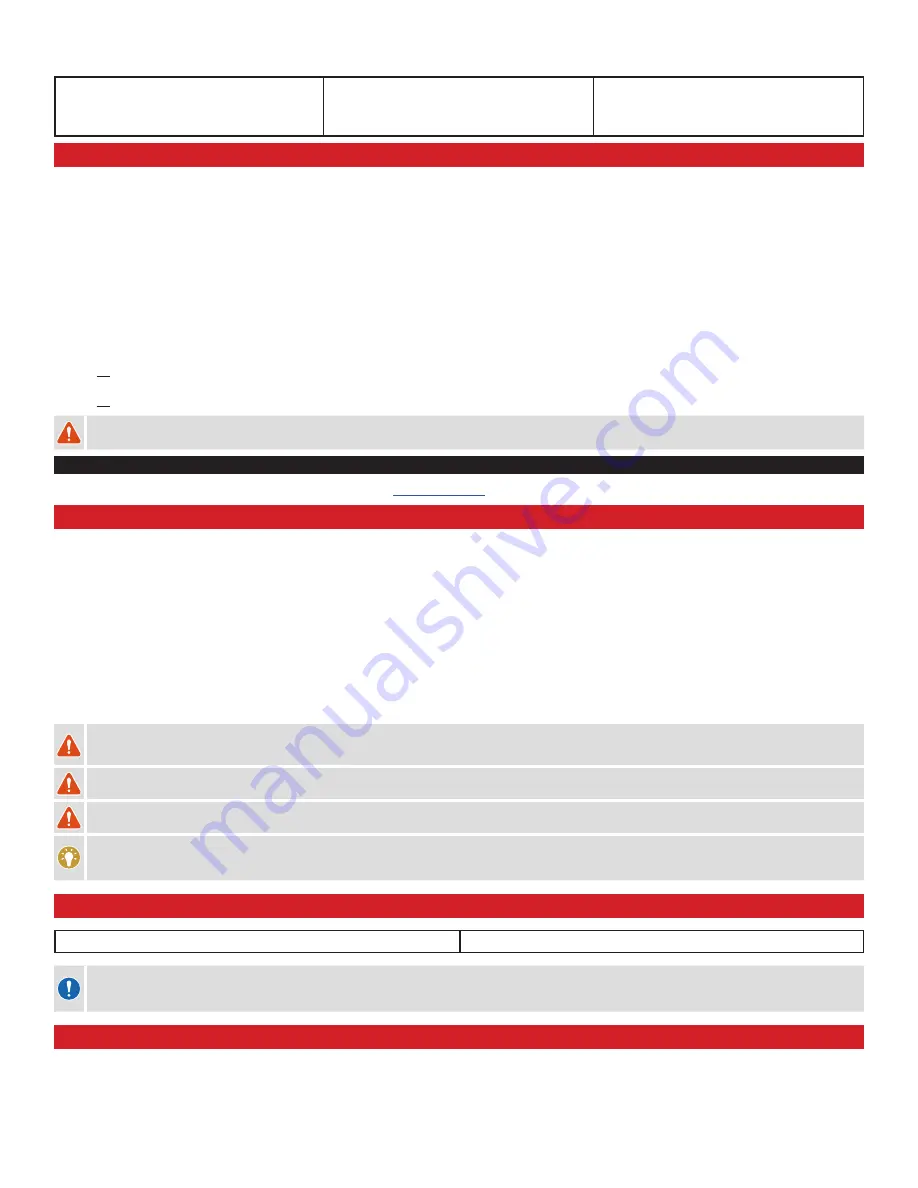
2
The following tools are required for assembly of this product:
2, 2.5, 3, 4, 5mm Allen keys
3, 4, 5mm socket Allen keys (3/8” socket)
Long 4mm Allen key bit for Roubaix/Ruby (S175300015)
Torque wrench (3/8” socket)
Cable and housing cutters
High-quality grease
Blue threadlocker (Loctite 242)
GENERAL NOTES ABOUT MAINTENANCE
The Specialized Diverge are high performance bicycles. All regular maintenance, troubleshooting, repair and parts replacement must be performed by an Authorized Specialized Retailer. For general
information regarding maintenance of your bicycle, please refer to the Owner’s Manual. In addition, routinely perform a mechanical safety check before each ride, as described in the Owner’s Manual.
•
Great care should be taken to not damage carbon fiber or composite material. Any damage may result in a loss of structural integrity, which may result in a catastrophic failure. This damage may or may not be
visible in inspection. Before each ride, and after any crash, you should carefully inspect your bicycle for any fraying, gouging, scratches through the paint, chipping, bending, or any other signs of damage. Do not
ride if your bicycle shows any of these signs. After any crash, and before you ride any further, take your bicycle to an Authorized Specialized Retailer for a complete inspection.
•
While riding, listen for any creaks, as a creak can be a sign of a problem with one or more components. Periodically examine all surfaces in bright sunlight to check for any small hairline cracks or fatigue at stress points, such as
welds, seams, holes, and points of contact with other parts. If you hear any creaks, see signs of excessive wear, discover any cracks, no matter how small, or any damage to the bicycle, immediately stop riding the bicycle and
have it inspected by your Authorized Specialized Retailer.
•
Lifespan and the type and frequency of maintenance depends on many factors, such as frequency and type of use, rider weight, riding conditions and/or impacts. Exposure to harsh elements, especially salty air
(such as riding near the ocean or in the winter), can result in galvanic corrosion of components such as the crank spindle and bolts, which can accelerate wear and shorten the lifespan. Dirt can also accelerate
wear of surfaces and bearings. The surfaces of the bicycle should be cleaned before each ride. The bicycle should also be maintained regularly by an Authorized Specialized Retailer, which means it should be
cleaned, inspected for signs of corrosion and/or cracks and lubricated. If you notice any signs of corrosion or cracking on the frame or any component, the affected item must be replaced.
•
Regularly clean and lubricate the drivetrain according to the drivetrain manufacturer’s instructions.
•
Do
not
use a high pressure water spray directly on the bearings. Even water from a garden hose can penetrate bearing seals and crank interfaces, which can result in increased bearing and crank wear, which can
affect the normal function of the bearings. Use a clean, damp cloth and bicycle cleaning agents for cleaning.
•
Do
not
expose the bicycle to prolonged direct sunlight or excessive heat, such as inside a car parked in the sun or near a heat source such as a radiator.
WARNING! Failure to follow the instructions in this section may result in damage to the components on your bicycle and will void your warranty, but, most importantly, may result
in serious personal injury or death. If your bicycle exhibits any signs of damage, do not use it and immediately bring it to your Authorized Specialized Retailer for inspection.
WARRANTY
Please refer to the written warranty provisions provided with your bicycle, or visit
. A copy is also available at your Authorized Specialized Retailer.
INSTALLING THE SEATPOST
Diverge frames have a 27.2mm seatpost diameter and require that the seatpost have a tolerance of 27.08mm to 27.25mm.
SEATPOST MINIMUM INSERTION:
To prevent damage to the frame and/or seatpost, it is important to have a minimum amount of seatpost insertion in the seat tube. This minimum insertion must meet the following requirements:
The seatpost must be inserted into the frame deep enough so the minimum insertion/maximum extension (min/max) mark on the seatpost is not visible.
The seatpost must also be inserted into the seat tube deep enough to be visible through the sight hole, or if no sight hole is present, the insertion must meet or exceed the 90mm minimum measured
insertion depth required by the frame.
If the seatpost and frame minimum insertion requirements differ from each other, always use the longer minimum insertion. For example, if the frame requires 90mm, but the seatpost
requires 100mm, then 100mm is the minimum insertion required.
If the seatpost is at the min/max mark and the seatpost is not visible through the sight hole or does not meet or exceed the minimum measured insertion depth of the frame, the seatpost is not inserted
deeply enough into the seat tube and should be lowered until it can be seen through the sight hole. This may result in the saddle being too low. If so, the seatpost must be replaced with a longer one.
WARNING! Failure to follow the seatpost and frame minimum insertion requirements may result in damage to the frame and/or seatpost, which could cause you to lose control and fall.
If the seatpost is cut short, the min/max mark on the seatpost may no longer be accurate. Before cutting the seatpost, note the min/max depth required by the seatpost manufacturer.
WARNING! For general instructions regarding the installation of the seatpost, refer to the appropriate section in the Owner’s Manual. Riding with an improperly tightened
seatpost can allow the saddle to turn or move and cause you to lose control and fall.
WARNING! Inspect the seatpost and seat tube to ensure that there are no burrs or sharp edges. Remove any burrs or sharp edges using fine grit sandpaper.
Do not apply grease to the contact surfaces between the seatpost and the seat tube. Grease reduces the friction, which is critical to proper seatpost grip. Specialized
recommends the application of carbon assembly compound (fiber paste), which can increase friction between carbon surfaces. Please visit your Specialized Authorized
Retailer for additional information.
INSTALLING THE BOTTOM BRACKET
DIVERGE CARBON:
BB386EVO bottom bracket shell
DIVERGE ALLOY:
BSA Threaded bottom bracket shell
CAUTION: Do not face or ream the carbon bottom bracket shell! This can prevent proper installation of the crank. Your Specialized frame does not require any bottom
bracket shell pre-installation preparation, as all surfaces have been precisely manufactured to specific tolerances at the factory for proper interface with BB386EVO
compatible bottom brackets and cranksets. Please refer to the manufacturer instructions for crank and bottom bracket installation.
INSTALLING A RACK
Alloy frames are equipped with a seat collar with rack mounts built into the collar. This collar is available separately for carbon frames.
Rear rack:
For best fit results, we recommend the use of the Specialized Elite Rear Rack.
Front rack:
Any low rider style front rack that bolts to the fork leg and dropout rack mounts.
For installation specifics, please refer to the rack manufacturer’s instructions.