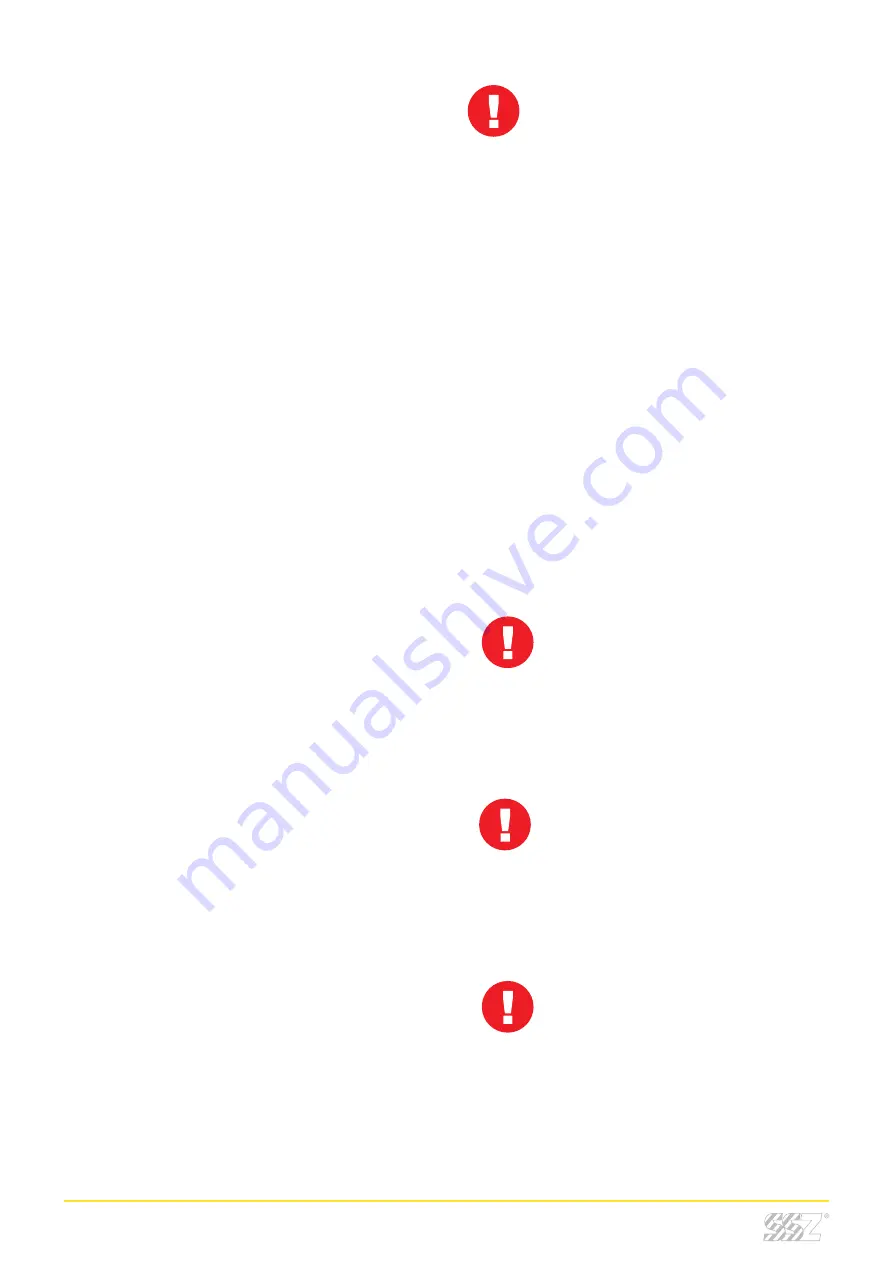
www.ssz-gmbh.de [email protected] Thüringerstrasse 17, 46286 Dorsten
13
Manual reset for SSZ-RZ4B control unit
The SSZ-RZ4B control unit is provided with automatic or manual
reset functions. Regarding the automatic reset function, the
functions are the same as in the SSS-RZ4 control unit. In case of
manual reset operation of reset button has no effect on output of
output signal switching device as long as forcepresent on sensor.
The output of output signal switching device remains in OFF state
. After removing the actuating force from sensor, signal switching
device remains in OFF state even though reset signal still present.
When releasing of reset button has no effect on output of output
signal switching device.
Reset is achieved after another operation of reset button without
actuating force on the sensor.
The SSZ-RZ4B is designed exclusively for use with safety bumper!
An SSZ-safety bumper is most often used to protect driverless
vehickles. The use of an SSZ-RZ4B control unit protects against
automatic movement, which may occur after incidental bridging
or failure of the reset function with a simultaneous release of
the bumper.
Manual reset control for SSZ-RZ4 and SSZ-RZ4B unit
1. Press the SSZ-pressure-sensitive device
2. Make sure that no one of the SSZ pressure sensitive devices
is pressed
•
The green LED`s “OK 3/5” and “4/6 OK” are off
•
The relais contacts of the channel K1 & K2 are opened
3. Press the reset button
•
The “OK 3/5” and “4/6 OK” green LEDs are on
•
The relais contacts of the channel K1 & K2 are closed
4. Press the SSZ pressure-sensitive device
•
The “OK 3/5” and “4/6 OK” green LEDs are switch off
•
The relais contact of the channel K1 & K 2 are opened
5. Unlock the pressure-sensitive device
•
The “OK 3/5” and “4/6 OK” green LEDs are switched off
•
The relais of the contacts channel K1 & K2 are opened
6. Press the reset button, while the pressure-sensitive device
should not be pressed
•
The “OK 3/5” and “4/6 OK” green LEDs are switched on
•
The relais contacts of the channel K1 & K2 are closed
•
The SSZ-pressure-sensitive device is unlocked and ready
for operation
Do not switch on the machine as long as there
is any risk!
The SSZ-control unit check shall include:
•
Visual check of the housing for possible damages.
•
Exclusion of possible manipulations. The SSZ hologram shall
remain intact.
•
Operation and functionality check executed acc. to this
Operation Manual.
•
Checking the correctness of the installation in the electric box.
•
Ensuring the correctness of connection to machine or device
After completing the assembly and function requirements the
system may be approved for use, according to the applicable
standards and regulations of the country of use.
The user may replace parts, using
exclusively their equivalents approved by
the manufacturer! Any modifications or
installations of other components / devices in
the system shall be prohibited. The SSZ control
unit shall be the only device suitable for control
of SSZ sensitive devices. Replacing SSZ control
unit or pressure-sensitive devices by products
of other vendors poses a risk of functionality
failure or total collapse for the entire system!
No spare parts for the above-mentioned
system. In case of any failure, replacement
parts shall be sought from the manufacturer,
including the control unit, the cable, the
aluminium profile or the pressure-sensitive
device.
In order to ensure proper functionality
of a pressure-sensitive protective device,
as well as its installation, adhering to the
requirements of EN-ISO 13849-1-2 and EN ISO
13856-1-3 : 2013-1, the technical personnel
shall be familiar with assembly techniques,
as well as with gear and systems, supported
by training at the SSZ-GmbH Company or at
an agency, designated for the purpose by the
manufacturer.
In case of any technical problems, it is recommended to contact
the manufacturer or any responsible agency, representing the
manufacturer at a given country. See the manufacturer’s home-
page www.ssz-gmbh.de for the actual list of representatives.
Periodical inspections of the control unit should be carried out
at least twice a month, while the functionality of signalling lights
– LEDs – should be a subject of daily control. The frequency of
the inspections should be estimated appropriate to the safety
function activations