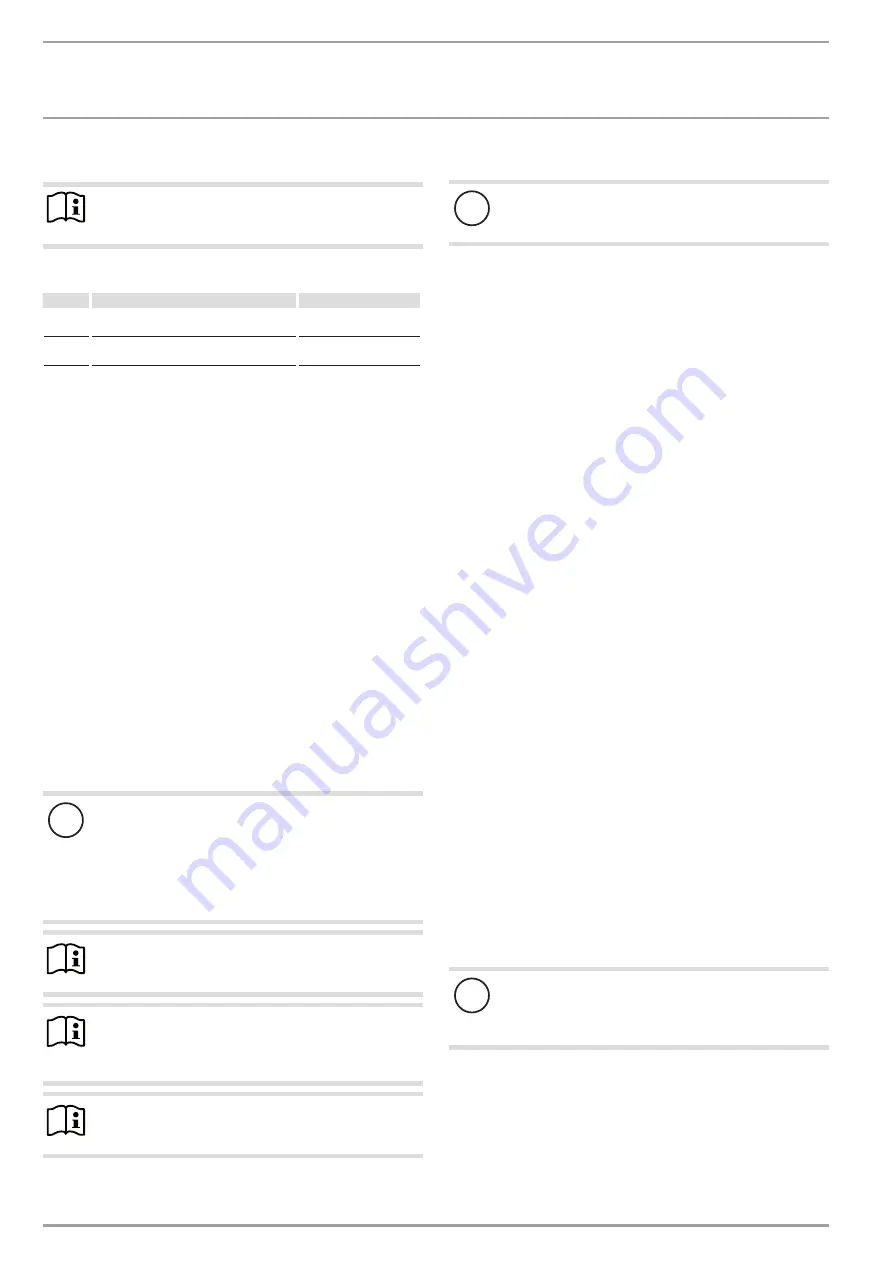
INSTALLATION
Installation
54
| WPE-I H 400 Premium
www.stiebel-eltron.com
10.4 Installing the heat source system
Note
Engineer the heat source system for the brine | water heat
pump according to the technical guides.
Permitted brine:
Part number
MEG 10 Heat transfer medium as concentrate on
an ethylene glycol base
231109
MEG 30 Heat transfer medium as concentrate on
an ethylene glycol base
161696
10.4.1 Connection
f
f
Thoroughly flush the pipework with brine before connecting
the heat pump to the heat source circuit. Foreign bodies,
such as rust, sand and sealant, can impair the operational
reliability of the heat pump.
f
f
Insert a filter (maximum mesh size 0.7 mm) in the heat
source flow.
f
f
Install the heat source flow and heat source return with all
the necessary components.
f
f
Insulate the heat source flow and heat source return against
vapour diffusion to prevent the formation of condensate.
f
f
Size the diaphragm expansion vessel according to the manu-
facturer's instructions. The maximum operating pressure of
the heat source is 6 bar.
f
f
Check for tightness.
10.5 Flow and return connection
10.5.1 Heating water quality
Carry out a fill water analysis before filling the system. This may,
for example, be requested from the relevant water supply utility.
!
Material losses
To avoid damage as a result of scaling, it may be neces-
sary to soften or desalinate the fill water. Always observe
the fill water limits specified in the “Specification / Data
table” chapter.
f
f
Recheck these limits 8-12 weeks after commission-
ing and as part of the annual system maintenance.
Note
With a conductivity > 1000 μS/cm, desalination treatment
is recommended in order to avoid corrosion.
Note
Suitable appliances for water softening and desalinating,
as well as for charging and flushing heating systems, can
be obtained via trade suppliers.
Note
If you treat the fill water with inhibitors or additives, the
same limits apply as for desalination.
f
f
Avoid chemical and oil contamination.
10.5.2 Heating water connection
!
Material losses
Ensure the supply lines are not under tension, in order
to avoid leaks.
The heating system to which the heat pump is connected must be
installed by a qualified contractor in accordance with the water
installation diagrams that are part of the technical guides.
f
f
Thoroughly flush the pipework before connecting the heat
pump. Foreign bodies, such as rust, sand and sealant, can
impair the operational reliability of the heat pump.
f
f
Construct the heating flow and return from a heat-resistant
and corrosion-resistant material (e.g. copper).
f
f
Install a dirt trap (maximum mesh size 0.7 mm) in the heat-
ing return in the immediate vicinity of the appliance.
f
f
Connect the heating system to the “heating flow” and “heat-
ing return” connections. Check for tightness.
f
f
Ensure that the heating flow and return are connected cor-
rectly.
f
f
Install air vent valves at the required positions.
f
f
Install the heating circuit pump in the heating flow.
f
f
Install a fill connector with a non-return valve.
f
f
When sizing the heating circuit, observe the maximum avail-
able external pressure differential (see chapter “Specifica-
tion / Data table”).
f
f
Provide thermal insulation in accordance with applicable
regulations.
10.5.3 Safety valve
f
f
In heating systems with a sealed unvented diaphragm ex-
pansion vessel, install a pressure gauge and a safety valve
(min. 20 DN) with a maximum opening pressure of 6 bar.
f
f
Ensure the connection pipe of the diaphragm expansion ves-
sel has a steady fall to the safety valve.
f
f
Install the safety valve drain with a constant fall to the dis-
charge outlet. When installing the drain, never kink the drain
hose.
f
f
Ensure that the safety valve drain is open to the outside and
free from the risk of frost.
f
f
Size the discharge outlet so that water can drain off unim-
peded when the safety valve is fully opened.
10.6 Oxygen diffusion
!
Material losses
Do not use open vented heating systems. Use oxygen
diffusion-proof pipes in underfloor heating systems with
plastic pipework.
In underfloor heating systems with plastic pipes that are per-
meable to oxygen and in open vented heating systems, oxygen
diffusion may lead to corrosion on the steel components of the
heating system (e.g. on the indirect coil of the DHW cylinder, on
buffer cylinders, steel radiators or steel pipes).
f
f
With heating systems that are permeable to oxygen, separate
the heating system between the heating circuit and the buff-
er cylinder.