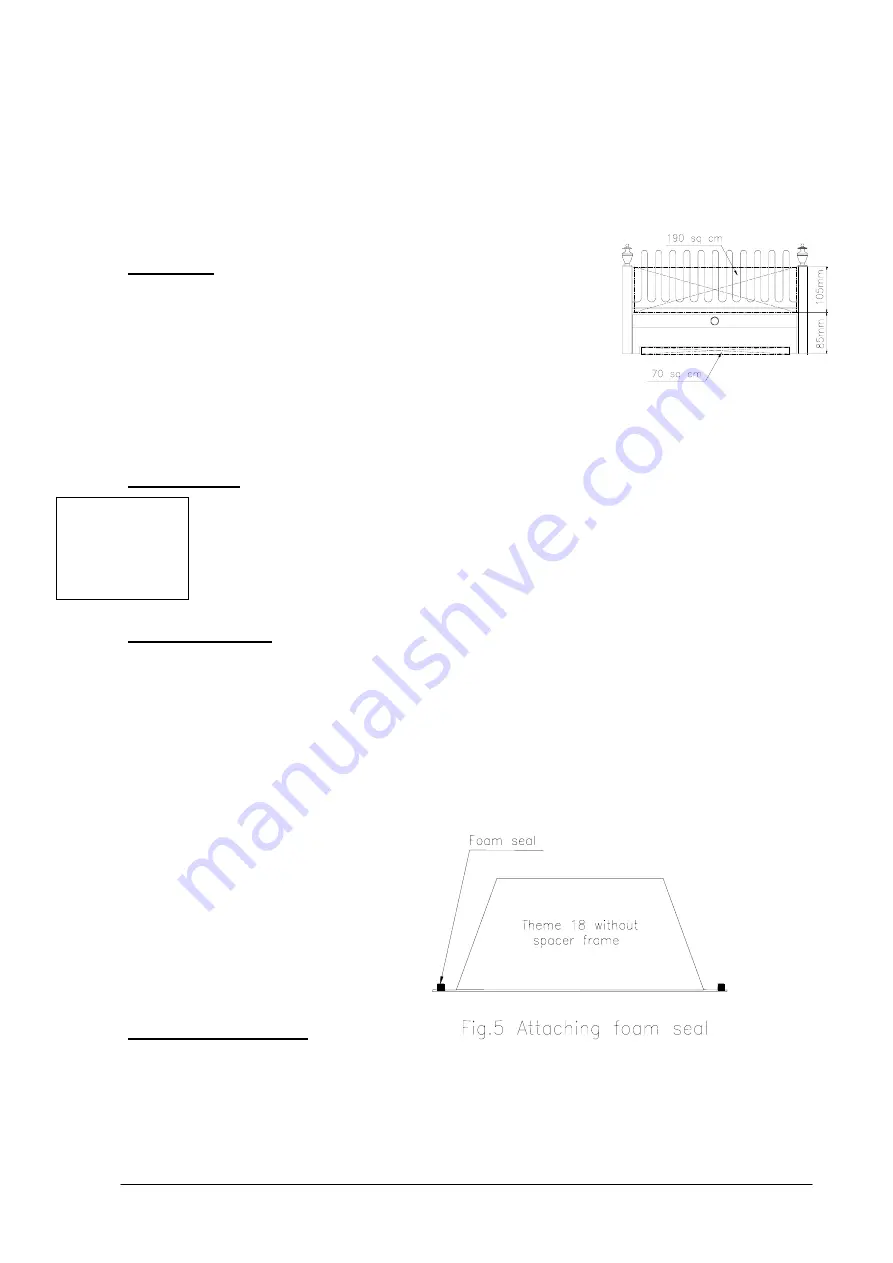
Theme 22 Issue 2.1 09/07/01
Page 3 of 12
10. Screws and wall plugs to complete the installation.
11. These installation instructions, guarantee card and end user operating instructions.
Warning:
Only Straxgas approved ceramic blocks and coals, designed for this appliance, must
be used with this burner. Use of ceramic components from any other supplier will invalidate the
guarantee or may be dangerous.
When unpacking the appliance, avoid touching the visible, painted parts as the paint requires
curing (this will take approximately 2 hours under fire. In some cases there may be a slight
odour given off for a short period).
Fret options
The following Straxgas frets are suitable for use with this appliance:
•
Black Broughton Classic
•
Silver Classic
•
Black finger
•
Brass finger
•
Gainsborough
•
Delta
If a fret from another manufacturer is being used, it must comply with the minimum free area
requirements shown in Fig. 1.
Gas connection
Note: Gas connection shall be with rigid or semi-rigid pipe, by concealed connection only. A
15mm (10mm for propane) gas supply pipe with isolation cock
should be brought to within
1M of the fireplace opening. The connection to the burner can be made from the right or left
hand side by a concealed pipe from behind the burner to the elbow on the left-hand side of
the burner. Use a pre-punched hole in the convection box to allow the gas supply pipe to be
installed. 8mm pipe is required for this purpose.
Assembly sequence
1. Fit the restrictor plate with its bottom edge inside the flue outlet, using 3 screws
provided, as shown in Fig. 3.
2.
For model S146H (4-sided version)
secure the separate bottom flange to the base of
the convection box using the screws supplied (Fig. 4).
3. Secure the self-adhesive foam-sealing strip to the back of the convection box flange
(Fig. 5).
4. Slide the firebox into position, making sure that the sealing strip is compressed and
forms an effective seal around the complete frame.
5. Drill the front face of the opening to match the 4 holes in the convection box flange and
insert the plugs provided.
6. Secure the convection box using the screws provided or alternatively use optional wire
fixing kit.
Wire Fixing Kit (Optional)
The kit supplied enables the convection box to be secured to the opening without drilling any
holes in the surround.
Items supplied:
1. 2 wire ropes with fixed nipple
2. 2 Sleeve bolts and backnuts
3. 2 Adjustable nipples with clamp screws
4.
4 Screweyes and wall plugs
When passing
the pipe through
brickwork or
plaster, cap the
end to prevent
entry of debris.
Fig. 1 Optional fret min. ventilation requirement