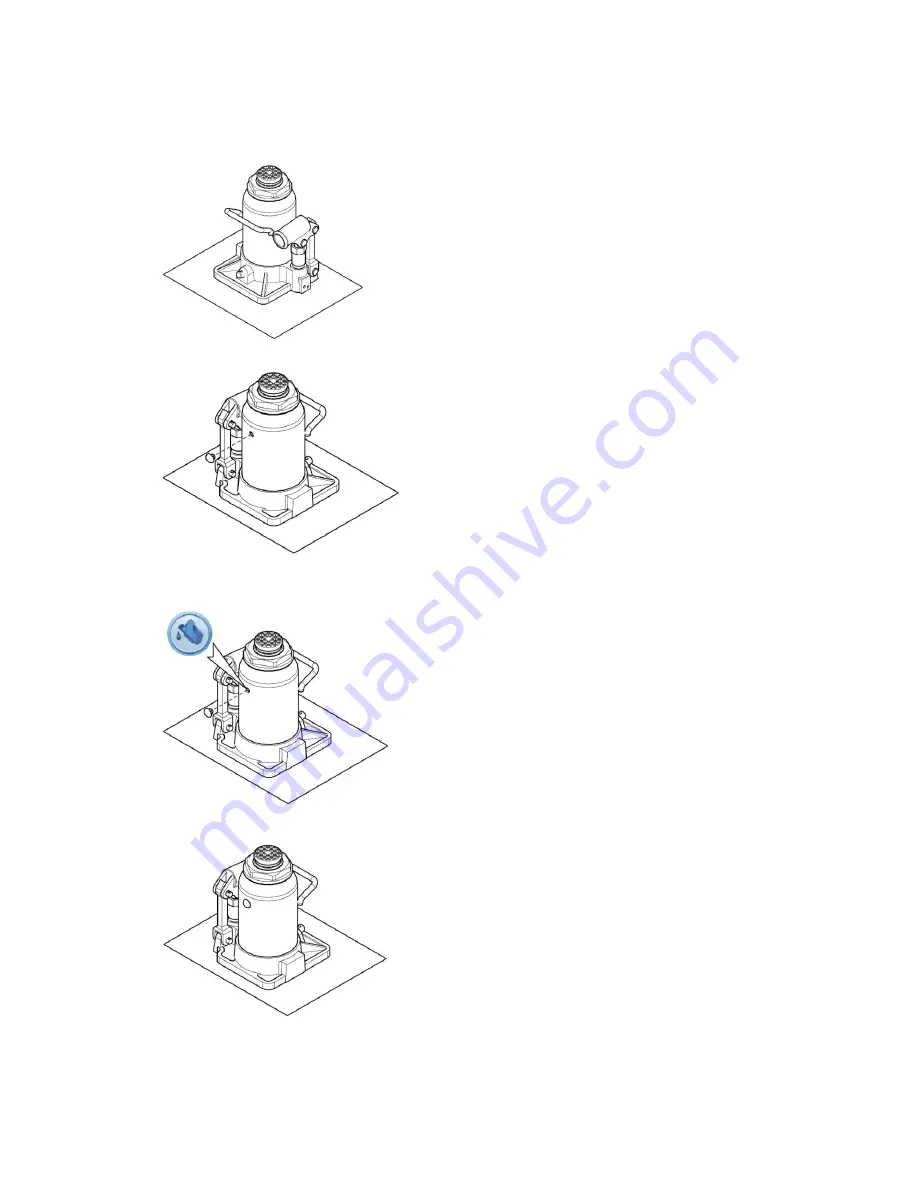
17
TO ADD JACK OIL:
The hydraulic cylinder assembly contains hydraulic fluid that must be kept at approximately 80% full at
all times for proper operation. To check the level and to fill remove oil filler plug.
1. Position the jack on level ground and lower the saddle.
2. Remove the oil plug.
3. Fill the oil case until oil level is just beneath the lower rim of the oil fill hole.
KEEP DIRT AND OTHER MATERIAL CLEAR WHEN POURING.
4. Replace oil plug.
5. Perform the Air Purge Procedure.
Содержание 47036
Страница 21: ...21 ASSEMBLY DIAGRAM ...
Страница 23: ...23 BOTTLE JACK ASSEMBLY DIAGRAM ...