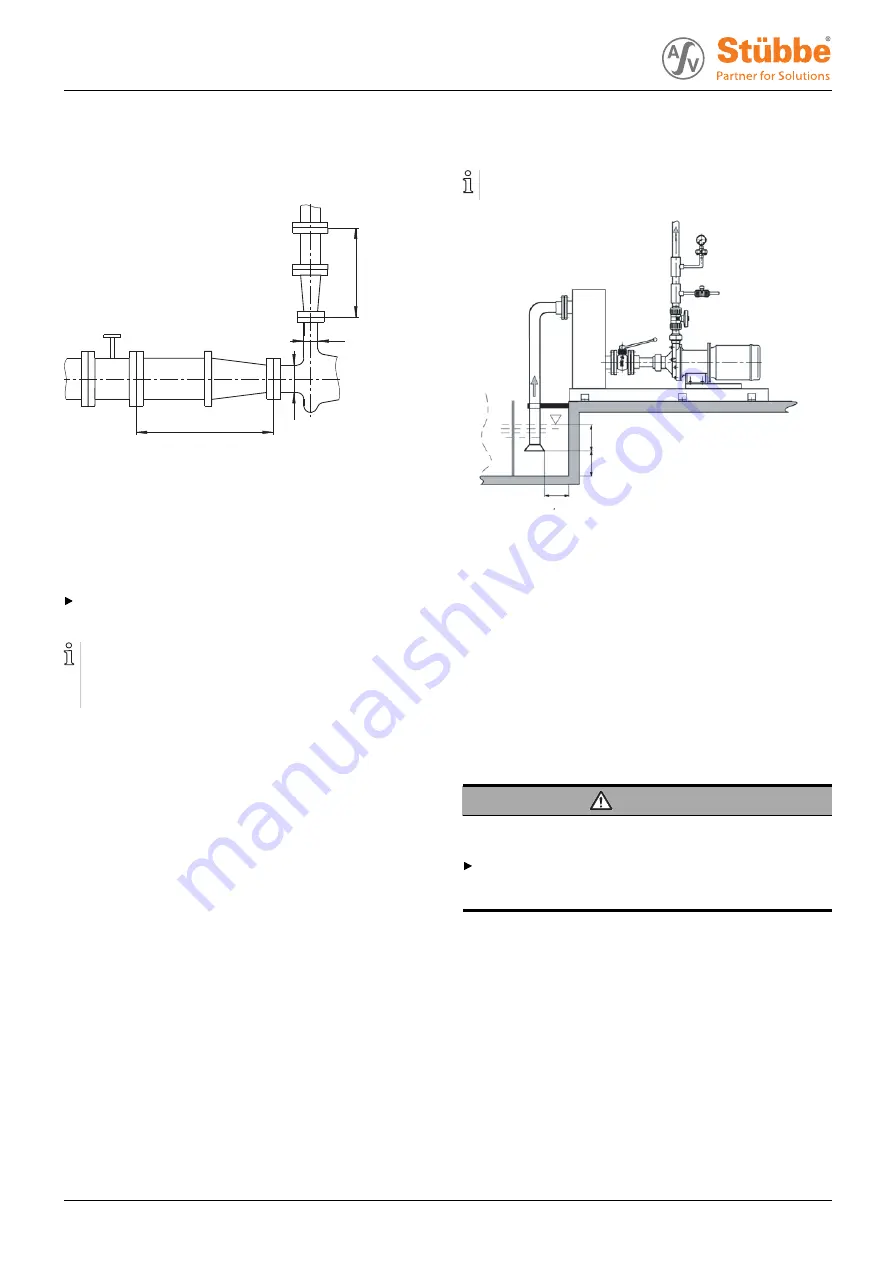
Installation and connection
5.3.3
Specifying pipe lengths
C
D
B
A
Fig. 7
Straight pipe lengths in front and after the
pumps (recommended)
A > 5x DNs
B DNs
C DNd
D > 5x DNd
Observe recommended minimum values when installing
the pump.
Suction side: Shorter lengths are possible, but may limit
hydraulic performance data.
Pressure side: Shorter lengths are possible, but may result
in increased noise development.
5.3.4
Provide self-priming container
A self-priming container can be used to make the pump
self-priming.
> 2xDN
> 1,5xDN
> 1,5xDN
1. Select container volumes according to the size of the
pump.
2. Clean containers carefully prior to commissioning or initial
fi
lling.
3. Install a straight section of pipe 5 to 10 x DN as a settling
pipe leading up to the pump intake.
5.3.5
Optimizing changes of cross section and
direction
1. Avoid radii of curvature of less than 1.5 times the nominal
pipe diameter.
2. Avoid abrupt changes of cross-section along the piping.
5.3.6
Discharging leaks
WARNING
Risk of injury and poisoning due to hazardous pumped
liquids!
Safely collect any leaking pumped liquid, then discharge
and dispose of it in accordance with environmental regula-
tions.
1. Provide equipment for collecting and discharging leaking
liquids.
2. Ensure the free discharge of leaking liquids.
16
SHB
BA-2015.12.16 EN
300 486