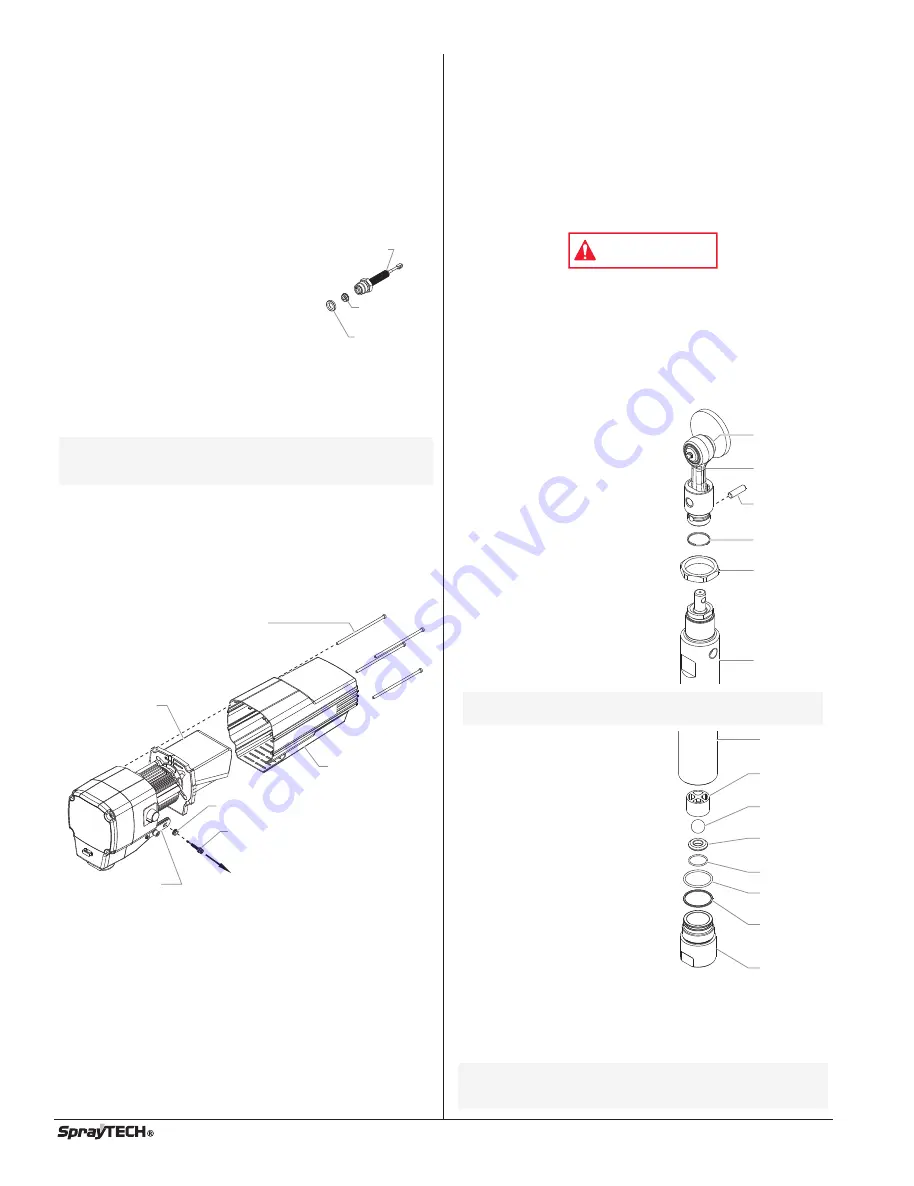
Replacing the Transducer
1. Perform the Pressure Relief Procedure and unplug the
unit.
2. Turn the pressure control knob to the “1” or “2” position to
make sure the power supply has discharged.
3. Loosen and remove the four motor shroud screws.
Remove the motor shroud.
4. At the electronic control assembly, disconnect the black
wire coming from the transducer.
5. Pull the grommet out of the mounting plate and slide it up
the shaft of the transducer until it is clear of the mounting
plate.
6. Using a wrench, loosen and remove
the transducer from the filter housing.
Carefully thread the transducer wire
out through the mounting plate.
Replace the transducer cap and inner
seal, if damaged.
7. Slide the grommet off of the old
transducer and onto the new
transducer.
8. Thread the new transducer wire through the mounting
plate and up to the electronic control assembly.
9. Thread the new transducer into the filter housing and
tighten securely with a wrench.
10. Push the grommet into the mounting plate.
11. Connect the transducer wire to the electronic control
assembly (refer to the electrical schematic in the Parts List
section of this manual).
12. Slide the motor shroud over the motor.
13. Secure the motor shroud with the four motor shroud
screws.
Motor Shroud
Transducer
Grommet
Motor Shroud Screws
Electronic
Control
Assembly
Mounting Plate
To
Filter
NOTE: Make sure the transducer cap and inner seal on
the transducer are in place before threading the
transducer into the filter housing.
Transducer
Transducer
Cap
Inner Seal
10
© SprayTECH. All rights reserved.
Servicing the Fluid Section
Use the following procedures to service the valves and repack
the fluid section.
1. Loosen and remove the four front cover screws. Remove
the front cover.
2. Position the crankshaft/slider assembly at the bottom,
dead-center of its stroke so that the connecting pin and
retaining ring are visible below the slider assembly. This
is done by turning the sprayer on and off in short bursts
until the connecting pin is visible below the slider housing.
3. Turn off and unplug the unit.
Before proceeding, follow the Pressure Relief Procedure
outlined previously in this manual. Additionally, follow all
other warnings to reduce the risk of an injection injury,
injury from moving parts or electric shock. Always unplug
the sprayer before servicing!
4. Remove the return hose from the clamp on the siphon tube.
5. Unscrew the siphon tube/suction set from the inlet valve.
6. Loosen and remove the high-pressure hose from the
nipple on the back of the cylinder of the fluid section.
7. Slide the retaining ring up on
the slider assembly to expose
the connecting pin.
8. Push the connecting pin
forward through the slider
assembly and piston. The
connecting pin will fall into a
recessed area of the gear box
housing where it can be
retrieved.
9. Using a wrench, turn the jam
nut counterclockwise to loosen
it from the gear box housing.
10. Turn the fluid section
counterclockwise to remove it
from the gear box housing.
11. Place the fluid section cylinder
upright in a vise by clamping on
the wrench flats.
12. Loosen and remove the inlet
valve housing from the
cylinder.
13. Remove the inlet valve cage,
inlet valve ball, inlet valve seat,
and o-ring from the inlet valve.
14. Clean out any debris in the
inlet valve housing and
examine the housing and the
inlet valve seat. If the seat is
damaged, reverse or replace
the seat.
15. Using a wrench, remove the
upper seal retainer.
16. Slide the piston rod out through
the bottom of the cylinder.
17. Inspect the piston rod for wear
and replace if necessary.
18. Remove the upper packing assembly from the top of the
cylinder.
19. Remove the adapter and lower packing assembly from the
bottom of the cylinder.
NOTE: Be careful not to scratch, score, or otherwise
damage the cylinder during removal of the
packings.
Inlet Valve
Housing
Viton
O-Ring
O-ring
PTFE
Back-Up
Ring
Inlet Valve
Seat
Inlet Valve
Ball
Inlet Valve
Cage
Cylinder
NOTE: Do not over-tighten the vise. Damage to the
cylinder may occur.
Retaining
Ring
Connecting
Pin
Slider
Assembly
Crankshaft
Jam Nut
Cylinder
WARNING
All manuals and user guides at all-guides.com