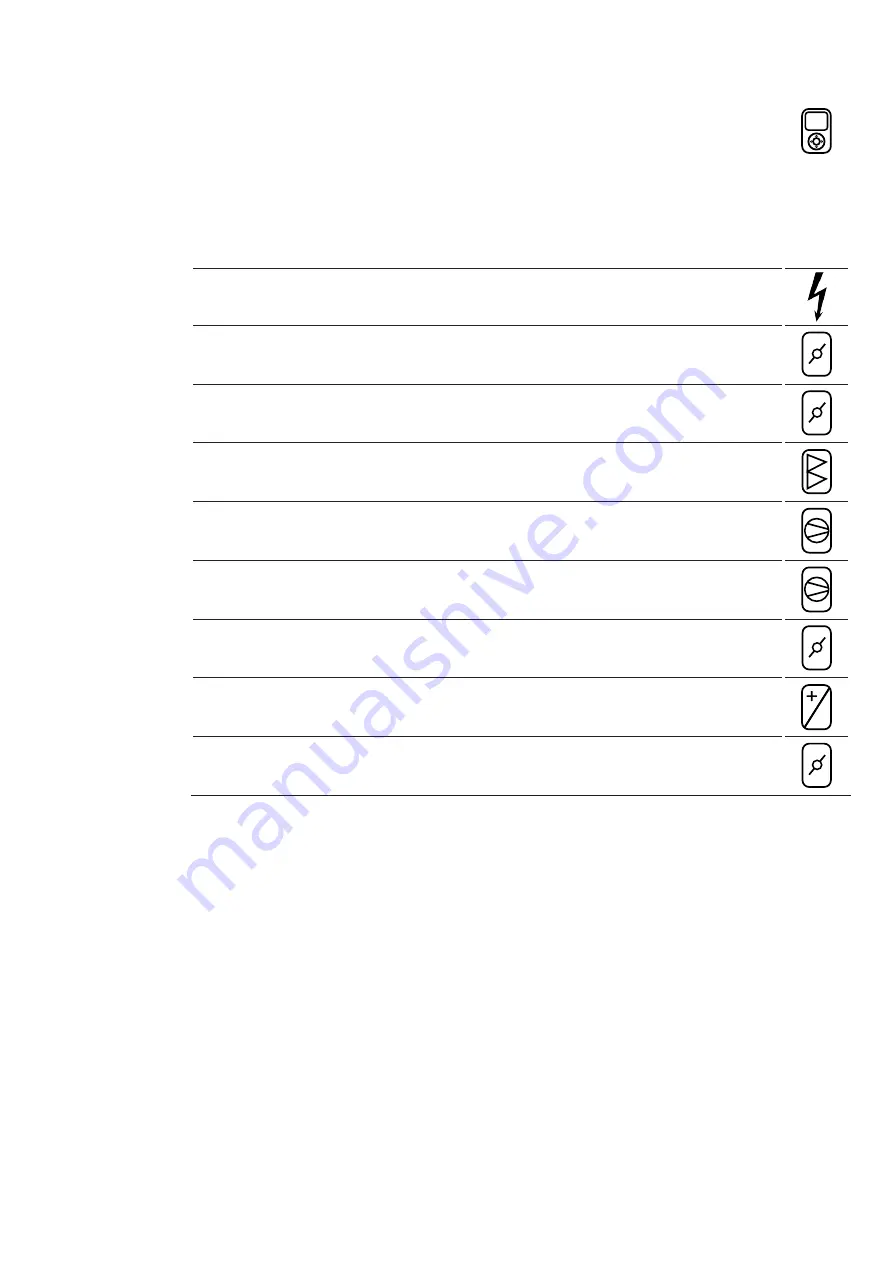
CYBERHANDLER 2 INSTALLATION, OPERATION AND MAINTENANCE MANUAL
EN/05.2019 © STULZ GmbH – all rights reserved
11
7 Cooling coil
The CH2 control consists of the C7000 controller and following sensors are mounted as standard:
- Temperature and humidity sensor (outdoor air)
- Temperature and humidity sensor (supply air)
- Temperature and humidity sensor (Return air)
- Pressure switch (Clogged filters alarm, IT room side)
For models equipped with a refrigerant circuit (DXT/DXR), additional sensors are used for refrigerant
circuit control.
For more information about the controller, see the C7000 user’s manual.
8 Electrical cabinet
The electric cabinet is housed inside the unit and is made according to the EN60204-1 IEC
standard.
9 Supply damper
Frame and blades are made of aluminium.
10 Return damper
Frame and blades are made of aluminium.
11 Filters, IT room side
Bag filters are used ensure a pressure loss as low as possible.
12 Supply fans
Supply fans are Electronically Commutated type and mounted in fan wall arrangement.
13 Exhaust fans
Exhaust fans are Electronically Commutated type and mounted in fan wall arrangement.
14 Recirculation damper
Frame and blades are made of aluminium.
15 Condenser coil
Only the model with DX top-up cooling is equipped with a condenser coil.
16 Exhaust damper
Frame and blades are made of aluminium.
Operation
In every unit there is a double plate heat exchanger with an adiabatic cooling system. The noz-
zles spray water directly on the lower plate heat exchanger to ensure the process reaches the
maximum efficiency.
This indirect adiabatic cooling process can be completed by a mechanical cooling system.
This mechanical cooling is provided by either a Chilled water coil (CWT and CWR configurations)
or a DX system (DXT and DXR configurations) with integrated or remote condenser.
The Cyber Handler 2 works in 3 operating modes depending on the outdoor conditions:
•
Dry mode:
when the outdoor temperature is low enough, the cooling is provided by the plate
heat exchanger only (adiabatic and mechanical cooling OFF),
•
Wet mode:
when the outdoor temperature is not low enough to allow the plate heat
exchanger to provide the required cooling capacity, the adiabatic system switches on to cool
down the outdoor air.
•
Mix mode
(not available for units with only adiabatic cooling): when the outdoor temperature
is very high, the mechanical cooling switches on to top-up the indirect adiabatic cooling.