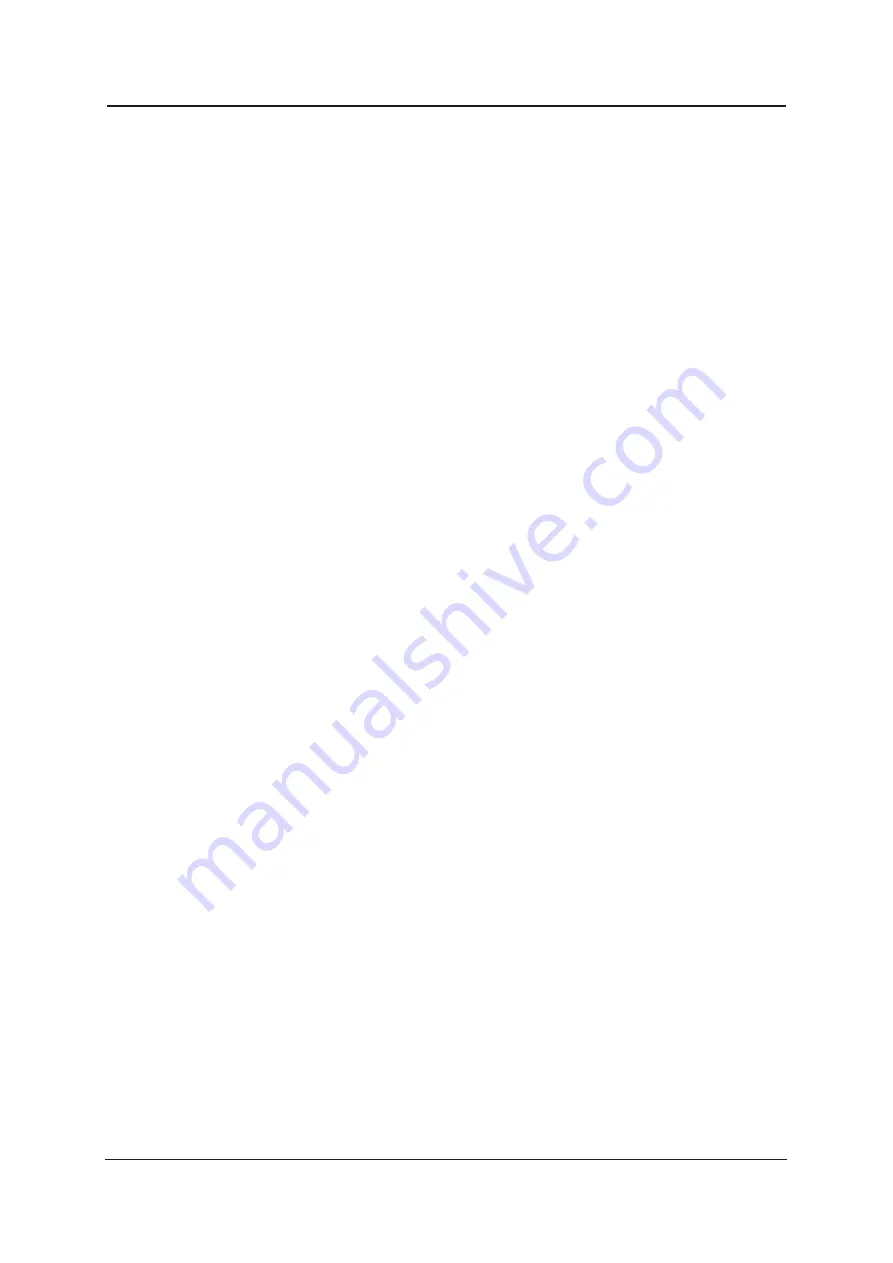
7
Properties and Features
SensoGate® WA 130 H Retractable Fitting
Hygienic design and sterilizability apply not only to the process side but also to the rinsing cham-
ber. The only part of the immersion tube which comes into contact with the process is that part
which was previously sterilized in the rinsing chamber.
This means that its suitability for use in pharmaceutical and food applications is proven, which
allows validation in FDA-regulated production processes.
Properties and Features
• With regard to hygienic design and sterilizability, all process-wetted parts incl. the rinsing/
calibration chamber comply with the recommendations of EHEDG (TNO report V7942 dated
February 25, 2008)
• Directed flow rinses the process seal from the process side as well as from the inside
of the fitting
• Prevention of re-contamination and safe separation to the process during probe movement
• Double sealings with leakage bores prevent microbial contamination of the drive
• Cost reduction by simple installation, operation and maintenance
• Protective rinsing of the seals for a long service life
• SensoLock for high safety of operation
• Integrated limit switches
• Fast and uncomplicated replacement of calibration chamber and immersion tube
• Cyclone rinsing for optimum cleaning effect
• Superior sensor immersion depth
• Standard sensor length (225 mm) even for large immersion depths
• Process-wetted parts made of electropolished stainless steel 1.4404
• Special version for sensors with pressurizable liquid electrolyte
• SIP and CIP capable process side
Содержание SensoGate WA 130 H
Страница 1: ...SensoGate WA 130 H User Manual Retractable Fitting ...
Страница 47: ......