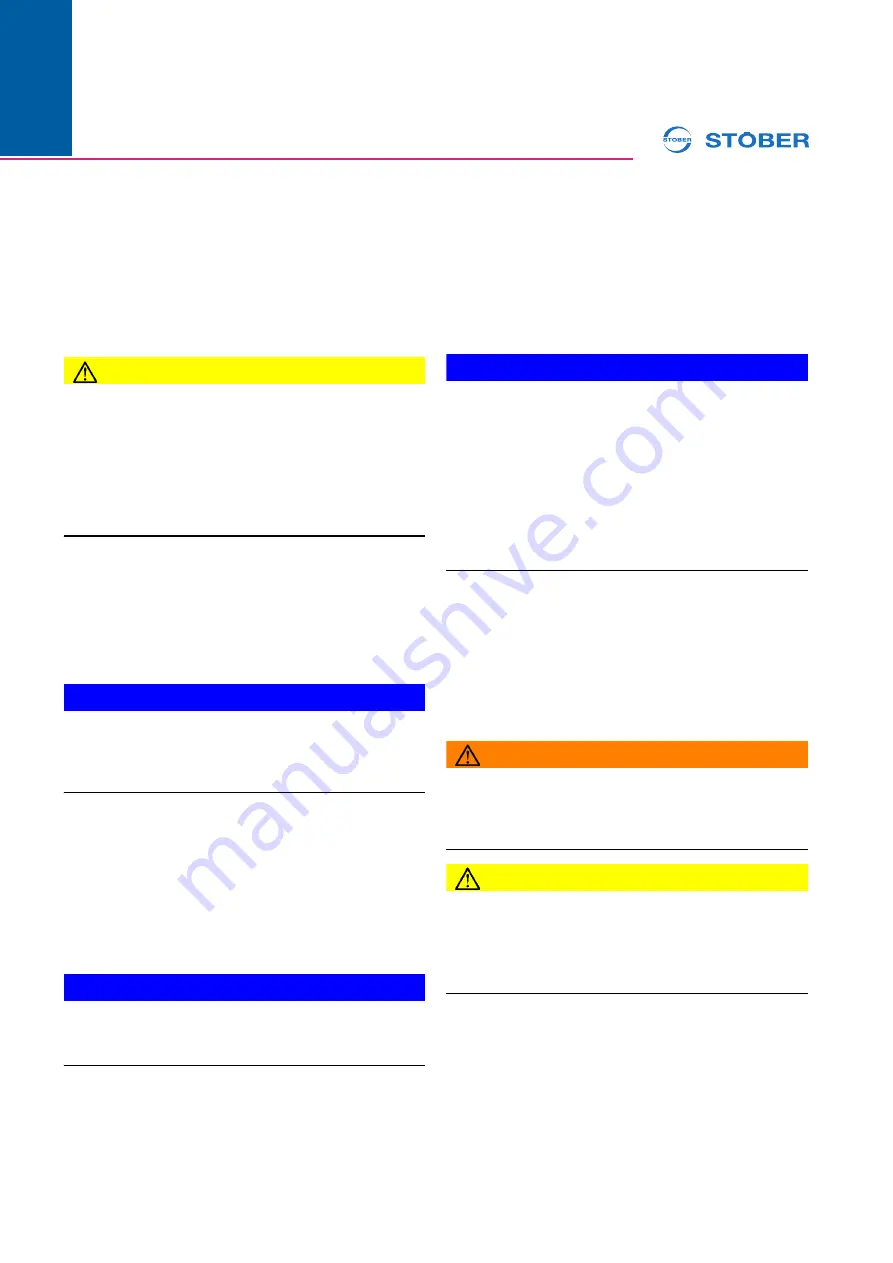
Operating manual
EZ/EZHD/EZHP synchronous servo motors, EZS/EZM synchronous servo motors for screw
drive
2
ID 443032_en.01
WE KEEP THINGS MOVING
05/2019
en
www.stober.com
2.1 Temperature sensor
STOBER synchronous servo motors are equipped with a
PTC thermistor to realize thermal winding protection as stan-
dard. The Pt1000 temperature sensor can be chosen as an
option. The Pt1000 replaces the previously available KTY 84-
130 that is only available for a limited time. The type of in-
stalled temperature sensor is stated on the nameplate of the
motor. Make note of the additional information specified in the
STOBER catalog and in the commissioning instructions for
the drive controller.
CAUTION!
Motor damage, fire risk!
If the winding temperature of the motor is not adequately
monitored, motor damage and fires may result. Claims under
the warranty are then void.
Always connect the installed temperature sensor to an
appropriate triggering unit so that the motor is switched
off if the maximum permitted winding temperature is ex-
ceeded.
You must take precautions to ensure that no hazard could oc-
cur after the thermal winding protection has responded and
the motor has then cooled off by unintentional automatic
switching on of the motor again!
2.1.1 PTC thermistor
The PTC thermistor is designed as a triplet. All three phases
of the motor winding are therefore monitored.
NOTICE
Damage to the PTC thermistor due to high connection
voltage.
Make sure that the maximum connection voltage of the
PTC thermistor is below 7.5 V DC.
2.1.2 Temperature sensor Pt1000
Optionally the temperature-dependent resistor Pt1000 can be
installed as a temperature sensor in one phase of the motor
winding. The resistance of the Pt1000 is proportional to the
temperature of the motor winding.
Make sure that the Pt1000 temperature sensor only protects
the motor to a limited degree before overload. For this reason,
parameterize the I2t monitoring of the drive controller to
"WARNING".
NOTICE
Falsification of the measured value due to self-heating of
the temperature sensor for a sensor current > 4 mA.
Ensure a constant sensor current of 2 mA.
2.1.3 Temperature sensor KTY
Optionally the temperature-dependent resistor KTY 84-130
can be installed as a temperature sensor in one phase of the
motor winding. The resistance of the KTY is proportional to
the temperature of the motor winding.
Make sure that the KTY temperature sensor only protects the
motor to a limited degree before overload. For this reason, pa-
rameterize the I2t monitoring of the drive controller to
"WARNING".
Ensure a constant sensor current of 2 mA.
NOTICE
Damage to the temperature sensor!
Prevent sensor currents > 4mA that can cause unaccept-
ably high self-heating of the temperature sensor as well
as damage to its insulation and at the motor winding.
Pay attention to the polarity of the connections that are
described in the supplied connection plan when connect-
ing the temperature sensor KTY.
Do touch your fingers on the connector contacts of the
motor because the temperature sensor can get damaged
due to electrostatic discharge.
2.2 Encoder systems
Synchronous servo motors have an encoder system integrat-
ed into the motor for motor commutation and recording of po-
sition. Two-pole resolvers are possible as well as absolute
encoders in various versions.
Note the relevant motor connection diagram and the details
on the motor nameplate. The encoder systems have been set
to the respective servo inverters in the factory.
WARNING!
Changes to the factory settings of encoder systems may
result in uncontrolled startup or vibrating movements of
the motor shaft.
Therefore the factory settings must not be changed.
CAUTION!
ESD/EGB safety information
This product contains components that can be damaged or
destroyed by electrostatic discharges.
Always avoid directly touching the pin contacts with your
fingers!