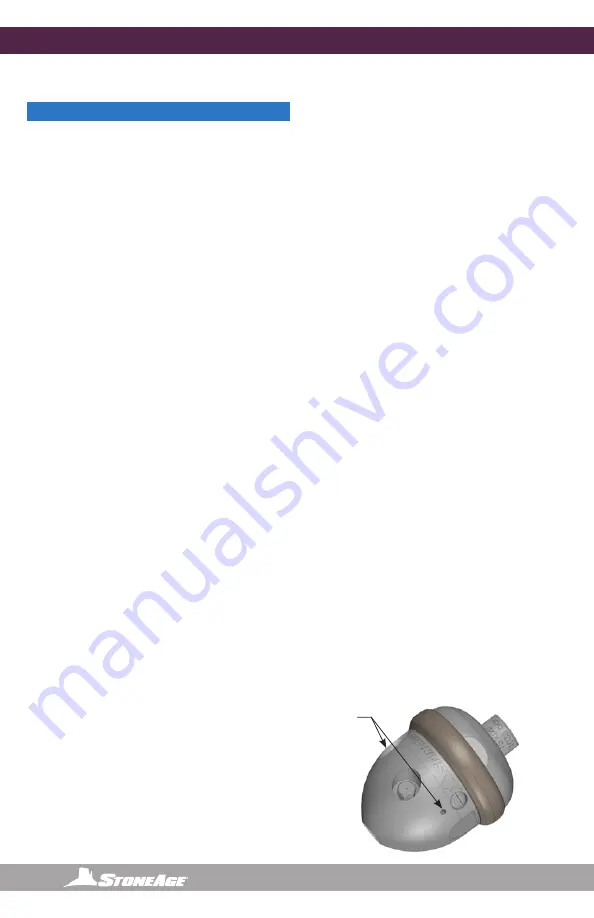
866-795-1586 • WWW.STONEAGETOOLS.COM
14
4” BADGER OPERATION AND TROUBLESHOOTING
OPERATION:
NOTICE
The two most important items in maintaining the
Badger tools;
- Keep debris from entering the tool and pre-
venting it from rotating by flushing high pressure
hoses before use.
- Keep the 4” and 6” models full of viscous fluid
to maintain control and rotation speed. When the
viscous fluid is lost or contaminated, the rotation
speed of the tool will increase, which reduce the
life of the high pressure seal and bearing.
1. Make sure the operator has a controlled
dump in the system and it is operated by
the person closest to the job. Test the dump
prior to beginning the job.
2. Flush out the high pressure hoses before
connecting the Badger™ to eliminate debris.
3. Attach tool to the end of the hose.
4. It is recommended that the hose be marked a
few feet from the end with a piece of tape so
the operator knows when to stop on the way
back out.
5. Position the tool in the pipe opening.
6. Close the dump and slowly bring the pump
up to pressure the first time to make sure
no nozzles are plugged and the jet thrust is
correct. The Badger should begin to slowly
rotate.
7. Once operating pressure is reached, feed the
tool into the pipe to begin the cleaning job.
8. Allow the jets time to do their work by
feeding the hose out at a controlled rate.
9. When the work is complete and the tool is
disconnected from the hose, blow out all
water to prolong the life of the tool.
10. A small amount of 3-IN-ONE or equivalent
lubricant can be blown into the tool as well.
TROUBLE SHOOTING:
HIGH-PRESSURE WATER SEAL LEAK:
• The high pressure seal may leak initially at
lower pressures, but should pop closed as
pressure is increased. A continuous leak
at operating pressure from the weep holes
indicates the need to replace the HP Seal and
Seat. HP Seals wearing out too quickly can
be an indication that the shaft bore is worn,
the HP Seat is installed upside-down, or the
tool is over spinning. Over spinning is caused
by low or contaminated viscous fluid, water
in the fluid chamber (replace shaft seals), or
too much jet torque. Refilling the viscous fluid
every 80-100 hours of operation is important
for proper speed control. Only use StoneAge
recommended viscous fluid.
TOOL SPINS TOO FAST:
• A significant increase in rotation speed means
that the speed control mechanism in the tool
has lost functionality. This can be a result
of viscous fluid loss or fluid contamination.
Operation of the tool in this state can
cause damage to other components and
accelerated wear of the high pressure seal. If
this occurs, the first step is to flush the tool
with new viscous fluid as shown below.
TOOL WILL NOT ROTATE:
• Check the nozzles for plugging or wear
(nozzles have to be removed to check for
obstructions), Check that the nozzle sizes
are correct for the desired flow and that the
desired flow matches the head flow range.
Check that the nozzle sizes are installed in
a balanced configuration. If the tool feels
rough when manually rotating the head, this
indicates internal damage. Replace bearings,
shaft seals, viscous fluid, and check the Inner
and Outer Discs for flatness. These discs
can be deformed if tool is reassembled
when discs are not properly aligned with the
internal flats inside the head.
WEEP
HOLES