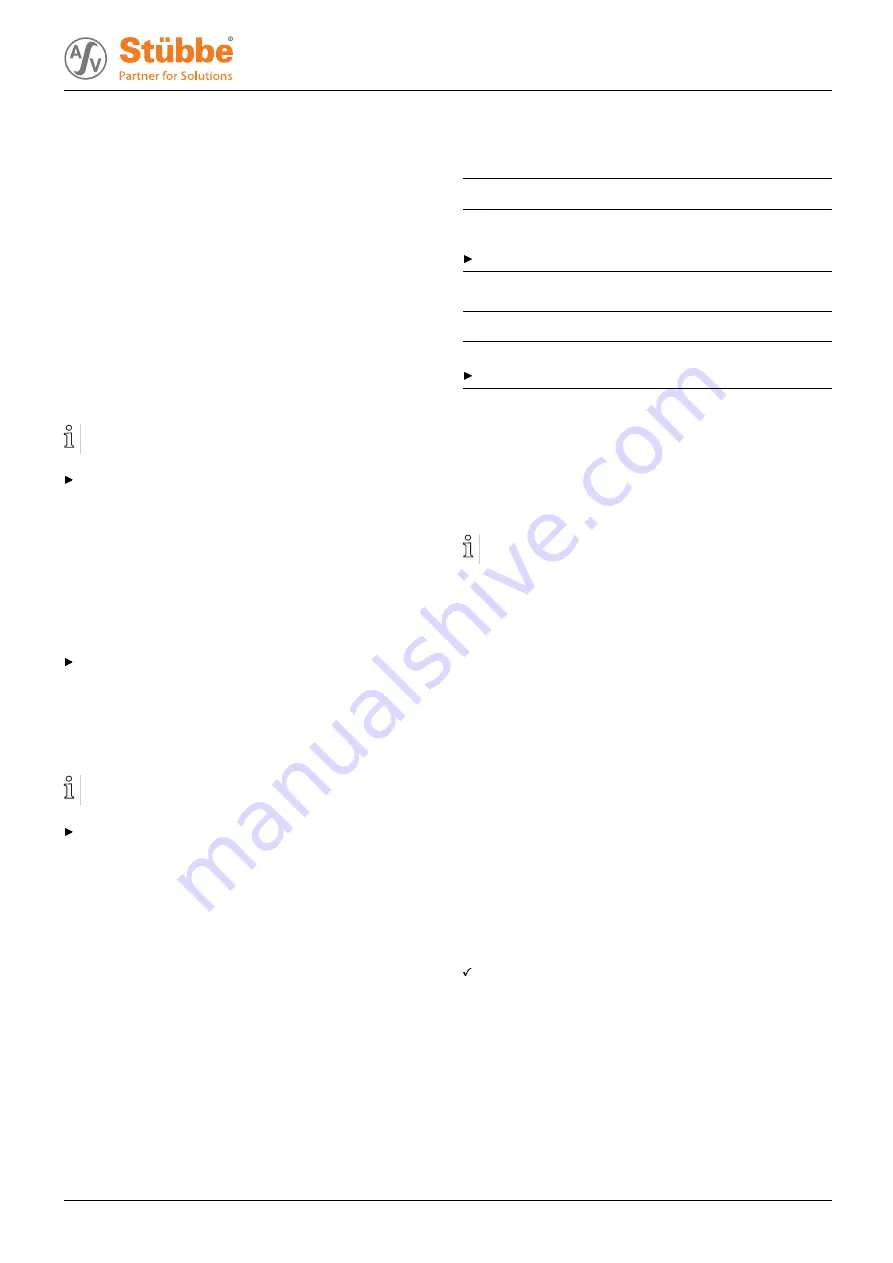
Installation and connection
5.3.7
Providing safety and control devices
(recommended)
Avoid contamination
1. Install
fi
lters in the suction pipe.
2. Install a differential pressure gauge with contact manome-
ter to monitor contamination.
Avoid reverse running
1. Ensure that the medium does not
fl
ow back after switch-
ing off the pump by using a non-return valve between dis-
charge
fl
ange and stop valve.
2. In order to enable venting, include vent connection
between discharge
fl
anges and non-return valve.
Make provisions for isolating and shutting off the pipes
For maintenance and repair work.
Provide shut-off devices in the suction pipe and pressure
line.
Allow measurements of the operating conditions
1. Provide pressure gauge in the suction pipe and pressure
line for pressure measurement.
2. Provide motorside load monitors (over and underload).
3. Provide pressure measurement on the pump side.
Providing dry run protection
In order to protect the pump from dry running and resulting
damage
–
Provide dry run protection
–
e.g. ASV PTM pressure and temperature monitoring
sensor
Provide an overpressure protection
Overpressure protection is required for operation in explo-
sive areas (
→
ATEX additional manual).
Provide an overpressure protection.
5.4
Connecting the pipes
NOTE
Material damage due to excessive forces and torques on
the pump.
Ensure pipe connection without tension.
5.4.1
Keeping the piping clean
NOTE
Material damage due to impurities in the pump!
Make sure no impurities can enter the pump.
1. Clean all piping parts and
fi
ttings prior to assembly.
2. Flush all pipes carefully with neutral medium.
3. Ensure no
fl
ange seals protrude inwards.
4. Remove any blind
fl
anges, plugs, protective foils and/or
protective paint from the
fl
anges.
5.4.2
Installing auxiliary pipes
Observe manufacturer information for any auxiliary sys-
tems present.
1. Connect the auxiliary pipes to the auxiliary connections so
that they are stress-free and do not leak.
2. Avoid formation of air pockets: Run the pipes with a con-
tinuous slope up to the pump.
5.4.3
Installing suction pipe
1. Remove the transport and sealing covers from the pump.
2. Fit suction pipe stress-free and sealed. (
3. Ensure no seals protrude inwards.
4. For the suction process: Install foot valve in the suction
pipe in order to prevent the pump and suction pipe from
dry running when pump is not running.
5.4.4
Installing the pressure pipe
1. Remove the transport and sealing covers from the pump.
2. Fit pressure line stress-free and sealed. (
3. Ensure no seals protrude inwards.
5.4.5
Inspection for stress-free pipe connections
Piping installed and cooled down
1. Disconnect the pipe connecting
fl
anges from the pump.
2. Check whether the pipes can be moved freely in all direc-
tions within the expected range of expansion:
–
Nominal width < 150 mm: by hand
–
Nominal width > 150 mm: with a small lever
3. Make sure the
fl
ange surfaces are parallel.
4. Reconnect the pipe connecting
fl
anges to the pump.
5. If present, check support foot for tension.
300 486
BA-2015.12.16 EN
SHB
17