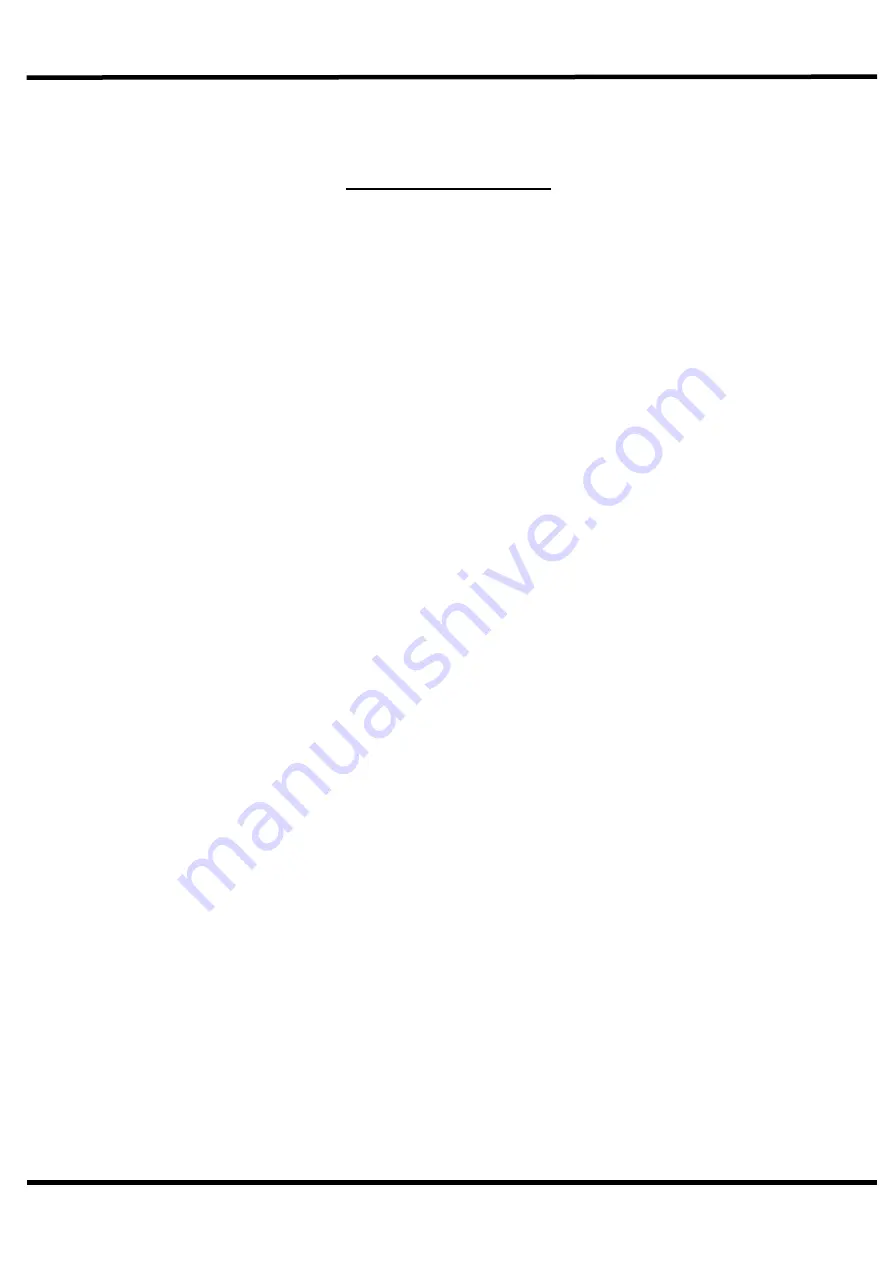
Spearhead Rollicut
500 & 600
3
WARRANTY POLICY
WARRANTY REGISTRATION
All machines must be registered, by the selling dealer with Spearhead Machinery Ltd, before
delivery to the end user. On receipt of the goods it is the buyer’s responsibility to check that the
Verification of Warranty Registration in the Operator’s Manual has been completed by the selling
dealer.
1. LIMITED
WARRANTIES
1.01. All machines supplied by Spearhead Machinery Limited are warranted to be free from defects in
material and workmanship from the date of sale to the original purchaser for a period of 12
months, unless a different period is specified.
1.02. All spare parts supplied by Spearhead Machinery Limited are warranted to be free from defects in
material and workmanship from the date of sale to the original purchaser for a period of 6
months.
1.03. The manufacturer will replace or repair for the purchaser any part or parts found, upon
examination at its factory, to be defective under normal use and service due to defects in material
or workmanship. Returned parts must be complete and unexamined.
1.04. This warranty does not apply to any part of the goods, which has been subjected to improper or
abnormal use, negligence, alteration, modification, fitment of non-genuine parts, accident
damage, or damage resulting from contact with overhead power lines, damage caused by foreign
objects (e.g. stones, iron, material other than vegetation), failure due to lack of maintenance, use
of incorrect oil or lubricants, contamination of the oil, or which has served its normal life. This
warranty does not apply to any expendable items such as blades, flails, bushes, belts, flap kits,
skids, shields, guards, wear pads or pneumatic tyres.
1.05. Temporary repairs and consequential loss - i.e. oil, downtime and associated parts are
specifically excluded from the warranty.
1.06. Warranty on hoses is limited to 12 months and does not include hoses which have suffered
external damage. Only complete hoses may be returned under warranty, any which have been
cut or repaired will be rejected.
1.07. Machines must be repaired immediately a problem arises. Continued use of the machine after a
problem has occurred can result in further component failures, for which Spearhead Machinery
Ltd cannot be held liable, and may have safety implications.
1.08. Except as provided herein, no employee, agent, dealer or other person is authorised to give any
warranties of any nature on behalf of Spearhead Machinery Ltd.
1.09. For machine warranty periods in excess of 12 months the following additional exclusions shall
apply:
1.09.1. Hoses, external seals, exposed pipes and hydraulic tank breathers.
1.09.2. Filters
1.09.3. Rubber mountings
1.09.4. External electric wiring.
1.09.5. Labour and mileage costs.
1.10. All service work, particularly filter changes, must be carried out in accordance with the
manufacturer’s service schedule. Failure to comply will invalidate the warranty. In the event of a
claim, proof of the service work being carried out may be required.
NB Warranty cover will be invalid if any non-genuine parts have been fitted or used. Use of non-
genuine parts may seriously affect the machine’s performance and safety. Spearhead Machinery
Ltd cannot be held responsible for any failures or safety implications that arise due to the use of
non-genuine parts.
Содержание Rollicut 500
Страница 1: ...Spearhead Rollicut 500 600 1 Rollicut 500 600 Rotary Mower Edition 1 0 January 2015 Part No 8999092...
Страница 10: ...Spearhead Rollicut 500 600 10 Safety Decal Location B E F B E F B E F D G A C H...
Страница 12: ...Spearhead Rollicut 500 600 12 Machine Specification...
Страница 38: ...Spearhead Rollicut 500 600 38 Gearbox Before first use check gearbox oil level thereafter check every 8 hours...
Страница 45: ...Spearhead Rollicut 500 600 45...