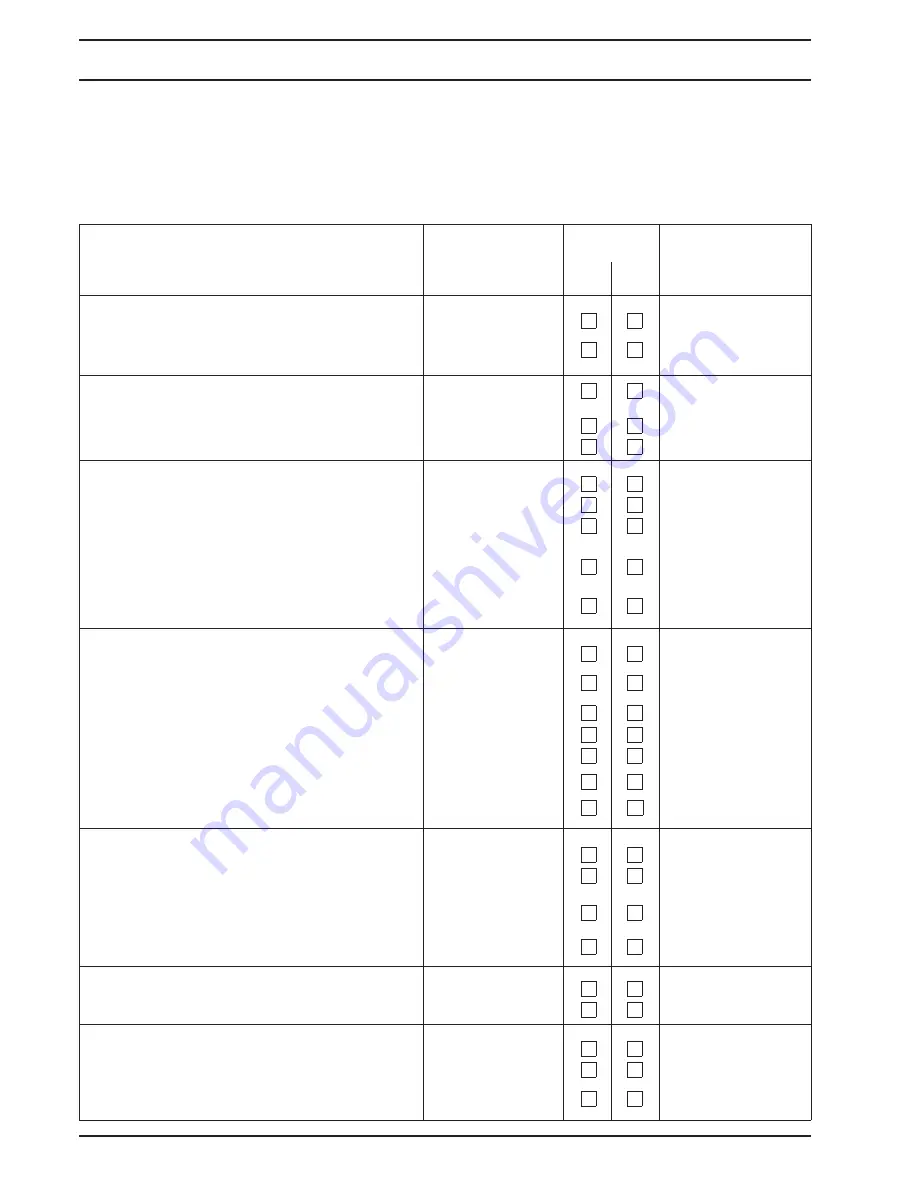
S
o
m
r
e
h
T
x
i
d
n
e
p
p
A
A
160/230/300/350/400
A-2
Periodic heater maintenance
The heater should be inspected in periodic time intervals,
latest at the beginning of the heating period (time of
increased heater usage due to present weather
conditions).
The maintenance intervals mentioned below refer to
common applications and requi rements in omnibuses. If
heaters should be used in other vehicles and/or
applications, the maintenance intervals may be shortened
or extended.
In such cases please contact your dedicated Spheros
partner for further information.
n
o
i
t
c
e
p
s
n
I
n
o
i
t
a
m
r
o
f
n
i
t
n
a
t
r
o
p
m
I
s
e
i
t
i
v
i
t
c
a
e
c
n
a
n
e
t
n
i
a
m
/
n
o
i
t
c
e
p
s
n
I
result
Measured values
Executed
repairs
OK
not
OK
1. Electrical connections
a) Loosen electrical plug connection s to the wiring harness, inspect for
oxidation, spray and reconnect after completing point 5.
b) Inspect electrical fuses for oxidation and/or contact
resistances.
Use suitable contact
spray, e.g. special
contact spray (order no.
101322).
2. Heat exchanger
a) Inspect for dark burn marks on the paint (local over-
heating).
b) Inspect for leak marks.
c) Clean heater exterior and interior.
Determine overheating
cause as needed (e.g.
water circulation system);
check overheat
temperature limiter.
3. Fuel system
a) Inspect fuel lines an d connections for leakage.
b) Replace fuel filter insert with gasket.
c) If available, open fuel shut-off valves
d) Fuel pump and fuel lines.
NOTE:
Observe technical information if bio diesel or FAME
is used!
e) Replace fuel screen with gasket in the pump.
Ensure connections to
fuel flow and return lines
are sealed tight!
Re-tighten screw
connections and hose
clamps.
Replace pump and pipes
every 5 years.
Observe technical bio
diesel / FAME
information!
4. Burner head
a) Inspect combustion air intake opening for clear passage.
b) Inspect hood for damage.
c) Inspect housing interior for fuel accumulations caused by leaking.
d) Clean flame detector inspection glass.
e) Inspect condition of the ignition electrodes.
f)
Replace atomiser nozzle.
g) Check nut-and-washer assemblies M8 (2ea) for burner attachment for
tight fit, torque to 7.5 +1 Nm.
Replace damaged hood
Replace bent electrodes.
In case of coke build-up
shorten fuel filter
replacement interval.
5. Exhaust system
a) Inspect exhaust line for cl ear passage, clean as needed.
b) Remove combustion chamber from heat exchanger,
inspect both parts for damage and contamination, clean and
replace as needed.
c) Insert combustion chamber and mount burner head. Ensure tight
connection to heat exchanger.
d) Connect electrical plug contacts.
6. Water system
a) Clean filter insert, if available.
c) Open water shut-off valves, if available.
7. Functional check
a) Open shut-off valve of the return line, if available.
b) Check heater functionality.
c) Check for smoke development duri
ng run-down, replace nozzle as
needed.
after at least 10 min.
heater operation.
Содержание Thermo S 160
Страница 2: ......
Страница 6: ...1 Introduction Thermo S 160 230 300 350 400 4...
Страница 11: ...S o m r e h T n o i t c u d o r t n I 1 160 230 300 350 400 105...
Страница 49: ...5 Troubleshooting and error correction Thermo S 160 230 300 350 400 520...
Страница 55: ...r e h T s m a r g a i d c i t a m e h c S 6 mo S 160 230 300 350 400 606...
Страница 71: ...9 Modifications and retrofits Thermo S 160 230 300 350 400 902...
Страница 73: ...10 Packing storage shipping Thermo S 160 230 300 350 400 1002 Empty page for notes...
Страница 74: ...x i d n e p p A A 0 0 4 0 5 3 0 0 3 0 3 2 0 6 1 S o m r e h T A 1 Appendix A Periodic maintenance...