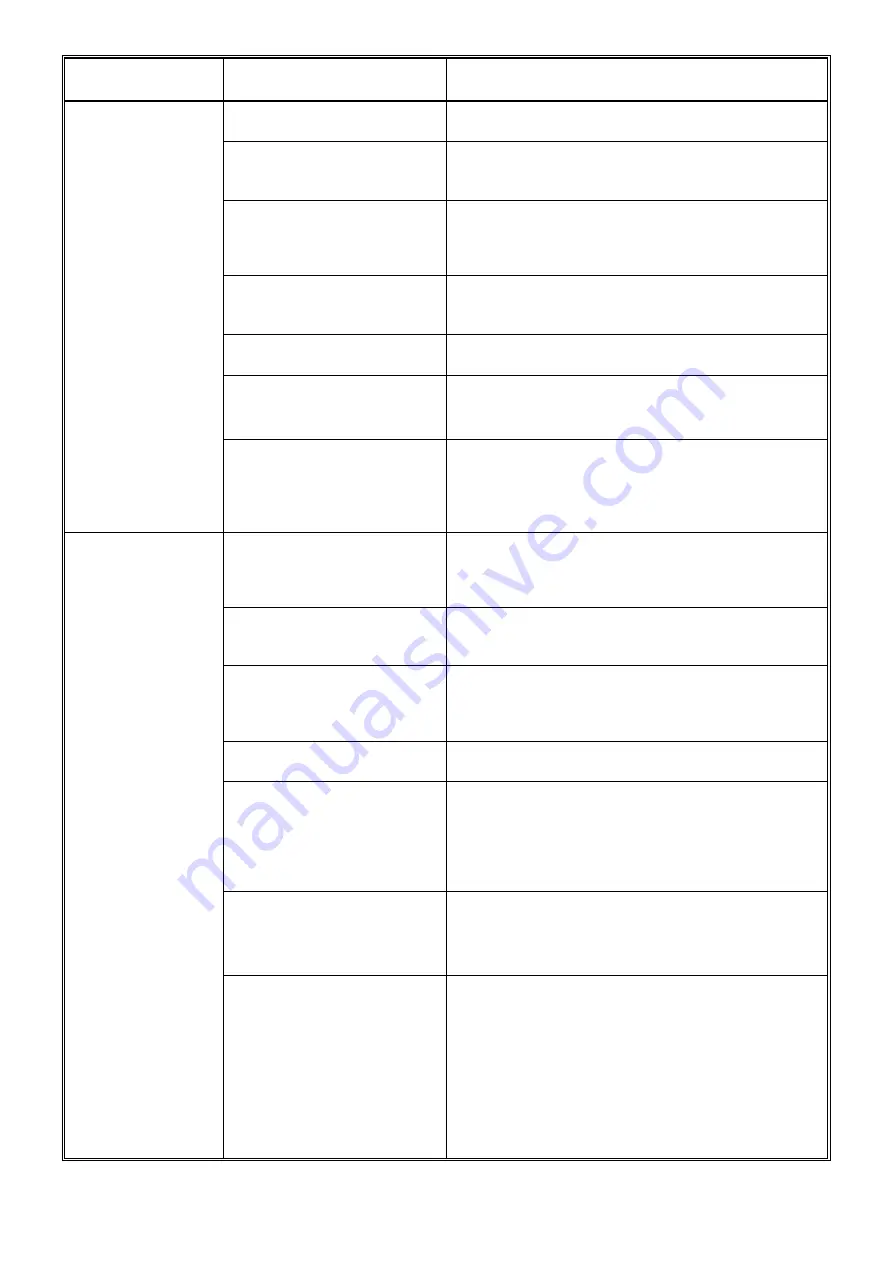
25
FAULT POSSIBLE
CASE REMEDY
No mains power.
Have fault corrected by a qualified electrician.
Oil level too low.
Add oil as necessary, refer to lubricating instructions on
lifting column.
Air in hydraulic pump (only
possible after the tank has been
empty).
Press the
⇑
(UP) and SET REF buttons until the lifting
column rises (max. 1 minute).
Safety valve not properly
adjusted
Have valve adjusted, contact Service Department to
check valve.
Pump has insufficient yield.
Replace the pump.
Column does not lift.
Power interrupted by thermal
relay in primary control box.
Reset the thermal relay.
If the defect occurs again, contact the service department.
Maximum height difference
(more than 2 1/2") exceeded.
Set the main switch to OFF and ON. Press the "SET REF"
button twice to make the system ready for operation again.
If the defect occurs again, contact the service department.
Column does not
lower.
No mains power.
Have fault corrected by a qualified electrician.
Catch not disengaged from
locking system.
Raise column approximately 2" and then lower.
The electrically operated
lowering valve on the hydraulic
unit does not open.
No mains power for solenoid or lowering valve is faulty.
fault Have corrected by the Service Department.
Dirty lowering valve.
Have valve cleaned or replaced by service department.
Maximum height difference
(more than 1 1/4") exceeded.
Press on lifting until the height difference has been
cancelled out. If lifting is not desired, the "SET REF" button
can be pressed once. Following, lowering can be activated.
The difference of 1 1/4" will be maintained.
If the defect occurs again, contact the service department.
Maximum height difference
(more than 2 1/2") exceeded.
Set the main switch to OFF and ON. Press the "SET REF"
button twice to make the system ready for operation again.
If the defect occurs again, contact the service department.
(From highest position) Setting to
the highest position practically
coincides with the engagement of
the catch.
Slightly raise the ramp by touching S2. Then set highest
position stop (see fig. 7.1)
Содержание ST 1055
Страница 1: ...Mobile Column Lifts ST 1055 ST 1060 ST 1072 Installation operation service 325 58 990A ...
Страница 2: ......
Страница 5: ......
Страница 34: ...29 FIG A ...
Страница 36: ...31 FIG B ...
Страница 40: ...35 FIG F ELECTRICAL DIAGRAM CONTROLBOX PRIMARY ...
Страница 42: ...37 FIG H ELECTRICAL DIAGRAM SECONDARY COLUMN ...
Страница 47: ...42 FIG M DIMENSIONAL DRAWING ST 1072 ST 1055 ST 1060 ST 1072 V widened model 27 49 ...
Страница 49: ......