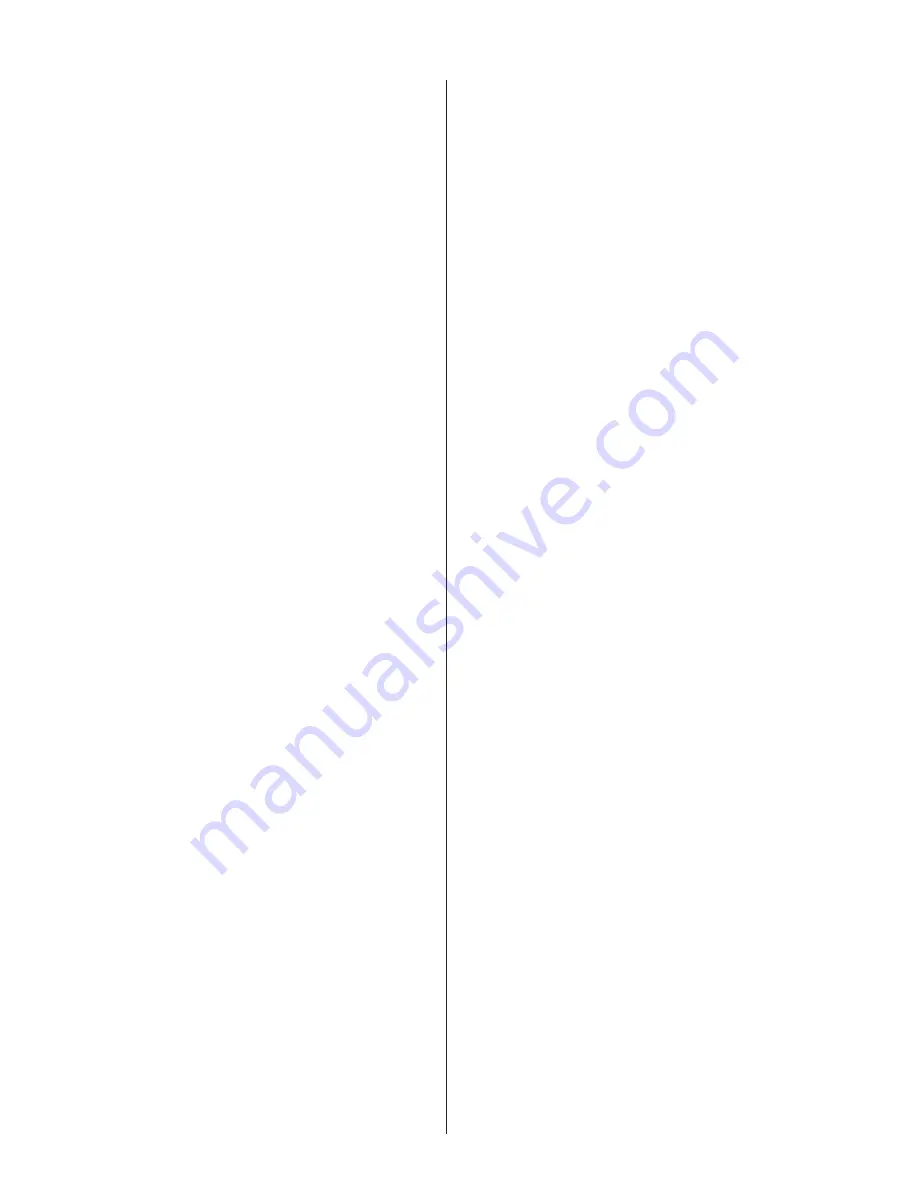
16
Panther HIP-PAC
b. Composite Cylinders
Ensure that no more than three years have elapsed
since the last hydrostatic test has been performed
for the 3000 psig, hoop wrapped cylinder and five
years for the 4500 psig fully wrapped fiber cylinder,
and that the cylinder is less than 15 years old. In-
spect the exterior of the cylinder for dents, gouges,
or cuts which have penetrated and caused separa-
tion or unraveling of the composite overwrap. Watch
for evidence of exposure to high temperature, such
as darkened or blistered paint, charred overwrap or
decals, melted or distorted gauge lens, etc.
c. Cylinder Valve
The cylinder valve should also be examined for ob-
vious external damage such as a deformed hand-
wheel, inaccurate or inoperative pressure indicator,
damaged threads on the outlet connection, or other
evidence of impact or exposure to extreme heat.
If internal contamination is suspected, remove the
cylinder valve and inspect the interior of the cylin-
der. The cylinder valve overhaul cycle should be as
follows. For steel, all aluminum, or fully wrapped
carbon fiber cylinders, overhaul the valve at every
hydrostatic retest (5 year cycle). For hoop wrapped
cylinders, overhaul the valve at every other hydro-
static retest (6 year cycle).
d. Additional Information
i. Additional information on cylinder inspection
and maintenance can be found in CGA pamphlet
C-6, “Standards for Visual Inspection of Com-
pressed Gas Cylinders,” CGA pamphlet C-6.1,
“Visual Inspection of High Pressure Aluminum
Cylinders,” or CGA pamphlet C-6.2, “Guidelines
for Visual Inspection and Requalification of Fiber
Reinforced High Pressure Cylinders,” available
from the Compressed Gas Association, Inc. If
there is any doubt about the suitability of a cylin-
der to recharge, it should be returned to a certi-
fied hydrostatic retest facility for expert examina
-
tion and retesting.
ii. A comprehensive listing of all licensed hydro-
static test stations is available from the Depart-
ment of Transportation.
2. Filling Procedure
a. Air Purity
Unless safety and health codes in your area specify
otherwise, air cylinders should be refilled with com
-
pressed air meeting the purity requirements for
Type 1, Grade D Gaseous Air as specified by the
Compressed Gas Association Commodity Specifi
-
cation for Air, publication G-7.1. The moisture con-
tent, expressed as dewpoint, shall be maintained
at -65°F (-53.9°C) or lower, or less than 24.0 ppm
by volume moisture content. UNDER NO CIRCUM-
STANCES SHALL AN AIR CYLINDER BE FILLED
OR PARTIALLY FILLED WITH OXYGEN.
b. Maximum Fill Pressure
Determine the service pressure of the cylinder prior
to filling. Composite and aluminum cylinders may
be filled only to the service pressure indicated on
the cylinder label. Composite and aluminum cylin-
ders must never be filled to a pressure greater than
the marked service pressure.
c. Filling Procedure
i. The fill station must be constructed and
equipped in accordance with applicable state in-
dustrial safety codes.
ii. The cylinder may be partially immersed (DO
NOT submerge the cylinder valve) in a water
bath to minimize the temperature rise that oc-
curs as the cylinder is filled. The fill hose should
be equipped with a restraining cable to prevent
uncontrolled “whipping” in case of hose failure.
iii. After connecting the fill hose, open the cylin
-
der valve fully. A separate metering valve must
be used to control the fill rate. Fill the cylinder
slowly, at a rate not exceeding 500 psig per min-
ute. (Use caution if faster recharging rates are
used.) After the initial filling, allow the cylinder
to cool to room temperature, then “top off” the
cylinder to achieve full service pressure.
iv. Use particular care to ensure that an air cyl-
inder is never connected to a source capable
of supplying air at a pressure greater than the
maximum service pressure of that cylinder.
v. Close the cylinder valve when the cylinder is
full.
vi. Slowly bleed pressure from the filling lines.
vii. Disconnect the filling line.
viii. Let the cylinder cool and check the gauge
reading. Top off if necessary.
d. Storage
Air cylinders should be recharged as soon as prac-
tical after use. Cylinders should not be stored par-
tially charged, for two reasons:
i. If used without recharge, the service duration
of the apparatus is reduced.
ii. The safety relief device is designed specifi
-
cally to protect a fully charged cylinder from the
effects of a fire.
For maximum safety, the cylinders should be stored
fully charged.
If the cylinder is stored empty and the valve is in-
advertently left open, humid atmospheric air may
enter the cylinder and result in interior corrosion.
If a HIP-PAC is to be maintained in “standby” mode,
i.e., available for immediate emergency usage, the
cylinder pressure gauge should be checked at least
once a month to assure that the cylinder is charged
to full service pressure. Place the cylinder in a suit-
able safety sleeve or filling area.