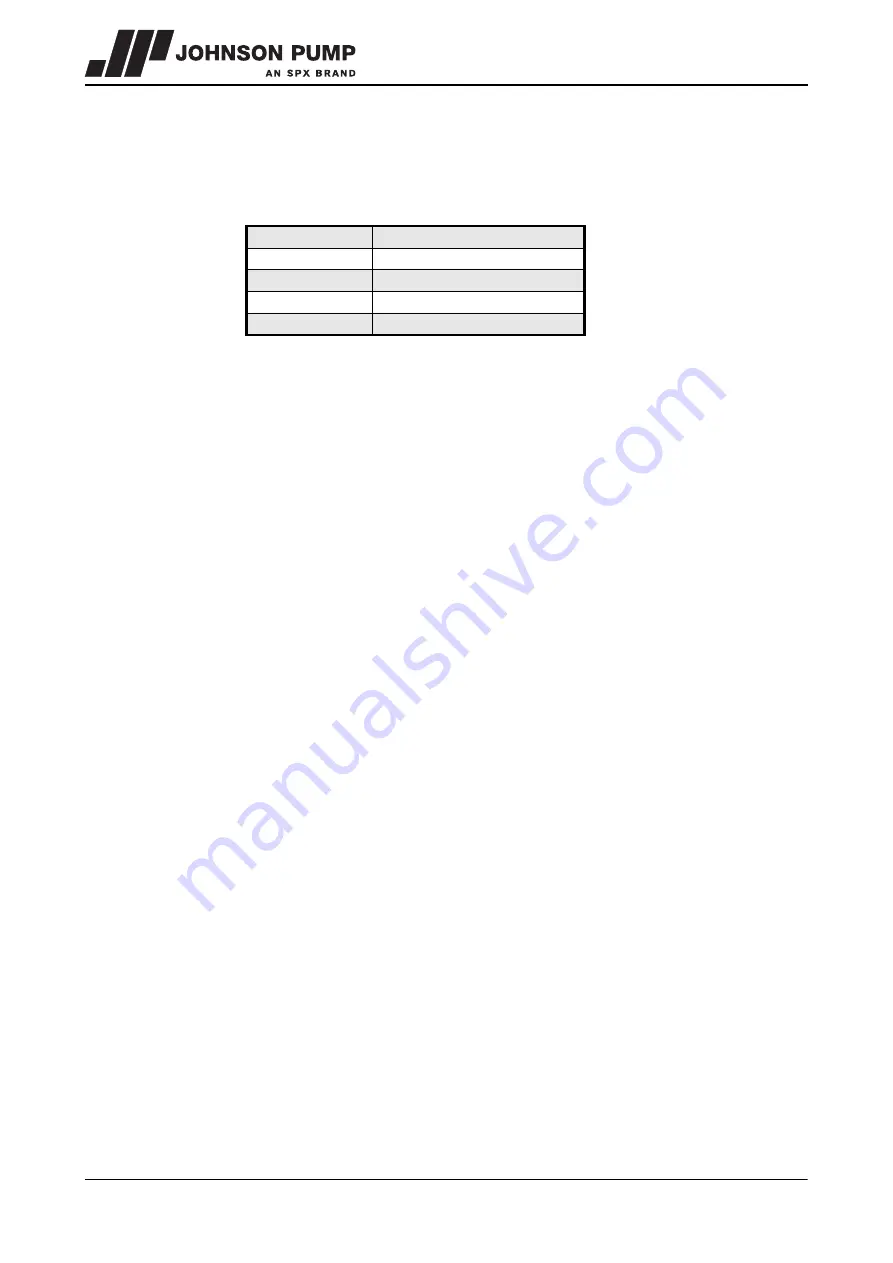
14
General
CV/EN (1009) 5.3
2.3
Serial number
Serial number of the pump or pump unit are shown on the name plate off the pump and
on the label on the cover of this manual.
2.4
Applications
• In general, this pump can be used for thin, clean or slightly polluted liquids. These
liquids should not affect the pump materials.
• The maximum allowed system pressure and temperature and the maximum speed
depend on the pump type and the pump construction. For relevant data see paragraph
2.6 "Application area".
• Further details about the application possibilities of your specific pump are mentioned
in the order confirmation and/or in the data sheet enclosed with the delivery.
• Do not use the pump for purposes other than those for which it is delivered without
prior consultation with your supplier.
Using a pump in a system or under system conditions (liquid, working
pressure, temperature, etc.) for which it has not been designed may hazard
the user!
2.5
Construction
The pump has a modular design. The main components are:
• Pump casing/impeller/suction bend
• Shaft sealing
• Self-priming unit
• Bearing
• Lantern construction
• Foot pads
The pumps are available in 3 bearing groups, meaning that bearing and shaft sealing are
divided into 3 groups. Furthermore, the pumps have been standardized in 5 groups
featuring the same connection for pump cover and bearing pedestal, depending on the
nominal impeller diameters. The pump covers are clamped between the pump casing
and bearing bracket.
2.5.1
Pump casing/impeller/suction bend
These are the parts that get into contact with the pumped liquid. For each individual
pump type there is only one construction of the pump casing and the impeller. The pump
casing and the suction bend are available in cast iron and in bronze, the impeller in cast
iron, bronze and aluminium bronze. The pump shaft is available in alloyed and stainless
steel. With the available materials the pumps can be supplied in a construction suitable
to pump sea water. The square suction bend has been designed in such a way that
resistance is low an that all the same a low position of the pump in relation to the floor is
possible. The pump types 200-200, 250B-315 have a fabricated suction bend. The
suction bend can be mounted in different positions in relation to the discharge flange.
This offers a large number of mounting possibilities.
Example:
01-1000675A
01
year of manufacture
100067
unique number
5
number of pumps
A
pump with motor
B
pump with free shaft end
Содержание Johnson Pump CombiPrime V
Страница 3: ...2 EC EN 1001 5 1...
Страница 5: ...4 CV EN 1009 5 3...
Страница 9: ...8 CV EN 1009 5 3...
Страница 49: ...48 Disassembly and assembly CV EN 1009 5 3...
Страница 63: ...62 Dimensions CV EN 1009 5 3...
Страница 65: ...64 Parts CV EN 1009 5 3 9 2 Pump 9 2 1 Sectional drawing Figure 29 Sectional drawing...
Страница 81: ...80 Technical data CV EN 1009 5 3...
Страница 85: ...84 ORDFORM 0804 3 1 EN...