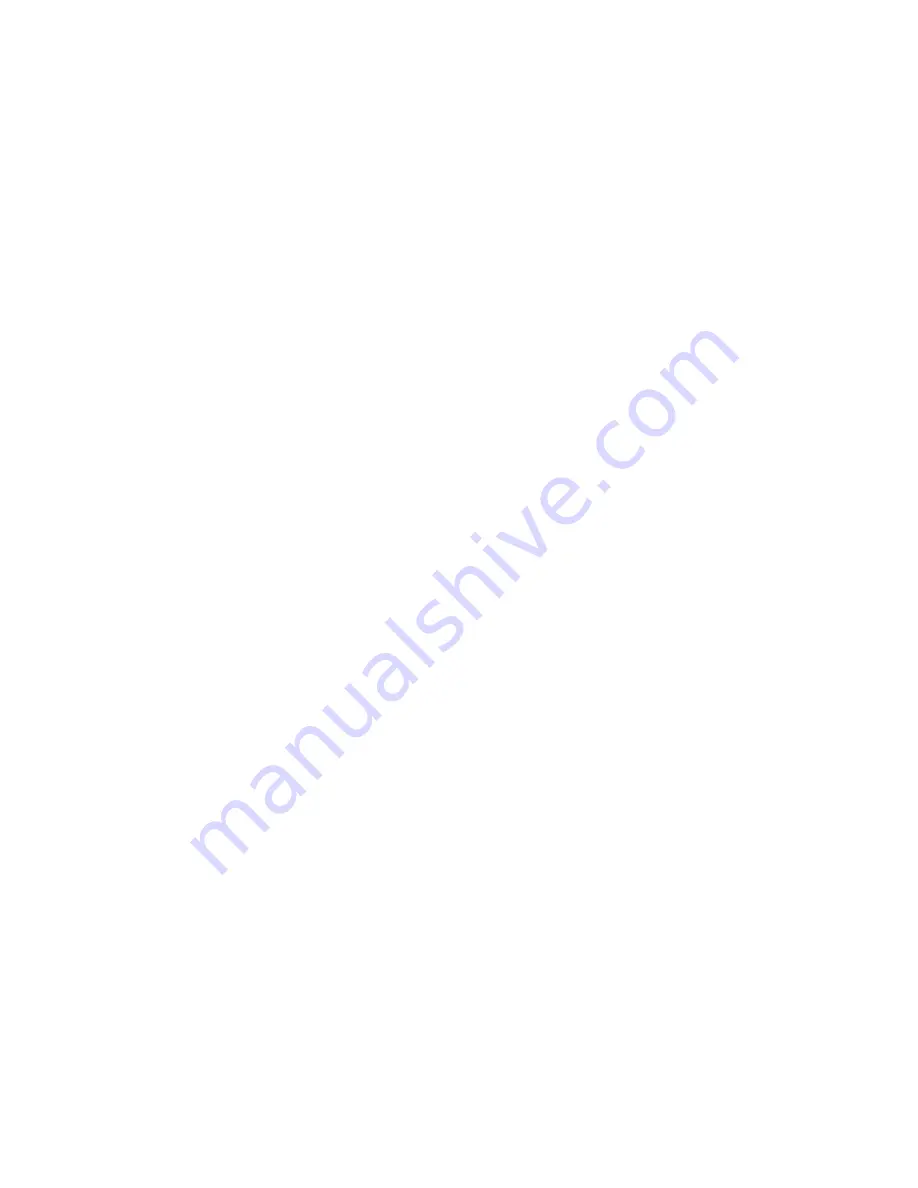
13
Trouble Shooting
Common Examples and Causes of Poor Laminating.
A. The film is not bonding to the subject or to itself at the sealed edges
Causes:
1. The heat (on either or both of the rollers) is set too low.
2. The film tension is too tight.
3. The bottom roll of film is threaded incorrectly.
4. The pressure setting is not correct.
B. There are wrinkles or irregular waves running across the laminated web
(Perpendicular to the edge)
Causes:
1. The heat set is too high.
2. There is not enough tension on the supply mandrels. (Large, irregular waves).
3. There is too much tension on the supply mandrels. (Small, fine wrinkles - “orange peel” effect).
4. The rubber laminating rollers are not clean.
5. The pressure adjustment for the laminating and pull rollers is out of adjustment.
C. There are stretch lines running with the web (Parallel to the edge)
Causes:
1. There is too much tension on the supply mandrels.
2. The heat (on either or both of the rollers) is set too high.
3. The heated rollers are not clean.
D. There are blisters on the surface or along the edge of the subject
Causes:
1. The heat is set too high on either or both heated rollers.
2. There is excessive moisture in the paper that is being laminated. (If inks are not dry, this may also
cause blisters). For high moisture content substrates, use low temperature films with a bonding
temperature of 185º-190ºF.
3. The rubber laminating rollers are not clean, or are damaged.
E. The finished lamination is curling
Causes:
1. There is unbalanced tension on the supply rolls. (Too much tension on the top supply roll will
cause the web to curl up. Too much tension on the bottom roll will cause a downward curl in the
web).
2. The bottom roll of film has been threaded incorrectly.
3. The heat is unbalanced in the top or bottom heated rollers. (If the subject curls up, there is too
much heat on the top roller. If it curls down, there is too much heat on the bottom roller).
F. There is wrinkling around the edge of the laminated item
Causes:
1. The item that needs to be laminated is too thick or there is not enough adhesive on the type of film
that is being used.
Possible Solutions:
a. Loosen tension
b. Use thicker film (Higher adhesive content)
c. Flush cut item
Laminator.com
www.laminator.com