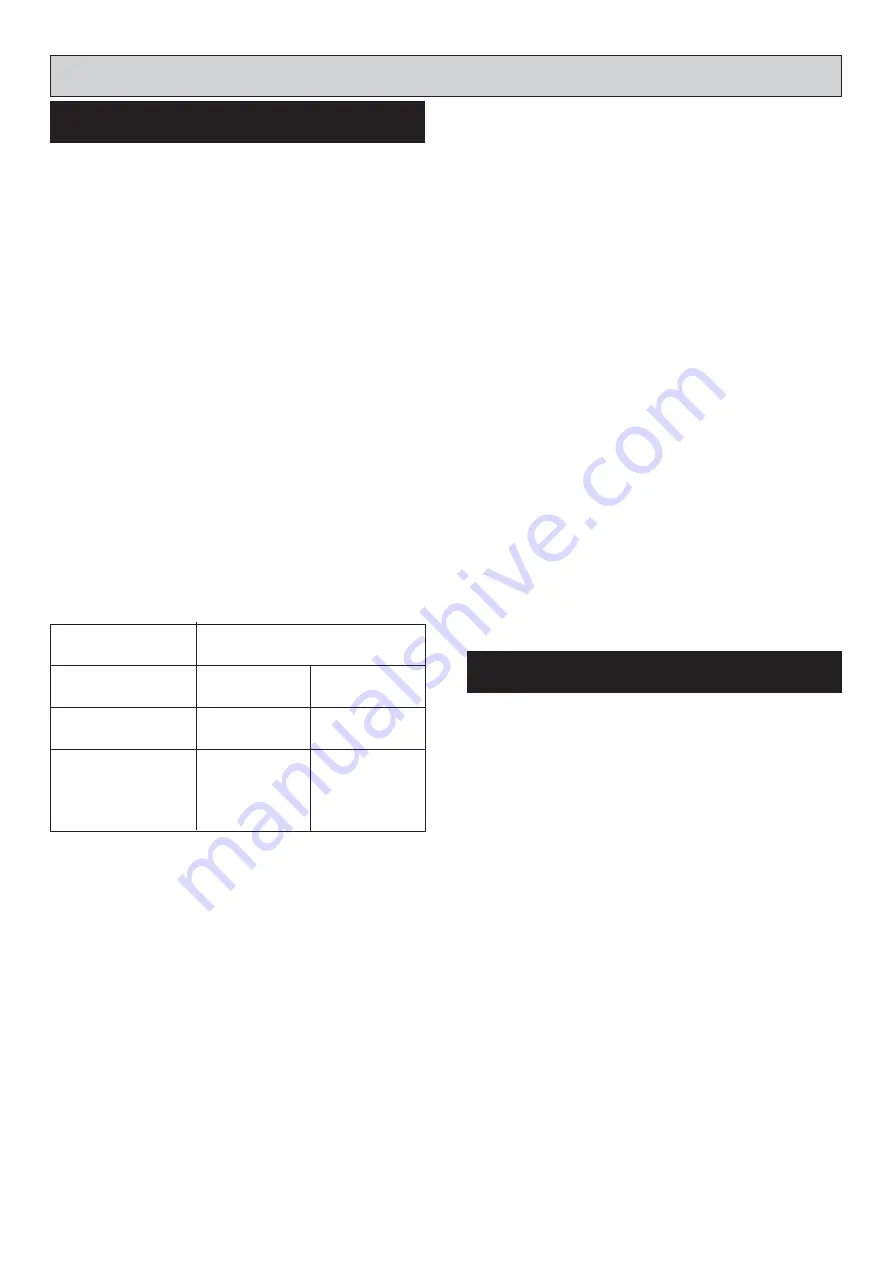
SEE FIG. 16
a.
The installation must comply with the requirements of
BS 6798 and BS 5449. Maximum water 82°C
temperature.
b.
A safety set to operate at 3 bar (30Ibf/In
2
) shall be
fitted in the flow pipe close to the boiler. There must
not be any valve between the safety valve and the
boiler. The valve should be positioned on a discharge
pipe fitted to prevent any discharge or creating a
hazard to occupants or cause damage to electrical
components and wiring.
c.
A pressure gauge covering at least the range 0 to 4
bar (0 to 60 Ibf/In
2
) shall be fitted in the system, in a
visible position.
d.
A diaphragm type expansion vessel, to BS 4814 shall
be connected at a point in the return pipe close to the
boiler. The vessel must be chosen to suit the volume
of water in the cistern and the system charge must not
be less than the static head at the point of connection.
Further details can be obtained from ‘British Gas
Specification for Domestic Wet Central Heating
Systems Part 3 Sealed Systems’.
Vs = System Volume Litres
e.
The hot water cylinder shall be either the indirect coil
type or a cylinder fitted with a calorifer which is suitable
for the system pressure.
f. The Make-Up System
Provision shall be made for replacing the lost water
from the system by either of the following methods:
a)
From a make-up vessel or tank, and connected
through a non-return valve to the system on the return
side of the hot water cylinder or return side of all heat
emitters or radiators.
b)
Where access to a make-up vessel would be difficult,
by a remote automatic pressurisation and make-up
unit.
g. Mains Connection
There shall be no connection to mains water supply or
to the water storage cistern supplying domestic hot
water, even though a non-return valve may be fitted,
without the approval of the local water authority.
h. The Filling Point
The system shall be fitted with a filling point at a low
level, and be used in accordance with the local water
authority requirement, and shall generally have a stop
valve to BS 1010.
i. Commissioning - General
The system shall be filled by water by a method
acceptable to the Local Water Authority.
Check the operation of the safety valve manually.
Test the operation of the high limit cut-out according to the
manufacturers instructions.
After flushing and re-filling the system either:-
(a) If a make-up vessel is filled release water from the
safety valve until the level in the make-up bottle falls
visibly, then top up the make-up bottle.
(b) If there is no make-up vessel either release or
introduce water until the designed cold water
pressure level is reached.
Follow the commissioning instructions as for open vented
systems. See Section Commissioning Instructions with
the following additions:-
Fill the system until the pressure gauge reads 1.5 bar
(22Ibf/In
2
). Clear any airlocks and check for water
soundness.
Check the operation of the safety valve, by allowing the
water pressure to rise until the valve opens. The valve
should open within ±0.3 bar (±4.35 Ibf/In
2
) of the pre-set
pressure. If this is not possible conduct a manual check
and test.
Release cold water for initial filling pressure.
Any set pointer gauge should be set to coincide with the
recommended filling pressure.
Sealed Systems
SEALED SYSTEM REQUIREMENTS
Safety Valve Setting
3.0 bar
Vessel charge and
initial system pressure
0.5 bar
1.0 bar
0.16
L
Vs
x
0.16
0.09
L
Vs
x
0.09
Multiplying Factor
Expansion Vessel
volume (litres)
= System volume Vs x
factor
COMMISSIONING
21
Содержание Alpha 120K
Страница 13: ...13 Site requirements FIG 6 External wiring with 2 zone valves ...
Страница 14: ...Site requirements 14 FIG 7 ...
Страница 22: ...22 FIG 16 ...
Страница 23: ...23 ...