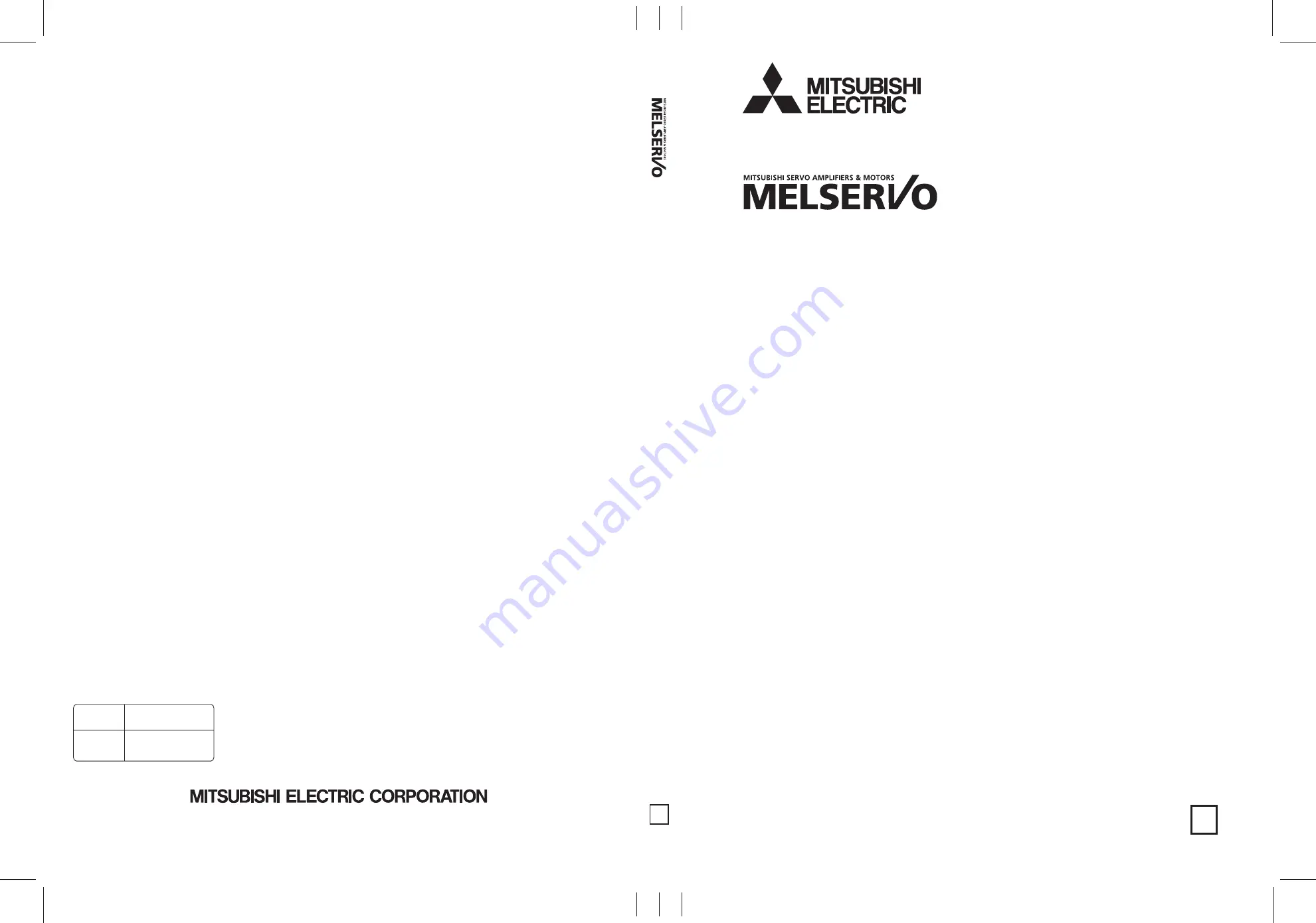
SH(NA)030112ENG-H(1710)MEE Printed in Japan
Specifications are subject to change without notice.
This Instruction Manual uses recycled paper.
MODEL
MODEL
CODE
DIRECT DRIVE MOTOR INSTRUCTION MANUAL
H
General-Purpose AC Servo
MODEL
TM-RFM
TM-RG2M
TM-RU2M
DIRECT DRIVE MOTOR INSTRUCTION MANUAL
1CW948
DIRECT DRIVEMOTOR
INSTRUCTIONMANUAL
H
HEAD OFFICE: TOKYO BLDG MARUNOUCHI TOKYO 100-8310
Summary of Contents for TM-RFM
Page 11: ...1 INTRODUCTION 1 2 MEMO ...
Page 19: ...2 INSTALLATION 2 8 MEMO ...
Page 35: ...5 CONNECTION OF SERVO AMPLIFIER AND DIRECT DRIVE MOTOR 5 8 MEMO ...
Page 45: ...6 WIRING OPTION 6 10 MEMO ...
Page 77: ...MEMO ...