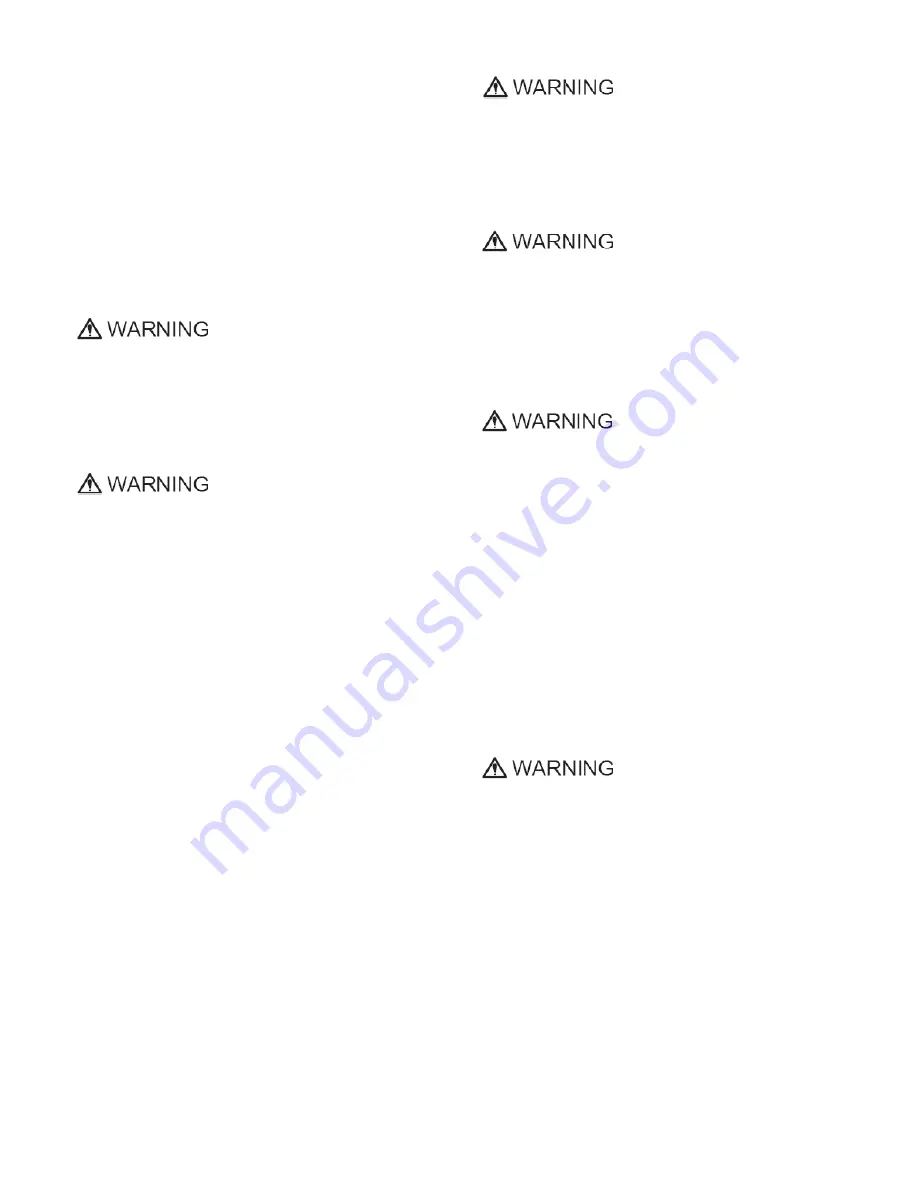
Superabrasive
User Manual Original Language
Lavina® 20GE
7/2020
11
Local law enforcement agencies such as the local Fire Marshall
also rely on independent testing labs such as UL and CGA
before giving their approval of the use of some equipment.
These labs thoroughly test equipment and submit their stamp
of approval only after rigorous testing. While not being
required by all law enforcement agencies, the stamp of
approval by these agencies further assures the operator that
he or she is working with and around safe equipment.
NOTE
: In order to reduce all consequences of the above‐
mentioned risks, we advise that machine operators will follow
the instructions in the manual at all times.
2.12 RESIDUAL RISKS
During the normal operating and maintenance cycles,
the operator is exposed to few residual risks, which
cannot be eliminated due to the nature of the
operations.
2.13 BEFORE YOU BEGIN
Clear working area of any debris or objects.
A first‐time operator must always read the manual
and pay attention to all safety instructions.
All propane connections and cables must be
inspected for potential damages.
Perform general daily inspections of the machine
and inspect the machine before each use.
Always inspect the safety devices:
-
The tool protector must be working.
-
Mount the security disc when working with
Quickchange Pads.
-
The machine must be clean.
-
Never operate the machine in the rain!
-
Confirm that there are no missing parts especially
after transportation, repair or maintenance.
-
Before filling the water tank with water, make sure the
machine is not running and the main switch is turned
off.
-
Before turning on the machine, make sure that the
base is placed on the floor, the machine MUST NOT be
in a tilted position when starting.
2.14 OPERATING MACHINE
When operating the Lavina® 20GE, make certain
that there is no one, but you around the machine.
Never leave the machine unattended while
working.
The water hose must move freely and must be
damage‐free.
Make sure the working surface is not too uneven. If
it is, it may damage the machine.
2.15 AFTER WORK IS COMPLETED
Clean the machine and its surroundings properly.
Empty and clean the water tank.
Store the machine in a safe place.
Place the Propane bottle outside in designated storage.
2.16 THE WORK AREA
Prevent people or vehicles from entering the work area.
Clear all hoses and cables from the work area.
Always check the floor for debris.
2.17 PERSONAL PROTECTIVE EQUIPMENT (PPE)
Always wear safety shoes when working with the machine.
Always wear ear protectors when working with the machine.
All personnel in the immediate work area must wear safety
glasses with side shields.
Always wear safety gloves when changing the tools.
Always wear clothes suitable for the work environment.
Always wear Carbon Monoxide Indicator badges as an extra
precaution.
The plastic indicator contains a colored indicator button
that darkens in the presence of Carbon Monoxide. The
relative darkness of the indicator button indicates the level
of CO in the ambient atmosphere. Most indicator badges
have a useful life of 30 days, depending on the concentration
of contaminants, humidity, and temperature.
2.18 TESTING
There are a great number of instruments offered on the market
to test for toxic gases. Only those designed to read carbon
monoxide resulting from combustion engines are considered
acceptable for testing exhaust emissions from propane powered
floor machines.
Some instruments are used to read “ambient air” and may
be damaged if used to take readings in the muffler or tail pipe.
Selecting the proper instrument is an important part of meeting
the testing requirements.
Generally speaking, units capable of reading in ppm, (parts per
million), at ranges from 0 to 1000 are adequate for checking
ambient air (air in the breathing zone of the operator).
Instruments capable of testing carbon
monoxide in the exhaust should be able to read from 0 to
at least 2000 ppm and should be certified by the
manufacturer for that purpose.
Some instruments and systems used for these purposes are: